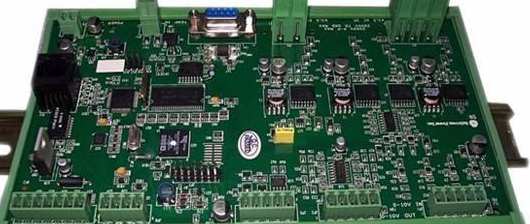
The basic operating procedures and processes of the dynamic SMT mounter
For our work or safety issues, when using smt SMT machine in the production process, yoPCB boardu need to understand your workflow and production process, not only can we be familiar with the operation of the use process, rapid production, you can also have a certain understanding of the protection of their own safety, then the automatic laying machine work steps and process do you understand? Let's take a look
1. Before using the automatic smt mounter, we need to provide a basic board mounting (called ) for the machine and perform fixed operation in the system. Then we can perform corresponding laying operations according to the specific Settings of the smt machine
2, we provide the board for the machine, but also need to provide the corresponding installation components, the storage location of the parts is called the feeder, we will reasonably install the feeder on the bracket, and then provide drawings and installation coordinates of the installation head through the positioning system.
3. We can operate smt machines to absorb and install components. System parameters and optical detector information can detect current absorption and installation to ensure our installation accuracy.
4. After the laying machine absorbs components through each laying head, it will be laid in the appropriate position to set up the system. We can use the mount head to mount the prepared component anywhere on the specified PCB.
5. After the first assembly of the PCB board is completed, the system will repeat the production according to the set schedule, otherwise the machine will stop after the completion of the set schedule and wait for the PCB board to be shipped. In this way, the full automatic assembly of the entire smt machine will be completed.https://www.kingfordpcb.com/yuan.php
Many laying machine processing plants or a generation of processing plants do not pay attention to the production of SMT machines, a good SMT production environment is very important, because employees want to have a clean and comfortable office, can improve work efficiency, in addition, a good production environment will also improve the productivity of the laying machine, this is why? Let's take a look at what are the requirements of SMT processing equipment and production processing? .
First of all, the first is the service life of the laying machine, the SMT machine is a relatively high-precision intelligent machine, the production environment of our workshop has certain requirements for temperature, humidity, pressure, etc., there are corresponding requirements, if it does not meet the requirements, it will improve the safety risks, the machine life caused by shrinkage, so we must ensure the following normal setting environment
Voltage: Voltage is a necessary condition for starting and using the chip machine, the stability of the voltage must be ensured, if it does not meet the requirements, it is necessary to configure a regulated power supply
Temperature: Temperature is the service life environment of the SMT machine. Normally, we can live at room temperature, between 16-27 degrees, neither too cold nor too hot. If the temperature is too low, it may damage the machine.
Environment: The environment is also the living space of SMD machines, and the workshop is kept clean and hygienic at all times, free of dust and corrosive gases, and air circulation must be ensured
Static electricity: It is easy to generate static electricity in the workshop, so we need to install anti-static devices on site. Avoid machine damage caused by static electricity
The following machines are required for PCB board:
1, solder paste printing machine
2, SMT machine 3, reflow welding 4, AOI detector 5, parts clipper machine 6, wave welding