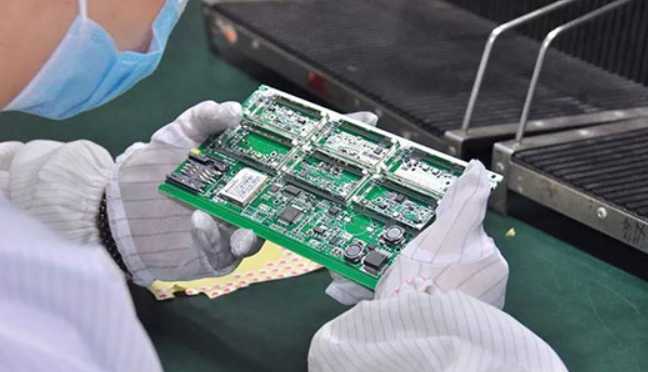
PCBA processing equipment, technology, process account for the vast majority of quality, the other part is what we will discuss here, that is components. Components are the core components of the circuit board, the quality of components is directly related to the final quality of PCBA processing. Components market is crowded and mixed, how to avoid fake and shoddy components is a professional PCBA processing manufacturers necessary skills.
The parts market is a very chaotic one at the moment. Not only the price is unstable, but also the quality is uneven. Some took advantage of the chaos to sell disassembled materials, scrap and three nothings. This has greatly tested the ability of various PCBA processing plants to identify counterfeit parts. Next, Shenzhen kingford will share with you several test methods that can be used to identify counterfeit electronic parts in daily operations.
First, visual inspection
The easiest way to check for counterfeit parts is a visual inspection. This includes checking the part number and screen markings on the part against the specifications provided by the source manufacturer. In addition, you can use previous data and past purchases from vendors to verify the validity of the date code. Other aspects of visual inspection are as follows:
Fraudsters may use black layers to place different part numbers and date codes on parts. It involves applying a thin black epoxy coating to the top of the part and then roughing the surface to get the desired texture. It also involves matching the font to the original font. In order to determine if there is a power failure, it is important to check the top and surface texture of the parts. In addition, it is necessary to compare the manufacturer's symbol with the known original parts.
Before PCBA proofing, you should also check whether the leads of the components are damaged, re-tinned, etc. This is part of the incoming inspection and cannot be ignored due to the tight delivery time.
Other factors to consider in the device include component orientation, general appearance, contact conditions, and visual inconsistencies.
Second, electrical testing
Electrical testing of counterfeit electronic components involves verification of resistance and capacitance values and full functional analysis of active components. Electronic testing facilities are available from various contract manufacturers (CM) and third party testing laboratories. In order to test complex products, expensive test setup and programming expertise is essential, which can only be achieved in OCM or some third party LABS. When major component exceptions are involved here, you can also request an evaluation from the source factory.
Third, X-ray examination
X - ray the hidden/internal characteristics of the component. When comparing, it is always helpful to have a gold standard or a famous example. This method checks and validates the physical dimensions, lead frame, and connection wires. In addition, it checks for any internal changes in all components.
Fourth, XRF technology
XRF stands for X-ray fluorescence spectrum. This technique determines the element composition of the material that is best suited for verifying RoHS compliance.
2. Is Gerber file important for PCBA processing?
We need Gerber file and BOM list in PCBA processing. In PCB board and SMT processing are helpful. These files are generated for each layer in stack-up. In addition to the layer information, these files also contain other data. All layers are specifically mentioned, such as top, bottom, solder stop top/bottom, assembly top/bottom, Silkscreen top/bottom, wafer layer, etc.
In terms of personal consumer products and military aerospace grade PCbas, whether the PCB design layout is simple or complex, the final design phase is the final node, with complete Gerber file output, which is input by the PCBA manufacturer during the manufacturing process. Gerber file can be defined as PCB structure drawing in digital format, which is an important document in PCB manufacturing and SMT processing. Incorrect or incomplete Gerber files can cause the PCB to malfunction or perform poorly. Because of the many details of the Gerber document design, some errors or other problems can occur if not reviewed rigorously during production. The main factors are as follows:
1. The Gerber file is lost or incomplete
2. List of missing circles
Having a detailed aperture list with all the layer specifications and the same format as the Gerber file reduces the chance of errors and failures.
3. Zero-byte Gerber PCB file
4.Gerber file labels are incomplete or misleading
5. Lack of internal clearance
6. Errors in making composite layers
Some design software uses layer combinations when creating design specifications for each layer. The Gerber file problem can be reduced here to prevent quality anomalies in PCBA processing. Therefore, Gerber files are very important for PCBA processing.
Why choose Shenzhen kingford to do PCBA processing?
1. Strength assurance
▪ SMT workshop: We have imported SMT machines and a variety of optical testing equipment, capable of producing 4 million pieces per day. Every process is equipped with QC personnel who can keep a close eye on product quality.
▪ DIP production line: There are two wave welding machines. Among them, there are more than ten old employees who have worked for more than three years. Skilled workers can weld all kinds of insert materials.
2. Quality assurance, high cost-effective
▪ High-end equipment can mount precision heterosexual parts, BGA, QFN, 0201 materials. Proofing can be machine paste, also can be hand pendulum.
▪ Samples and large and small batches can be produced. Proofing starting price 800 yuan, batch starting price 0.008 yuan/point, no start-up fee.
3. Rich experience in SMT and welding of electronic products, stable delivery time
▪ Has served thousands of home appliance subsidiaries, involving various kinds of automotive equipment and industrial control motherboard SMT SMT processing services. Products are often exported to Europe and the United States, the quality of new and old customers affirmed.
▪ On time delivery, usually within 3-5 days after the board is assembled, small batch expedited can also be shipped on the same day.
4. Strong maintenance ability and perfect after-sales service
▪ Experienced maintenance engineers are able to repair defective products caused by various welding problems and ensure the connectivity rate of each circuit board.
▪ 24-hour customer service staff will be ready to respond and resolve your order as soon as possible.