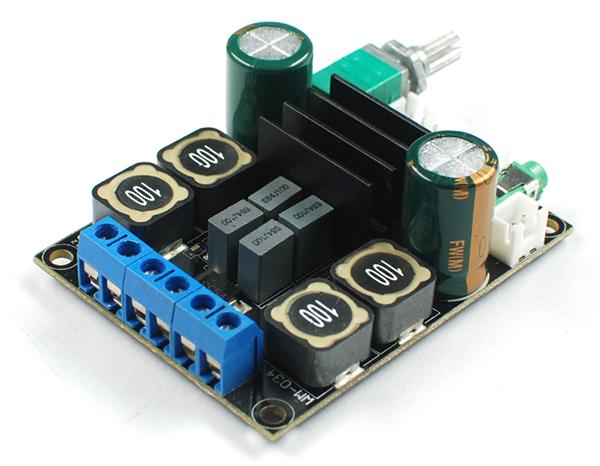
Although many traditional printed circuit board offer excellent features, not all PCBS are suitable for LED applications. For optimal performance in lighting applications, PCBS must be designed for use with leds to maximize heat transfer capacity. Aluminum based circuit boards provide a common foundation for a variety of high output LED applications. LED lighting solutions are rapidly gaining ground in a variety of industries and are highly valued for their low power consumption, high efficiency and impressive light output. Most high lighting output LED applications use aluminum-based circuit boards, primarily aluminum-based circuit boards that enable higher levels of heat transfer.
The biggest difference between aluminum based circuit board and conventional FR4 circuit board is the heat dissipation. Compared with the 1.6mm thickness of FR4 circuit board and aluminum based circuit board, the thermal resistance of the former is 20 ~ 22℃, and the thermal resistance of the latter is much smaller 1.0 ~ 2.0℃. Aluminum based circuit board is a kind of metal based copper coated plate with good thermal conductivity, which has good thermal conductivity, mechanical properties, gas and electrical insulation properties.
(1) Heat dissipation
At present, many double panels and multilayer panels have high density, high power and difficult heat emission. Conventional printed circuit board substrates such as FR4, CEM3 are hot conductors, interlayer insulation, heat does not go out. Local heating of electronic equipment is not excluded, resulting in high temperature failure of electronic components, and aluminum based circuit board can solve this problem of heat dissipation.
(2) Dimensional stability
Aluminum-based circuit boards are obviously much more stable in size than insulated printed boards. Aluminum based circuit board, aluminum sandwich board, from 30℃ heating to 140~150℃, the size change is 2.5~3.0%.
(3) thermal expansibility
Thermal expansion and cold contraction is the common nature of substances, and the coefficient of thermal expansion of different substances is different. Aluminum based circuit board can effectively solve the problem of heat dissipation, so that the printed circuit board components of different substances on the thermal expansion and contraction problem to alleviate, improve the durability and reliability of the whole machine and electronic equipment, especially to solve the SMT patch processing thermal expansion and contraction problem.
(4) Other performance
Aluminum circuit board has a shielding effect, instead of brittle ceramic substrate, the use of surface installation technology at ease, reduce the real effective area of the printed circuit board, replace the radiator and other components, improve product heat resistance and physical properties, reduce production costs and labor.
The advantage of aluminum based circuit boards is that the heat dissipation is significantly better than the standard FR4 circuit boards, the dielectric used is usually 5 to 10 times the thermal conductivity of conventional epoxy glass, and the heat transfer index of one tenth of the thickness is more efficient than the traditional PCB circuit boards. How much is the thermal conductivity of aluminum based circuit board? Aluminum based circuit board thermal conductivity refers to the heat dissipation performance parameters of aluminum based circuit board, it is one of the three standards to measure the quality of aluminum based circuit board. The thermal conductivity of aluminum circuit board can be obtained after the plate pressing through the test instrument test data, the higher the thermal conductivity is the better the performance of the aluminum circuit board.
Aluminum based circuit board its thermal conductivity is 1.0-2.5, aluminum based circuit board is a kind of good heat dissipation function of metal coated copper plate, usually a single panel is composed of three layers of structure, are circuit layer (copper foil), insulation layer and metal base. For high-end use are also designed for double panels, the structure of the circuit layer, insulation layer, aluminum base, insulation layer, circuit layer. Very few applications for multilayer board, can be made of ordinary multilayer board and insulation layer, aluminum base fit. The thermal conductivity of aluminum based circuit board is determined by the thickness of copper foil and insulation layer. The thickness of copper foil is 25mu, 35mu, 70mu. The insulation layer has PP glass fiber cloth base (poor thermal conductivity), thermal glue (good thermal conductivity), ceramic powder (excellent thermal conductivity).
The size of the thermal conductivity of aluminum circuit board is generally fixed, will not change with the external factors, the size of the thermal conductivity is mainly determined by the raw materials of aluminum circuit board. If copper, silver and other high thermal conductivity materials are added, the thermal conductivity of aluminum substrate materials will certainly be higher. Thermal conductivity is a basic physical quantity, a fixed component of a material, and the size of its thermal conductivity has nothing to do with thickness or area. Now the high thermal conductivity value is usually ceramic, copper, but because of the cost of the question, now on the market for the majority of aluminum based circuit boards, the corresponding aluminum substrate thermal conductivity is the parameter we care about, the higher the thermal conductivity is one of the symbols of the better function.
(1) Telecommunication industry: Telecommunication equipment usually uses PCBS to control its LED indicators and displays. Lightweight and durable PCBS tend to be advantageous in the industry, mainly due to the density of mechanical equipment in the industry. Aluminum based circuit boards are commonly found in telecommunications lighting applications because they tend to have better heat transfer characteristics than FR4 boards.
(2) Automotive industry: PCB LED displays are common in the automotive industry, especially in dashboard indicators, headlights, brake lights and advanced panel displays. The industry particularly likes PCB leds because of their low manufacturing cost and durability, which increase the value and service life of vehicles.
(3) Computer technology industry: PCB-based leds are becoming increasingly common in the computer technology industry, commonly found in desktop and laptop computer monitors and indicators. Because of the thermal properties of computer technology, aluminum-based circuit boards are particularly suitable for LED lighting applications in computers.
(4) Medical industry: Lighting tools are extremely important in medical applications, especially in surgical and emergency applications, where bright light can help improve the doctor's vision. In these applications, leds are often the preferred lighting method due to their low power and small size. PCBS are commonly used as the basis for these applications, especially aluminum-based circuit boards, which have a longer life and better heat transfer capacity compared to other types of PCBS. In this way, the aluminum-based circuit board ensures a durable medical device that can be used repeatedly in a variety of medical Settings.
(5) Residential and storefront applications: In addition to the uses listed above, PCB LED are becoming increasingly popular in the form of signs and displays in homes and businesses. Smart LED lighting is an inexpensive way for homeowners to efficiently light their homes, while customizable LED displays can direct business to storefronts.