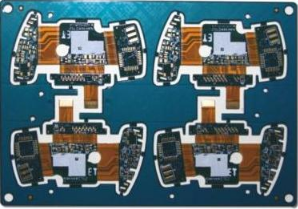
Usually, the two pads of the capacitor are marked with a+- sign. The actual color of the circuit board is white, that is, the pin on the side with the white face is the negative pole.
The names of circuit boards include: ceramic circuit board, alumina ceramic circuit board, aluminum nitride ceramic circuit board, circuit board, PCB board, aluminum substrate, high-frequency board, thick copper plate, impedance board, PCB, ultra-thin circuit board, ultra-thin circuit board, printed (copper etching technology) circuit board, etc.
Circuit board
Circuit board classification:
1、 Classification according to circuit layers:
1. Single panel. At the most basic level, parts are concentrated on one side and wires are concentrated on the other side. Because wires only appear on one side, this PCB is called a single panel.
2. Double sided board. This kind of circuit board has wiring on both sides, but if you want to use wires on both sides, you must have proper circuit connections between them.
3、。
(1) In order to increase the area of pcb wiring, more single or double sided wiring boards are used for multilayer boards. A printed circuit board with one double-sided as the inner layer, two single-sided as the outer layer, or two double-sided as the inner layer, and two single-sided as the outer layer, is a four layer or six layer printed circuit board, also known as a multilayer printed circuit board, when the positioning system and insulating bonding materials are alternately combined and the conductive patterns are interconnected according to the design requirements.
(2) The number of layers of the board represents several independent wiring layers. Usually, the number of layers is even and includes the two outermost layers. Most mainboards are 4-8 layer structures.
2、 Classified according to software and hardware: divided into ordinary circuit boards and flexible circuit boards.
Usually, the circuit board is marked with+- on or near the two pads of the capacitor, that is, positive and negative. Traditionally, the square pad is the first pin, but it is not sure that it is the positive pole. However, the actual color of the electrolytic capacitor on more circuit boards is white, that is, the pin on the side with the white face is the negative pole.
The square negative pole and round positive pole can also refer to the polarity of other capacitors on the same circuit board
The circle point is the positive pole! Block or block is the negative pole!
Meaning of pcb design substrate color
Many people like to judge the advantages and disadvantages of the motherboard according to the color of the PCB substrate. In fact, the color of the motherboard is not directly related to the performance. The color of PCB surface is actually the color of a solder mask (also known as solder mask), which is used to prevent the wrong soldering of electrical components in the welding process. At the same time, it has another role, which is to prevent the circuit oxidation and corrosion of welding components in the use process and reduce the failure rate.
In general, observe that the PCB boards of Huawei and ZTE are generally green, because the green process is the most mature and simple. But in extreme cases, there will also be red, white, blue, yellow and matt colors, and in more extreme cases, there will be black, purple, chrysanthemum, bright green, etc. In normal cases, white PCB boards must be used to make light products. Other colors are mostly product grading systems. Different companies use red to represent experimental boards, and blue to represent key boards, Some use black to represent the boards used in the computer. Each has its own rules.?
The most common color is green, that is, green board, also known as green oil. The green solder resist ink has the longest history and is the cheapest and most popular. Generally speaking, the whole electronic board level products have to go through the process of board making and pasting. In the process, several processes have to go through the yellow light room. The visual effect of green in the yellow light room is better, but this is not the main thing. During SMT welding, tin coating, pasting and final AOI verification are required. These processes are all optical positioning calibration. The green background is better for instrument identification.
Other common ones are red, yellow, green, blue and black. Due to the problem of process, the inspection of many lines still depends on workers' eyes (of course, most of them are tested with flying needles now). Keep looking at the board with bright eyes. This is a very tiring job. Green is relatively harmless. Therefore, most of them adopt green.
The blue and black PCB are mixed with cobalt and carbon respectively, which have certain conductivity, so there is a risk of short circuit. The green PCB is more environmentally friendly, and will not release toxic gas when used in high temperature environment.
Pcb design
In fact, if the color is too dark, it will often increase the difficulty of mainboard inspection and maintenance. Take the first black PCB as an example. In the process of PCB washing, black is the most likely to cause color difference. If there is a slight deviation between the raw materials used in the PCB factory and the self-made process, the color difference will cause an increase in the defective rate of PCB. Because the circuit routing of black PCB is difficult to identify, it will increase the difficulty of later maintenance and debugging. Generally, motherboard manufacturers will not use black PCB easily. Therefore, we can see that even military and industrial products with high quality requirements only use green PCB substrates.
What effect does the color of solder resist ink have on the board? Ink has no impact on finished products, but it has a great impact on semi-finished products, mainly on the ease of making semi-finished products. Some people also say that the color has an impact on PCB boards. Indeed, for example, there are matt green, sun green, dark green, light green, etc. in green. The color is a little different. The color is too light. It is easy to see that the appearance of the boards after the hole plugging process is not beautiful and the color is too dark. Then the ink of some manufacturers is not good enough. There is a problem with the ratio of resin and dye. There will be problems such as bubbles, and the ink will fall off in the final curing, This is the problem of ink matching. You can see that there is a slight change in color, and you can't feel it without years of experience. (This problem is a little complicated. Some inks are used by different machines, such as electrostatic spraying, spraying and screen printing. The inks are different, the proportions are different, and the colors are different. There will be a little problem if they are used incorrectly. In fact, for the finished board, these are all problems in appearance, and have no impact on the product itself.)
Although the ink color has no influence on the board, the ink thickness has a great influence on the impedance. Especially for the metal plate, the thickness control of the ink for this board is very strict. According to experience, it is easy to control the red ink, bubbles and thickness. First, the price of the ink is more expensive and the quality is indeed desirable. Second, the color can cover some defects on the circuit board, The green color will be more obvious. The third is the imaging link. It seems that the exposure of red and yellow is relatively stable, while green is not necessarily, and white is the most difficult to control.?