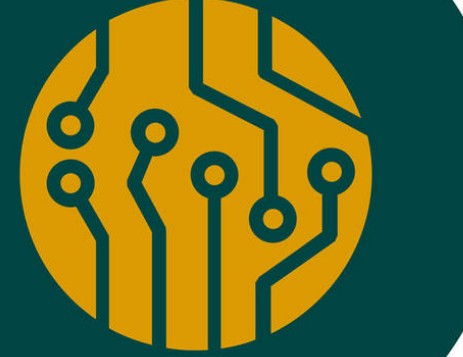
The spacing between adjacent wires must meet the electrical safety requirements, and in order to facilitate operation and production, the spacing should be as wide as possible. When the wiring density is low, the distance between signal lines can be increased appropriately. For signal lines with a wide gap between high and low levels, the distance should be shortened and increased as far as possible. In general, the distance between lines should be set to 8mil.
The distance between the inner hole edge of the pad and the printed board edge should be greater than 1m, so as to avoid the defects of the pad during processing. When the wire connection with the pad is fine, the connection between the pad and the wire should be designed into a droplet shape. The advantage of this is that the pad is not easy to peel, but the wire and the pad are not easy to disconnect.
wiring
The switching power supply contains high frequency signals. Any printed line on PCB can play the role of antenna. The length and width of printed line will affect its impedance and inductive reactance, thus affecting the frequency response. Even printed lines that pass through the DC signal can couple from neighboring printed lines to the RF signal and cause circuit problems (or even re-radiate interference signals). All printed wires that pass through the AC current should therefore be designed to be as short and wide as possible, which means that all components connected to the printed wires and to other power lines must be placed close together.
The length of the printed line is proportional to its inductance and impedance, and the width is inversely proportional to the inductance and impedance of the printed line. The length reflects the wavelength of the printed line's response. The longer the length, the lower the frequency at which the printed line can send and receive electromagnetic waves, and the more radio-frequency energy it can radiate. According to the size of the printed circuit board current, try to rent the width of the power line, reduce the loop resistance. At the same time, make the direction of the power line, ground line and the direction of the current, which helps to enhance the anti-noise ability. Grounding is the bottom branch of the four current circuits of the switching power supply. As the common reference point of the circuit, it plays an important role. It is an important method to control interference.
Therefore, careful consideration should be given to the placement of ground wires in the layout. Mixing all kinds of ground will cause unstable power supply.
The following points should be noted in the design of ground wire:
1. Correct selection of single point grounding Usually, the common end of the filter capacitor should be the only connection point of other ground points coupled to the AC ground of large current. The ground point of the same level circuit should be as close as possible, and the power filter capacitor of this level circuit should also be connected to the ground point of this level, mainly considering that the current of each part of the circuit back to the ground is changed. Interference is introduced due to the impedance of the actual flowing line, which causes changes in the ground potential of various parts of the circuit. In this switching power supply, the inductance between wiring and components has little influence, while the circulation formed by grounding circuit has great influence on interference. Therefore, one-point grounding is adopted, that is, ground wires of several devices in the power switching current loop () are connected to the ground pin, and ground wires of several devices in the output rectifier current loop are also connected to the ground pin of the corresponding filter capacitor. This power supply work more stable, not easy to self-excitation. When you can't do a single point, you can connect two diodes or a small resistor at a common location. In fact, you can connect it to a concentrated piece of copper foil.
2. If the ground wire is very thin, the ground potential will change with the change of the current, resulting in the timing signal level of electronic equipment is unstable, anti-noise performance deteriorated, so to ensure that the grounding terminal of each large current uses as short and wide as possible printed wire, as far as possible to widen the width of the power supply, ground wire, it is best to ground wire wider than the power line, their relationship is: Ground wire > Power cord > Signal wire, if possible, the width of the ground wire should be greater than 3m. A large area of copper layer can also be used as ground wire. On the printed board, the unused places are connected with the ground as ground wire. When conducting global wiring, the following principles must be followed:
(1) Wiring direction: from the perspective of welding surface, the arrangement orientation of components should be consistent with the schematic diagram as far as possible, and the wiring direction should be consistent with the wiring direction of the circuit diagram. Because various parameters are usually detected in the welding surface during the production process, it is convenient to do so for inspection, debugging and maintenance in the production (Note: On the premise of meeting the requirements of circuit performance, overall installation and panel layout).
(2) When designing the wiring diagram, try to minimize turning, the line width on the printing arc should not be sudden, the wire corner should be more than 90 degrees, and strive to make the line simple and clear.
(3) The printed circuit is not allowed to have a cross circuit, for the possible cross lines, you can use "drill", "wind" two ways to solve. That is, let a lead from other resistance, capacitance, the gap at the foot of the audion "drill" in the past, or from the possible cross of a lead end "wound" in the past, in special cases how to circuit is very complex, in order to simplify the design also allows the use of wire straddle, to solve the problem of cross circuit. Because of the single panel, the in-line component is located on the to p surface, and the surface paste device is located on the bottom surface, so in the layout of the in-line component and the surface paste device overlap, but to avoid the overlap of the pad.