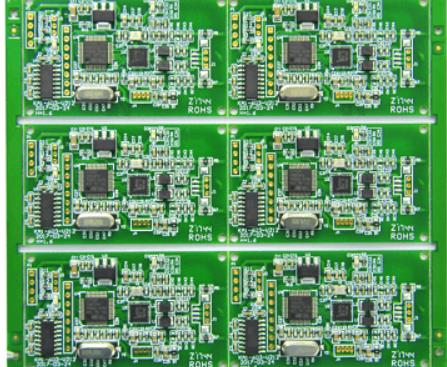
Reflow soldering has several temperature zones and furnace temperature settings
In PCB manufacturers in the process of PCB processing and production, reflow soldering of surface mounted technology equipment is an important link in which PCB is being processed and connected The reflow furnace process of SMT technology equipment is difficult The reflow furnace of SMT technology equipment is a group welding process All electronic components enable PCB circuit boards to be heated by welding polychlorinated biphenyls once. In this polychlorinated biphenyl treatment process, experienced SMT technology operators are required to control the furnace temperature curve of reflow soldering to ensure the welding quality of components PCB circuit boards and the quality and reliability of final products
Smt technology
SMT technology equipment reflow furnace has four areas. The standard is divided into preheating zone, constant temperature zone, tin melting zone and cooling zone. Most solder pastes can place PCB boards in these temperature zones. In order to enhance everyone's understanding of the standard temperature curve of PCB factory, PCB processing and SMT technology equipment reflow soldering furnace, the temperature of each area of SMT technology equipment reflow soldering furnace is the change of residence time, and the solder paste in each area is detailed as follows:
1. Preheating area: it is used to heat PCB circuit board to achieve preheating effect and fuse it with solder paste; However, at this time, the heating rate should be controlled within an appropriate range to avoid thermal shock and damage to circuit boards and components The heating slope of the preheating zone shall be less than 3 ℃/SEC, and the set temperature shall be between room temperature and 130 ℃ The residence time is calculated as follows: if the ambient temperature is 25 ℃ and the heating rate is 3 ℃/Securities and Exchange Commission, then (150-25)/3 is 4.2 seconds; If the heating rate is 1.5 ℃/s, then (150-25)/1.5 is 85 seconds Generally, it is better to adjust the time according to the difference of element size, and control the heating rate below 2 ℃/s
2. Constant temperature zone: the purpose is to stabilize the temperature of components on PCB and minimize the temperature difference. We hope that the temperature of large and small parts in this area can be balanced as much as possible, and the flux in the solder paste can be fully volatilized. However, it should be noted that in this area, the components on the PCB should have the same temperature to ensure that bad soldering does not occur when entering the reflow section. The set temperature of the constant temperature zone is 130 ℃~ 160 ℃, and the constant temperature time is 60 ~ 120s.
3. Reflow area: The temperature of the reflux area is the highest, which makes the component temperature on the PCB rise to the peak temperature. The peak temperature of reflow in SMT technology equipment depends on the solder paste used. It is generally recommended to use the melting point temperature of solder paste plus 20~40 ℃. The peak temperature is 210 ℃~230 ℃, and the time should not be too long to avoid adverse effects on polychlorinated biphenyls; The temperature rise rate in the reflux zone shall be controlled at 2.5-3 ℃/s, and the peak temperature shall be generally within 25s-30s. One of the skills here is that the tin melting temperature is above 183 ℃, and the tin melting time can be divided into two types, one is 60-90 seconds above 183 ℃, the other is 20-60 seconds above 200 ℃, and the peak temperature is 210 ℃~230 ℃.
4. Cooling area: the SMT technology equipment in this section has melted and fully wetted the lead tin powder polychlorinated biphenyl in the solder paste on the connection surface The polychlorinated biphenyl should be cooled as soon as possible, which will help to obtain bright solder joints and good appearance quality, and will not produce rough solder joints on the surface. The cooling speed of SMT equipment solder paste machine in the cooling section is generally 3~4 ℃/s, cooling to 75 ℃, and the cooling slope is less than 4 ℃/s
The above is the explanation given by the editor of pcb circuit board company.
If you want to know more about PCBA, you can go to our company's home page to learn about it.
In addition, our company also sells various circuit boards,
High frequency circuit board and SMT chip are waiting for your presence again.