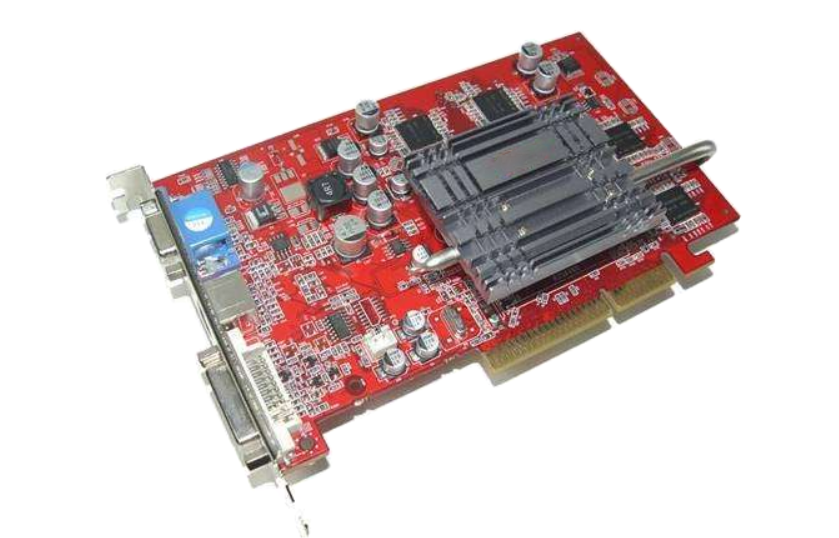
PCB sensor technology is one of the symbols of the development level of modern science and technology, and PCB pressure sensor technology is an important branch of sensor technology. At present, various types of PCB pressure sensors, such as diffused silicon, capacitive type, silicon sapphire, ceramic thick film, metal strain electric type, are widely used in various industries of national production and scientific and technological fields. The following is a brief introduction to the characteristics of some commonly used PCB pressure sensors and their differences.
Sapphire pressure sensor
Sapphire pressure sensor uses the working principle of strain resistance, and uses silicon sapphire as the semiconductor sensor, which has unparalleled metrological characteristics.
Sapphire system is composed of single crystal insulator elements, which will not cause hysteresis, fatigue and creep; Sapphire is stronger than silicon, with higher hardness and no fear of deformation; Moreover, sapphire has very good elasticity and insulation. Therefore, semiconductor sensing elements made of silicon sapphire are insensitive to temperature changes, and have good operating characteristics even under high temperature conditions; Sapphire has strong radiation resistance; In addition, the silicon sapphire semiconductor sensor has no p-n drift, so the PCB manufacturing process is fundamentally simplified, the repeatability is improved, and the high PCB yield is ensured.
PCB pressure sensors and transmitters made of silicon sapphire semiconductor sensing elements can work normally under the worst working conditions, with high reliability, good accuracy, minimal temperature error and high cost performance.
Diffused silicon pressure sensor
The working principle of the diffused silicon pressure sensor is: the pressure of the measured medium directly acts on the diaphragm of the sensor (stainless steel or ceramic), making the diaphragm produce a micro displacement proportional to the medium pressure, making the resistance value of the sensor change, detecting this change with PCB electronic circuit, and converting and outputting a standard measurement signal corresponding to this pressure.
Ceramic pressure sensor
The corrosion resistant ceramic pressure sensor has no liquid transmission. The pressure directly acts on the front surface of the ceramic diaphragm and the surface of the chamber diaphragm, causing slight deformation of the diaphragm. The thick film resistor is printed on the back of the ceramic diaphragm and connected to a Wheatstone bridge (closed bridge). Due to the piezoresistive effect of the varistor, the bridge generates a highly linear voltage signal proportional to the pressure and the excitation voltage, Standard signals are calibrated as 2.0, 3.0, 3.3 mV, etc. according to different pressure ranges, which can be compatible with strain gauge sensors. Through laser calibration, the sensor has high temperature stability and time stability. The sensor has its own temperature compensation of 0 ℃~70 ℃ and can directly contact with most media.
Ceramic is a recognized material with high elasticity, corrosion resistance, abrasion resistance, impact resistance and vibration resistance. The thermal stability of ceramics and its thick film resistance can make its working temperature range as high as - 40 ℃~135 ℃, and have high measurement accuracy and stability. The electrical insulation degree is greater than 2KV, the output signal is strong, and the long-term stability is good. Ceramic sensors with high characteristics and low price will be the development direction of pressure sensors. There is a trend to comprehensively replace other types of sensors in European and American countries. In China, more and more users use ceramic sensors to replace diffused silicon pressure sensors.
Complementary advantages of ceramic thick film structure and force sensitive Z-element
The thick film pressure sensor is another major technological innovation of the pressure sensor after the diffusion silicon pressure sensor, and the force sensitive Z-element is the only sensitive element with digital signal output at home and abroad at present. Therefore, the ingenious combination of the ceramic thick film process and the simplest circuit of the force sensitive Z-element can produce a new type of sensor with excellent performance and low cost. Specifically, the ceramic thick film process has the following advantages:
● The ceramic elastomer has excellent performance, and the flat, uniform and dense materials strictly follow Hooke's Law within the extent, without plastic deformation.
● The thick film resistor (including high-temperature conductor) can be firmly sintered with the ceramic elastic membrane, without adhesive. The rigid structure has small creep, small drift, stable static performance and good dynamic performance.
● Thick film elastomer has simple structure and is easy to prepare. Compared with the diffused silicon pressure sensor, it does not require semiconductor planar process to form the diffusion resistance elastic membrane, which greatly reduces the initial investment and processing cost of PCB production line.
● The ceramic thick film structure is resistant to the corrosion of liquid or gas medium, without the conversion and isolation of stainless steel diaphragm and silicone oil, and the packaging structure is simplified to further reduce the cost.
● Wide working range. The measuring range depends on the ratio of the effective radius to the thickness of the diaphragm. As long as the micro pressure is not less than 1Kpa, in principle, a higher measuring range is also easy to achieve.
● Wide operating temperature range, up to - 40 ℃~120 ℃.
Structure design of ceramic thick film force digital sensor
The ceramic thick film force digital sensor is mainly composed of ceramic ring, ceramic diaphragm and ceramic cover plate. As a force sensing elastomer, the ceramic membrane is made of 95% Al2O3 porcelain by finishing. It is required to be flat, uniform and dense. Its thickness and effective radius depend on the design range.
Porcelain ring is fired at high temperature by hot die casting process. High temperature glass slurry is used between the ceramic membrane and the ceramic ring, which is fired together through thick film printing and hot firing technology to form a force sensing cup shaped elastomer with peripheral fixed supports, that is, a rigid structure without creep shall be formed at the peripheral fixed supports of the ceramic. On the upper surface of the ceramic membrane, namely the bottom of the porcelain cup, the thick film process technology is used to make the circuit of the sensor. The circular groove at the lower part of the ceramic cover plate forms a certain gap between the cover plate and the diaphragm. The diaphragm can be prevented from breaking due to excessive bending when it is overloaded by limiting, forming an anti overload protection for the circuit board sensor.