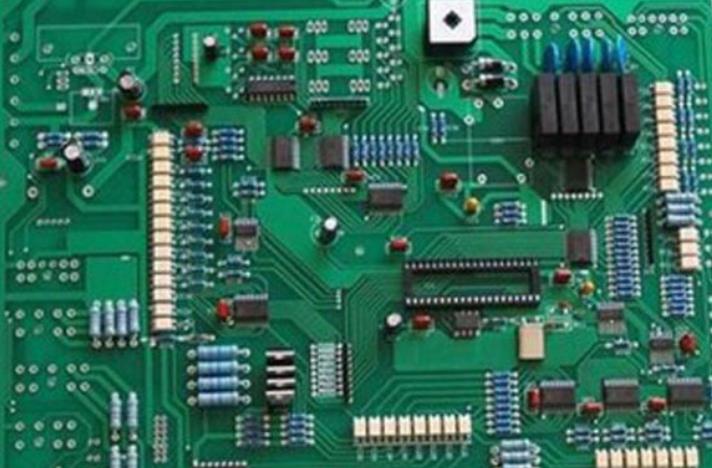
SMT Grape Ball and Patch Machine Workflow
Grape ball phenomenon usually refers to the phenomenon that solder pastes are not completely melted and welded together in the reflow process, but are gathered into a single tin bead and stacked together to form a grape bunch
Cause SMT grape ball phenomenon
1. Solder paste is wet and oxidized
Water oxidation of solder paste is the main reason for grape ball phenomenon. The oxidation of solder paste can be divided into many categories, such as careless operation of operators, expired solder paste or improper storage, re heating/poor mixing of solder paste, which causes the solder paste to absorb water and moisture. This may be the cause of solder paste oxidation. One of the possible reasons is that some steel plates (meshes) are not completely dry after solvent cleaning.
2. Solder paste and flux volatilization
Circuit board
The flux in the solder paste is an important factor affecting the melting of the solder paste. The purpose of flux is to remove oxides on the metal surface and reduce the surface of solder metal. In fact, there is another purpose to protect tin powder. Avoid contact with air. If the flux volatilizes in advance, the effect of removing oxides on the metal surface cannot be achieved. In this case, the solder paste must be used up within a period of time after unpacking, otherwise the flux will volatilize and the solder paste will change. In addition, if the preheating area in reflow soldering is too long, the flux will evaporate excessively, and the possibility of grape ball phenomenon is greater.
3. Insufficient return temperature
When the reflow temperature is not enough to provide the condition for complete melting of solder paste, solder paste may also have grape ball phenomenon If the amount of solder to be printed is small, the chance of solder paste oxidation and flux volatilization will be higher This is because the smaller the amount of solder paste printed, the higher the ratio of solder paste to air contact, which is more likely to cause grape balls This is why component 0201 is more prone to grape ball phenomenon than component 0603
Solutions to improve the phenomenon of SMT grape balls:
1. Use a more active solder paste.
2. Increase the amount of solder paste printing.
3. The width or thickness of the steel plate opening is added to increase the printing amount of flux and solder paste, and improve the oxidation resistance of solder paste.
4. Shorten the preheating time in the reflow curve, increase the temperature rise slope, and reduce the volatility of the flux.
5. Turn on nitrogen to reduce the oxidation rate of solder paste.
Working process of chip mounter
The working process of the mounter roughly includes the following processes: plate feeding, PCB fixing, suction nozzle selection, plate feeder selection, component picking, component detection, displacement positioning, component placement and plate out placement
1. The PCB board to be installed enters the working area of the mounter and is fixed at a predetermined position;
2. The assembly passes through the feeder and is installed to the pickup position of the tip of the placement machine according to the position set by the program
3. Move the placing head to the suction position, turn on the vacuum, and the suction nozzle sucks the corresponding parts set in the program through the negative pressure, then check whether the parts are sucked in by the sensor;
4. Through the visual identification and positioning system, the placement head reads the component features of the component library and compares the absorbed components (such as appearance, size, etc.). Calculation of position and angle;
5. According to the set program, the placement head moves to the position set by the program, so that the center of the component coincides with the placement position of the PCB board;
6. The placement head lowers the nozzle to the programmed height (the placement height of the assembly is preset in the library), turns off the vacuum, and places the assembly on the corresponding pad of the PCB;
7. After that, the PCB board components have been installed, the suction nozzle returns to its position, and the PCB is transferred to the next smt process through the track Repeat to complete more PCB placement
The above is the explanation given by the editor of pcb circuit board company.
If you want to know more about PCBA, you can go to our company's home page to learn about it.
In addition, our company also sells various circuit boards,
High frequency circuit board and SMT chip are waiting for your presence again.