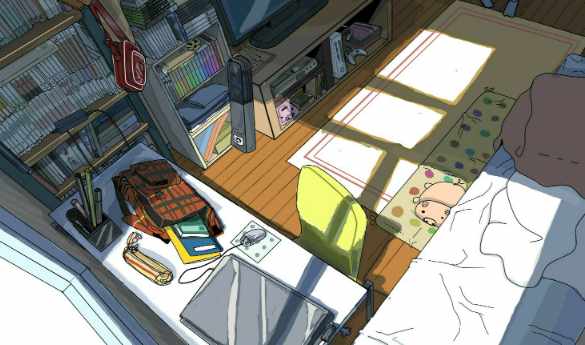
1. The preheating of PCB board through reflow welding is not sufficient;
2. The setting of reflow welding temperature curve is unfair, and there is a large gap between the surface temperature and the welding zone temperature before entering the welding zone;
3. Solder and solder paste can not be completely restored to room temperature when they are taken out from the cold storage;
4, the solder paste opened after a long time in the air exposure;
5, in the patch when tin powder splashed onto the PCB board surface;
6. In the process of printing or transferring, there is oil or water sticking to the PCB board;
7. The distribution of flux itself in solder paste is not fair and it is not easy to evaporate solvents or liquid additives or activators.
The first and second reasons above can also clarify why the new replacement of the solder paste prone to such questions, the main reason is the current temperature curve and the used solder paste does not match.
The third, fourth and sixth reasons can be formed for the user to manipulate improperly; The fifth reason can be because the solder paste storage is not proper or beyond the shelf life of the solder paste failure caused by the solder paste non-viscous or too low viscosity, forming a splash of tin powder in the patch; The seventh reason for the solder paste supplier's own production technology.
There are more residues on the PCB surface after welding SMT patches: It is a question often reported by customers that there are more residues on the PCB surface after welding. The existence of more residues on the PCB surface not only affects the brightness of the board surface, but also has a certain impact on the electrical properties of PCB itself. The main reasons for the formation of more residue are as follows: in the implementation of solder paste, do not know the customer's plate situation and customer needs, or other reasons to form the selection of fault; The solder paste contains too much rosin resin or its quality is not good.
LED switching power supply PCB design how to do is correct?
The speed of research and development of LED switching power supply has made a significant technological leap in recent years, and the speed of new product replacement has also accelerated a lot. As the last design link, PCB design is particularly important, because once there is a problem in this link, it is likely to produce more electromagnetic interference to the whole LED switching power system, and will cause adverse effects on the stability and safety of the power supply. So, how to do the design of PCB is correct?
The results of component layout research and market practice of LED power supply in recent years prove that even if the circuit schematic designed in the early stage of research and development is very correct, the reliability of electronic equipment will be adversely affected once PCB design problems occur. For example, the interference caused by the inconsiderate consideration of power supply and ground wire will degrade the performance of the product. Therefore, when designing PCB board, it is necessary to adopt the correct method.
In a PCB board commonly used in switching power supply, usually each switching power supply has four current circuits, they are respectively input signal source current circuit, power switch AC circuit, output rectifier AC circuit, output load current circuit. The input loop charges the input capacitor through an approximate DC current, and the filter capacitor mainly plays a role of broadband energy storage. Similarly, output filter capacitors are used to store high-frequency energy from the output rectifier while eliminating DC energy from the output load loop. Therefore, the terminals of the input and output filter capacitors are very important, and the input and output current loops should be respectively connected to the power supply only from the terminals of the filter capacitors.
The setup and connection of input and output circuits are very important for the whole printed circuit board, and whether it is reasonable or not will directly affect the size of electromagnetic interference. If the connection between the input and output loops and the power switch and rectifier loops cannot be directly connected to the terminal of the capacitor, the AC energy will be filtered by the input or output capacitor and radiated into the environment. The AC circuit of power switch and rectifier contains high amplitude trapezoidal current, which has a high harmonic component. Its frequency is much higher than the fundamental frequency of the switch. The peak amplitude can be up to 5 times of the continuous input and output DC current amplitude, and the transition time is usually about 50ns. These two circuits are the most likely to generate electromagnetic interference, so they must be laid before other printed wires in the power supply are routed.
In the input and input circuits of the LED switching power supply, each circuit is composed of three main components, which are filter capacitor, power switch or rectifier, inductor or transformer. These three important components should be placed next to each other and adjusted so that the current path between them is as short as possible. The best way to establish a switching power supply layout is similar to its electrical design. The optimal design process is as follows: Place the transformer → design the power supply switch current loop → Design the output rectifier current loop → control circuit connected to the AC power supply circuit → design the input current source loop and input filter.