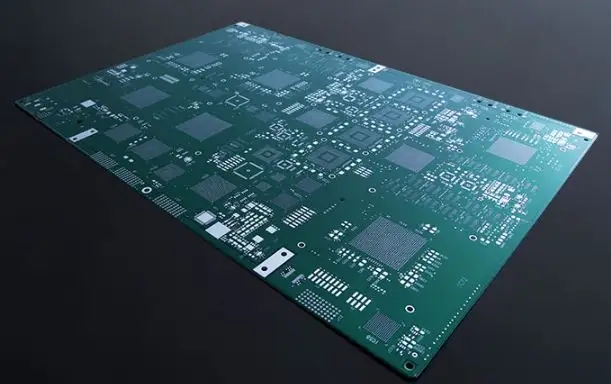
PCB manufacturers analyze PCB direct electroplating process for you
PCB manufacturers, PCB designers and PCBA processors explain to you that PCB manufacturers analyze PCB direct electroplating process for you
1. Dirt removal
For the conduction of multi-layer plate holes, after drilling, the drilling dirt shall be removed first, that is, the resin on the inner copper surface shall be removed after drilling. Typical drilling dirt removal processes include resin expansion, alkaline potassium permanganate solution treatment, neutralization and other processes to remove the residual potassium permanganate on the board.
The resin expansion treatment includes the use of appropriate expansion agent for the circuit board at elevated temperature. Expanding agents may include aqueous solutions containing alkali metal hydroxides and ethylene glycol or other solvents, or using non-aqueous solvents.
After resin expansion, the circuit board is treated with alkaline potassium permanganate solution. It is usually prepared by mixing alkaline hydroxide and potassium permanganate with water. Also, surface reducing agents can be used in special applications. The effective time and temperature of the multilayer board treated with alkaline potassium permanganate solution depend on the technological characteristics of the dielectric materials.
After removing drilling dirt with potassium permanganate solution, neutralize the solution The composition of neutralization solution includes at least one part of neutral or acid reducing agent. Reductants can be selected from any chemical and can reduce excessive potassium permanganate or manganese ions. The verified reducing agents include dihydrozine sulfate and hydroxydiamine salt. Hydrogen peroxide/sulfate neutralization can also reduce potassium permanganate and manganese oxides. At the same time, it can slightly corrode the copper surface to remove the "nail head" in the through-hole, and obtain a standard appearance to improve the adhesion with the coating.
2. Regulators
In the process of conditioning agent treatment, it is easy to deposit carbon particles with negative changes on the plate to increase the adhesion if the positive change of regulator molecules is used for the medium surface coating. The regulator solution comprises an alkaline buffer mixed solution composed of a cationic regulator and a surface stress reducing agent.
The alkaline regulator usually uses the chelate of amine to provide solution stability in alkaline solution, provide a safer environment for direct metallization process, and develop a non chelate alkaline buffer system to meet the development needs of the black hole process.
3. Carbon base
Carbon black has good electrical conductivity. Its performance depends on its particle size, surface area, structure and other chemical reactions and physical properties. Carbon black is used for direct metallization because it is very easy to disperse into liquid water, and this coating is applied to the substrate because it has stability and conductivity. At the same time, the changes of carbon surface after chemical adjustment and the effects of different carbon particles in the dispersion on conductivity and stability were also studied. For example, when the oxidized carbon black and non oxidized carbon black are mixed, the high conductivity of carbon black can easily make the oxidized carbon hydrophilic in the dispersant and improve the conductivity of the coating, which should be attributed to the non oxidized carbon black with high conductivity. The use of regulators and new dispersants can not only improve the stability of the solution, but also effectively improve the conductivity of the coating and have excellent compatibility with the copper carbonate electroplating solution.
4. Dispersion
Carbon particles are hydrophobic and difficult to disperse into aqueous solution. Adding dispersant can provide hydrophilic layer around carbon particles. The cationic dispersant preferentially promotes the adhesion between the surface of the medium treated by the cationic regulator and the carbon particles. Cationic dispersants also produce repulsion between negative carbon particles to prevent condensation. Various dispersants have different chemical properties. After testing, they include phosphate grease, sulfonate and alkylated ethanol. Add dispersant to make the most important conditions can be reached through process test. When the concentration of dispersant is too low, the carbon particles will agglomerate and precipitate. Excessive dispersant will form a barrier layer between the carbon particles and the medium, which will eventually reduce the conductivity of the carbon coating obtained. Therefore, the best process condition is to improve the stability of dispersant and the conductivity of dry carbon coating.
5. Microetching
The micro etching process is to remove excess carbon from the copper surface and corrode the copper surface by penetrating the carbon coating. In this way, the micro rough surface provided by the carbon coating from the copper surface will be improved, and the adhesion with the electroplating copper will be increased. The micro etching solution contains oxidants, such as persulfate or peroxide, acid and other additives. Etching rate is changed by the concentration of oxidant and operating temperature or the concentration of other ions and additives. The micro etching system minimizes the loss of clean copper surface. In particular, it is very important to apply high technology to the cleaning treatment of small holes or micro blind holes on the inner layer of copper, and improve the micro etching performance through chemical changes and good adjustment. New additives enable clean copper surfaces to achieve an effective low etch rate of 10-20 microinches per minute. Another important carbon removal process should be micro etched after a short time of water washing. Because too long water cleaning or slightly acidic cleaning will loosen the dry carbon particles, the cleaning process should be accelerated after micro etching, and the best cleaning process conditions should be selected to prevent the reduction of conductive layer on the medium surface. PCB manufacturers, PCB designers and PCBA processors explain the PCB manufacturers' analysis of PCB direct electroplating process for you.