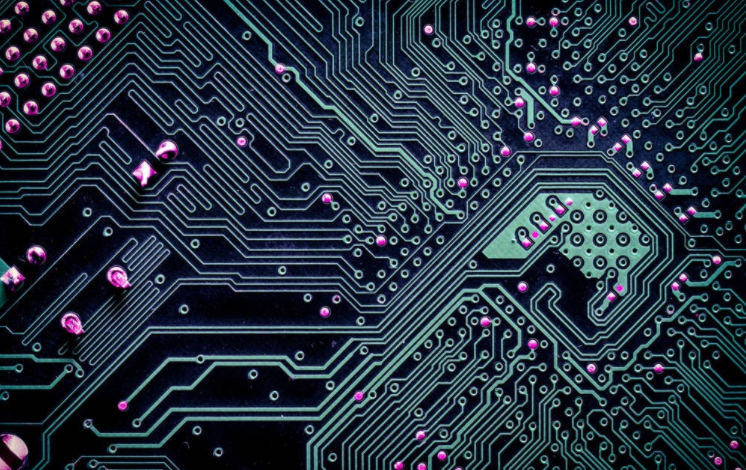
How to improve the open and short circuit problem of PCB
PCB circuit open and short circuit is a problem that PCB manufacturers encounter almost every day, which has always plagued production and quality management personnel. The problems caused by it, such as replenishment due to insufficient shipment quantity, delivery delay, and customer complaints, are more difficult for insiders to solve. I have worked in PCBA manufacturing industry for more than 20 years, mainly engaged in production management, quality management, process management and cost control. We have accumulated some experience in improving the open and short circuit problems of PCB, and now we have formed a text for summary, which can be used for discussion of PCB manufacturing by peers, and we look forward to the peers who manage production and quality for reference. First, we summarize and classify the main causes of PCB open circuit into the following aspects:
1. The copper clad laminate is scratched before entering the warehouse; 2. The CCL is scratched in the process of cutting; 3. The copper clad plate was scratched by the drill bit during drilling; 4. The copper clad plate is scratched in the process of transportation; 5. The copper foil on the surface was damaged due to improper operation when stacking plates after copper deposition; 6. The copper foil on the surface of the production plate is scratched when passing the leveler.
Improvement method:
1. The IQC must carry out spot check on the CCL before entering the warehouse to check whether there is scratch on the board surface and the base material is exposed. If there is, contact the supplier in time and make appropriate treatment according to the actual situation.
2. The copper clad laminate was scratched during the blanking process, mainly due to the existence of hard and sharp objects on the table of the blanking machine. During blanking, the copper foil was scratched due to the friction between the copper clad laminate and the sharp objects. Therefore, the table must be carefully cleaned before blanking to ensure that the table is smooth and free of hard and sharp objects.
3. The copper clad laminate was scratched by the drill bit when drilling, mainly because the spindle clamp bit was worn, or there were sundries in the clamp bit was not cleaned up, the PCB sampling drill bit was not firmly grasped, the drill bit did not go up to the top, which was slightly longer than the set drill bit length, the lifting height during drilling was not enough, and the drill bit tip scratched the copper foil to form exposed substrate when the machine tool moved. a. The clamping nozzle can be replaced by the number of times recorded by grabbing the tool or according to the wear degree of the clamping nozzle; b. Clean the clamping nozzle regularly according to the operation procedures to ensure that there are no sundries in the clamping nozzle.
4. The plates are scratched in the process of transportation: a. The number of plates lifted by the handling personnel at one time is too much and the weight is too large, so the plates are not lifted but pulled up in the process of transportation, resulting in friction between the plate angle and the plate surface and scratching the plate surface; b. The boards were not placed neatly when they were put down, so they were pushed hard to rearrange them, which caused friction between boards and scratched the board surface.
5. After copper sinking and electroplating, the plates were scratched due to improper operation when stacking: after copper sinking and electroplating, when storing the plates, the plates were stacked together, and the weight was not small when there were a certain number of plates. When the plates were put down again, the plate corners were downward and there was a gravitational acceleration, forming a strong impact force hitting the plate surface, causing the plate surface to scratch and expose the substrate. 6. The production plate is scratched when passing the leveler: a. The baffle of the plate grinder sometimes contacts the surface of the plate. The edge of the baffle is generally uneven and there are sharp objects protruding. The plate surface is scratched when passing the plate; b. The stainless steel transmission shaft becomes a sharp object due to damage, and the copper surface is scratched when passing the plate, exposing the base material.