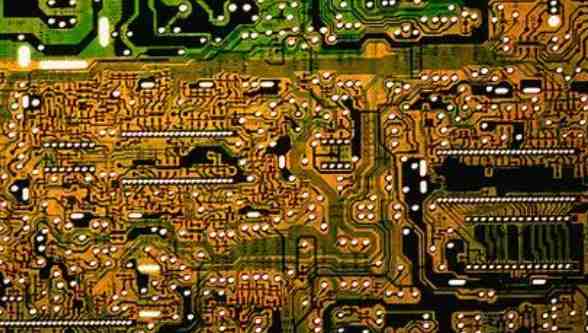
The current strength of the signal. When the average current of the signal is large, the current carried by the wiring width should be considered. The line width can refer to the following data:
PCB design copper foil thickness, wire width and current relationship
The carrying capacity of copper foil of different thickness and width is shown in the following table:
Note:
i. When copper wire is used to pass through high current, the carrying capacity of copper foil width should be selected and considered by referring to the value derating by 50% in the table.
ii. In PCB design and processing, OZ is commonly used as the unit of copper skin thickness. 1 OZ copper thickness is defined as the weight of copper foil within 1 square foot area is 1 ounce, and the corresponding physical thickness is 35um; 2OZ copper thickness 70um.
Four, how to determine the high current wire width
(b) Conductor thickness 35μm (c) conductor thickness 70μm (d) conductor thickness 105μm
Five, use PCB temperature impedance calculation software to calculate (calculate line width, current, impedance, etc.) PCBTEMP
Fill in the Location (External/Internal) wire on the surface or inside the FR-4 plate, Temp temperature (Degree C), Width line width (Mil) and Thickness (Oz/Mil), then Solve the current through. You can also figure out the current that's going through, and you can figure out the line width. It's very convenient.
You can see the same result as the first method (20 degrees Celsius, 10mil wire width, which is 0.010inch wire width, copper foil thickness 1 Oz).
Vi. Empirical formula
I = KT0.44 A0.75
(K is the correction factor. Generally, 0.024 is used for the inner layer of copper coated wire, and 0.048 is used for the outer layer
T is the maximum temperature rise in degrees Celsius (copper's melting point is 1060 degrees Celsius)
A is the cross-sectional area of copper-covered metal, and the unit is square MIL(not mm mm, note square mil.)
I is the maximum allowable current, expressed in amperes (amp)
Generally, 10mil=0.010inch=0.254 can be 1A,250MIL=6.35mm, 8.3A
7. The calculation method provided by a netizen is as follows
First calculate the cross-sectional area of track. The copper foil thickness of most PCBS is 35um (if you are unsure, you can ask the pcb manufacturer), which is the cross-sectional area multiplied by the width of the line, and pay attention to converting it into square millimeters. There is an empirical current density value of 15 to 25 amps per square millimeter. Call it the upper cross-sectional area and you get the through-flow capacity.
Eight, a little experience on line width and copper laying through holes
We generally have a common sense when drawing PCB, that is, use thick lines (such as 50mil, or even above) where the current is high, and use thin lines (such as 10mil) for signals with low current. For some electromechanical control systems, sometimes the instantaneous current flowing through the wire can reach more than 100A, so the relatively thin wire will certainly cause problems.
A basic rule of thumb is 10A/ mm2, that is, 10A for a cable with a cross-sectional area of 1 mm2. If the wire width is too thin, it will burn out when a large current passes through it. Of course, the current burning wire should also follow the energy formula: Q = I*I*t. For example, for a 10A current wire, a 100A current burr suddenly appears, with a duration of us level, then the 30mil wire is sure to be able to withstand. Another question arises... The stray inductance of the wire, the burr will produce a strong reverse electromotive force under the action of this inductance, which may damage other devices. The thinner and longer the wire, the larger the stray inductance, so in practice, the length of the wire should be taken into consideration)
General PCB rendering software to the device pin of the through hole solder plate when laying copper often has several options: right Angle spoke, 45 degree spoke, straight laying. What's the difference? Novices often do not care too much, just choose one, beautiful on the line. Not so much. There are two main considerations: one is to consider not too fast heat dissipation, the second is to consider the current capacity.
The use of direct paving mode is characterized by a strong overcurrent capacity of the pad, for high-power circuit device pins must be used in this way. At the same time, its thermal conductivity is also very strong, although the work is good for the heat dissipation of the device, but this is a problem for the circuit board welding personnel, because the heat dissipation of the welding plate is too fast and not easy to hang tin, often need to use larger wattage iron and higher welding temperature, reduce the production efficiency. The use of right Angle spokes and 45 Angle spokes will reduce the contact area between the pin and the copper foil, slow heat dissipation, and welding will be much easier. Therefore, the connection mode of copper paving through the hole welding plate should be selected according to the application situation, the comprehensive overcurrent capacity and heat dissipation capacity should be considered together. The signal line of low power should not be directly paved, and the welding plate must be directly paved through the high current. Whether it's a right Angle or a 45 degree Angle is beautiful.
Why bring this up? Because I was researching a motor driver a while ago, the device of the H bridge in this driver kept burning out, and I couldn't find the reason for it for four or five years. After a lot of hard work, it was finally found that the welding disc of a device in the power loop used the right Angle spokes when laying copper (and due to the poor copper laying, only two spokes actually appeared). This makes the overcurrent capacity of the whole power loop greatly reduced. Although the product does not have any problems in the normal use process, it works perfectly normally under the condition of 10A current. However, when there is a short circuit in the H bridge, there will be a current of about 100A in the circuit, and the two spokes will be burned out instantaneously (Class uS). Then, the power loop becomes a circuit breaker, and the energy stored in the motor is dissipated through all possible ways without a drain channel. This energy will burn the current measuring resistance and related op-amp devices, destroy the bridge control chip, and enter the signal and power supply of the digital circuit part, causing serious damage to the entire equipment. The whole process was as thrilling as detonating a large landmine with a single strand of hair.
So why are only two spokes used on the pads in the power loop? Why don't you just lay the foil across? Because, the production people said that this pin is too difficult to solder!