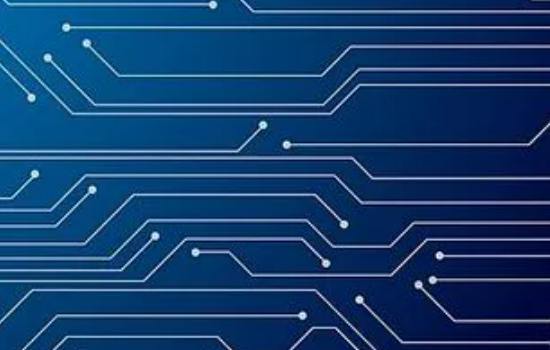
New product introduction (NPI) and getting your design ready for full production is an exciting, risky, and complex process. Most new products start with a working prototype, which manufacturers can test and refine over and over again to achieve the most optimized final product. But fine-tuned prototypes are a far cry from something that can be mass-produced in most cases. This is almost always true when it comes to electronics.
Of course, it's not impossible to launch new products and get them ready for mass production, but it does require research, design tweaks, flexibility, strategic partnerships and a lot of patience. NPI is also a must because even the most trusted and stable product lines eventually need upgrades and overhauls. This cannot be done overnight, especially when it comes to PCB assembly changes. There are many considerations and all the bases need to be covered before a successful application can be made. Especially in the current parts shortage, substitution and crossover market.
NPI is not just a concept; This is a process that includes everything from conceptualization, PCB layout, developing, building, and improving prototypes, all the way to launch the product. During this process, many considerations enter into the formula necessary for a successful launch.
Prototype stage
Turning ideas into physical representations, assembling them into PCBS and making them work is just the tip of the iceberg. No one ever gets the design right on the first try, or even in the first few iterations. It takes many hours of testing and refinement to finalize a quality product.
This requires prototyping, an early incarnation of the product for testing and quality assurance. Prototyping can be expensive, but it's essential. Imagine putting together a PCB for a new product, assuming all the parts are in place, and then putting it into mass production without any confirmation that its problems and defects are being fixed. This is a sure-fire way to lose a lot of money and time.
By their nature, prototypes are elements of the NPI testing phase and are rarely ready for mass production. For example, a prototype may not provide ideal positioning for components on a circuit board, resulting in a layout that requires complete remapping. Sometimes these parts are placed in a way that does not thoroughly test their viability, leading to necessary layout overhauls. When defects are found in the prototype, they also need to be processed, which requires further refinement of the PCB and its components.
New product introduction (NPI) process
Once the prototype is confidently in a good place, the PCB manufacturer needs to start thinking about all the elements needed to put the product into mass production. Before that, many considerations involve all aspects of the process that need to be considered, such as where production will take place,
High quality NPI processes force manufacturers to focus on the basic aspects of production. But every process of launching a new product must begin with conception and preparation.
Concept, preparation, and goal setting
At this stage, the manufacturer must accumulate all the necessary research data that shows what components are needed to produce the PCB, what functions it should include, what aspects are essential, what options are available, and what can be used to obtain materials, as well as to determine what constitutes a "quality" version of the product.
feasibility
In order for PCB products to be marketable, the concept must be workable. This requires evaluating and analyzing financial feasibility, discussing preliminary design, and estimating time.
Product development
The concept of a product and its feasibility is the key to figuring it out on paper, but whether it can be developed and manufactured is another matter. Working with the CM (contract manufacturer), this phase of the NPI needs to figure out how best to put the product together. This involves reviewing, gathering lists of materials, ensuring that appropriate components are available, workable combinations, establishing guidelines, etc.
test
Once a product is developed and manufactured, it needs to be tested. It must first be determined whether the product meets the intended purpose for which it was designed. If so, testing needs to verify that there are no obvious weaknesses in the functionality or performance of the product. If any problems are found, they need to be analyzed and appropriate corrective actions taken to improve efficiency. This phase involves prototyping to identify and isolate areas for improvement.
execute
The next stage is product implementation. At this stage, product documentation is collected and compiled, including all manuals, catalogs, and related product documentation.
evaluation
No product is ever perfect, so there is always a way to make PCB products better. However, much of this evaluation will require comments and feedback from some initial users of the product. This is a form of quality assurance because a group of users needs to thoroughly use the product and provide feedback.