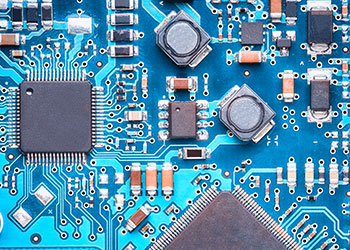
Quality assurance of PCBA processing?
Several links to ensure product quality One stop PCBA patch factory:
1. Smt patch processing link
The systematic quality control of solder paste printing and the reflow temperature control of PCBA for SMT chip processing are important links in the manufacturing process of PCBA. For high-precision PCB boards with special and complex printing process, laser steel mesh is used according to specific processing and production conditions to meet the quality standards of PCB boards. According to the requirements of PCB board and product characteristics of customers, some parts of chip processor need to add U-shaped holes or reduce steel mesh holes. The wire mesh shall be processed according to the requirements of PCBA processing technology.
The temperature control accuracy of the reflow furnace is crucial to the wetting of solder paste and the welding of steel mesh. It is also adjusted according to the normal SOP operation guidelines to reduce the minimum loss rate and reduce the occurrence of defective products in the process of PCBA SMT. In addition, the scientific and technological operators in the SMT workshop of the chip processing plant must conduct AOI testing in strict accordance with the standard to significantly reduce the occurrence of defective products caused by human factors during PCBA processing.
Polychlorinated biphenyls
2. Post welding connection of DIP parts
DIP plug-in post welding treatment is an important step in the welding process. PCB processing stage and the operation at the end of PCBA processing in the SMT processing plant In the process of DIP plug-in post welding, the requirements and standards for PCBA over peak welding are also critical PCBA over peak soldering can greatly improve the yield, reduce the occurrence of bad soldering such as tin connection, and reduce tin and tin deficiency Moreover, according to different requirements and standards of customers' products, PCBA processing plants must constantly summarize experience in practice Improve technology in the process of experience accumulation
3. Test and program combustion link
The manufacturability report is an evaluation conducted by the patch processor before the whole production when the patch processor receives the production contract from the customer. In the previous DFM report, the patch processor also communicated with the customer before processing the PCB and provided some effective suggestions, such as setting some key test points on the PCB. This is helpful for PCB welding test and key test of PCB conductivity and connectivity after PCB processing. If conditions permit, you can communicate with customers, provide back-end programs, and then burn PCBA programs to the core main IC through the burner. This will directly test the PCB through touch action, which is convenient for testing and testing the integrity of the entire processed PCB, and can detect defective PCB at the first time.
4. PCBA test connection
PCBA processing customers with one-stop service also have certain implementation standards for PCBA back-end testing. PCBA test generally includes ICT (circuit test), FCT (function test), combustion test (aging test), temperature and humidity test, drop test, etc. The relevant personnel in SMt workshop of SMt processing plant must receive strict standard training. In practice, we strictly follow the implementation standards and deliver the best quality products to customers.
The above is the explanation given by the editor of pcb circuit board company.
If you want to know more about PCBA, you can go to our company's home page to learn about it.
In addition, our company also sells various circuit boards,
High frequency circuit board and SMT chip are waiting for your presence again.