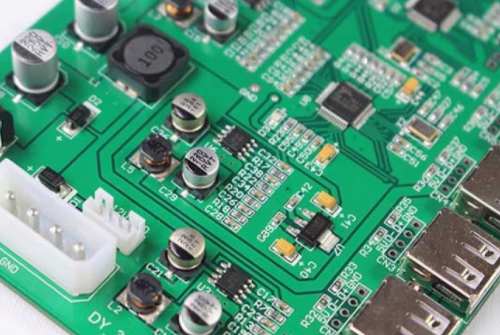
In the medical, automobile and other industries closely related to life, many products have strict requirements on quality. As a criterion of welding quality, tin penetration rate also has its own importance. In addition to the flux and solder wire/solder paste problem, the biggest impact is the welding method.
Next, Shenzhen PCBA processing manufacturer kingford will introduce the influence of welding methods on the tin penetration rate of PCBA
1, manual welding is mainly for some special-shaped parts and the process sequence need to be manually welded devices for processing an original means, this way in the iron temperature setting is not appropriate and unreasonable adjustment of welding time is easy to cause plug-in solder penetration rate is insufficient, and lead to false welding products. Therefore, this method can be used as plug-in welding in general. If the product has a very high requirement for tin penetration, it is necessary to carefully consider whether this method is feasible.
2. Wave soldering, as the main welding equipment of DIP plug-in in pcba processing, has a direct influence on welding quality in soldering, such as the height setting of wave crest, the setting of temperature curve, the moving speed of the product and the length of welding time, so the process control of wave soldering directly determines the quality of tin penetration rate.
3. Selective wave welding, as the "upgrade version" of wave welding equipment, can be applied to the spot coating of solder paste for a single point, which greatly eliminates the influence of wave height and welding time, and can greatly ensure the tin penetration rate of PCBA. Therefore, in the processing of medical electronics pcba, in order to ensure the penetration rate of the plug-in material, Shenzhen Honglijie Electronics will use selective wave soldering, to ensure the quality stability of customers in the process of use. This method has been proved to be the most helpful welding method for solder penetration.
2. How to set SMT patch processing parameters?
Shenzhen kingford has its own SMT plant, which can provide SMT SMT processing services of 0201 components with minimum package, supporting incoming material and sample processing and PCBA OEM. Next, we will introduce the SMT patch processing parameters setting method.
In SMT patch processing, many processes need to set up processing equipment, among which the most important steps can be summarized into 7 steps:
First, graph alignment
The printer camera is used to align the optical MARK point with the steel mesh and the steel mesh on the workbench, and then fine tune the X, Y, θ and other graphics, so that the steel mesh and steel mesh pad graphics are completely consistent.
2, the Angle of the scraper and the steel mesh
The smaller the Angle of the scraper and the steel mesh, the greater the downward pressure, you can easily inject the solder paste into the steel mesh, you can also easily squeeze the solder paste into the bottom of the steel mesh, resulting in the solder paste adhesion. Usually the Angle is between 45 and 60. Today, most automatic and semi-automatic printing press systems are in use.
3, scraping force
Scraper force is also an important factor affecting printing quality. Scraper (also known as scraper) pressure management is actually the depth of the scraper drop, the pressure is too small, the scraper can not stick to the surface of the screen, so it is equivalent to the SMT patch processing to increase the thickness of printing materials. In addition, if the pressure is too small, the net will leave a layer of solder paste, easy to cause printing defects, such as molding, bonding, etc.
4, printing speed
Because the scraping speed is inversely proportional to the solder paste viscosity, when the solder paste density is large, the spacing becomes narrow and the printing speed becomes slow. Because the scraping is too fast and the mesh time is short, the solder paste can not fully penetrate the mesh, which is easy to cause the solder paste uneven, leakage and other printing defects. There is a certain relationship between printing speed and scraper pressure, the speed of decline is equal to the speed of pressure, appropriate reduction of pressure speed can improve the printing speed. The best scraping speed and pressure control method is to scrape the solder paste off the surface of the steel mesh.
5, printing gap
The printing gap is the distance between the printed circuit and the circuit, which is related to the printed solder paste left on the circuit board.
6, steel mesh and PCB separation speed
After solder paste printing, the instantaneous speed of steel mesh leaving PCB is the separation speed. The separation speed is the main factor affecting the printing quality, which is particularly important in high-density printing. Advanced smt printing equipment, the iron screen away from the solder paste pattern will have 1 (or more) small pause process, that is, multi-stage release, to ensure the best printing results. The separation rate is too large, the solder paste viscosity decreases, the solder pad viscosity is small, resulting in part of the solder paste attached to the bottom of the steel mesh and the hole wall, resulting in printing quality problems, such as printing quantity reduction, printing collapse, etc. The separation speed is slow, the solder paste viscosity is large, the viscosity is good, the solder paste is easy to leave the steel mesh, the hole wall, and the printing condition is good.
Vii. Cleaner production mode and cleaning frequency
Steel mesh washing bottom is also a factor to ensure the quality of printing. Cleaning method and frequency should be based on the solder paste material, steel mesh thickness and hole size. Steel mesh pollution (set dry cleaning, wet washing, one-time reciprocating, wiping speed, etc.). If the data is not cleaned up in time, it will pollute the PCB surface, and the residual solder paste around the steel mesh holes will harden, and in serious cases it will block the steel mesh holes.
In SMT processing plant, the parameter setting of many details cannot be accomplished overnight. It is necessary to sum up experience in long-term practice to improve the management and continuous optimization of quality control details.
Shenzhen kingford PCBA processing capacity
1. Maximum board card: 310mm*410mm(SMT);
2. Maximum plate thickness: 3mm;
3. Minimum plate thickness: 0.5mm;
4. Minimum Chip parts: 0201 package or parts above 0.6mm*0.3mm;
5. Maximum weight of mounted parts: 150g;
6. Maximum parts height: 25mm;
7. Maximum parts size: 150mm*150mm;
8. Minimum spacing of pin parts: 0.3mm;
9. Minimum ball parts (BGA) spacing: 0.3mm;
10. Minimum ball parts (BGA) ball diameter: 0.3mm;
11. Maximum parts mounting accuracy (100QFP) : 25um@IPC;
12. Patch capacity: 3-4 million points/day.
Why choose Shenzhen kingford to do PCBA processing?
1. Strength guarantee
▪SMT workshop: We have imported SMT machines and several sets of optical inspection equipment, with a daily output of 4 million. Each process is equipped with QC personnel, who can keep an eye on product quality.
▪DIP production line: We have two wave-soldering machines, among which there are more than 10 old employees who have worked for more than three years. The skilled workers can weld all kinds of plug-in materials.
2. Quality assurance, cost-effective
▪ High-end equipment can stick precision shaped parts, BGA, QFN, 0201 materials. Can also template patch, loose material hand.
▪ Sample and size batch can be produced, proofing from 800 yuan, batch 0.008 yuan/point, no start-up fee.
3. Rich experience in SMT and welding of electronic products, stable delivery
▪ Accumulated SMT SMT processing services for thousands of electronic enterprises, involving many kinds of automotive equipment and industrial control motherboard. The products are often exported to Europe and the United States, and the quality can be affirmed by new and old customers.
▪ On time delivery, normal 3-5 days after complete materials, small batch can also be expedited on the same day shipment.
4. Strong maintenance ability and perfect after-sales service
▪ Experienced maintenance engineers can repair all kinds of patch welding caused by bad products, to ensure the connection rate of each piece of circuit board.
▪ 24-hour customer service staff at any time response, the fastest speed to solve your order problems.