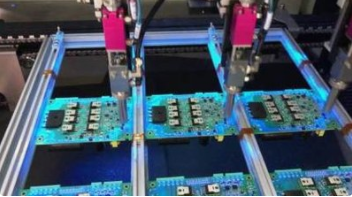
This paper describes the basic situation and development trend of water-soluble organic solderable protective agent (OSP) in PCB industry, and focuses on the research of a copper/gold selective OSP system. The OSP solution of this system is stable and easy to control. It has excellent gold surface selectivity and excellent weldability. It solves the problems existing in OSP in PCB industry, such as easy coating of gold surface and uneven discoloration at high temperature.
1 Preface
In recent years, the requirements of electronic products and mounting technology on the finished surface treatment of printed circuit boards (PCBs) are increasingly high, including lead-free, halogen-free and high-temperature solderability. Due to various disadvantages, the traditional hot air leveling technology will gradually be replaced by other surface coating technologies, such as chemical nickel gold deposition, chemical silver deposition, chemical tin deposition, and organic solderability preservatives (OSP). Among them, the OSP surface treatment method has become one of the environmentally friendly PCB surface coating methods preferred by many enterprises after continuous improvement in recent years, with increasingly mature technology and low price.
Water soluble OSP is also called copper protecting agent and copper surface antioxidant in the industry. It forms a thin, uniform and dense organic protective film on bare copper by chemical method. The protective film can be easily pushed away by the solder during high temperature welding, thus ensuring the solderability of the copper surface. The heat resistance of the OSP film layer mainly depends on the film forming agent used. At present, the film forming agent has experienced five generations of changes, including benzotriazole, alkyl imidazole, benzimidazole, alkyl benzimidazole and aromatic imidazole. At present, the fourth generation of alkyl benzimidazole derivatives are mostly used in the market. There are different opinions on the mechanism of OSP film formation. Some scholars believe that imidazole compounds are bound with divalent copper ions to form a film; Some scholars also believe that imidazole compounds coordinate with copper surface atoms first, and then univalent copper ions complexe with imidazole compounds, further increasing the film.
At present, OSP is divided into OSP for copper plate and selective OSP for copper gold mixed carrier plate. That is, the difference lies in whether the film is deposited on the gold surface. The quality of OSP on the market varies greatly. Although some of them are selective, there are problems such as easy coating on the copper surface, uneven discoloration at high temperature, easy crystallization of bath solution, and complex process management and control. These problems have been widely concerned by the industry, and everyone is committed to developing OSP technology with better performance. This paper introduces the research of a copper/gold selective OSP system.
2 Overview of the OSP Technology
2.1 Process flow
The general process flow of OSP is as follows:
Degreasing → water washing → micro etching → water washing → acid washing → water washing → OSP → water washing → strong air drying → hot air drying
The process flow of this OSP system is as follows:
Degreasing → water washing → micro etching → water washing → pre immersion water washing → OSP → water washing → strong air drying → hot air drying.
Good compatibility with the original equipment, just replace the pickling section with the pre leaching section.
2.2 Process principle
In the OSP process, there are different valence copper (Cu0, Cu+and Cu2+) on the copper surface after micro etching treatment. The active imidazole in the pre immersion solution coordinates with the copper atom on the copper surface to form a single molecular layer. After dehydrogenation of - NH on the imidazole molecule, it continues to coordinate with the univalent copper to form bonds, thus forming a very thin alkaline organic film on the copper surface. When the copper surface covered with alkaline organic film enters the OSP main tank, the alkaline organic film is dissolved under acidic conditions, releasing univalent copper ions. Copper ions do not diffuse rapidly, but stay near the copper surface, directly bond with the main film-forming material in the OSP solution, and enter the newly formed OSP film. When the imidazole compound copper organic complex film grows to a certain extent, because there is no excess univalent copper ion in the solution, the increase of the film thickness mainly depends on the van der Waals force and hydrogen bond between the imidazole compound molecules. When the dynamic balance of the deposition and desorption of imidazole molecules is reached, the film thickness will not increase.
3 Advantages in PCB technology
3.1 Excellent copper/gold selectivity
Generally, after OSP treatment, the copper/gold mixed carrier plate is reflowed and subjected to high temperature treatment, and the gold surface on the PCB is easy to change color, that is, an organic film is applied on the gold surface that should not be coated, and oxidation discoloration occurs at high temperature, resulting in quality problems. This is because the copper/gold mixed carrier plate is prone to generate the Giavanni effect directly under the acid bath of the OSP main tank. At this time, the copper surface plays the role of anode, while the gold surface plays the role of cathode. When copper is dissolved in the bath solution and forms an organic copper complex film with imidazole compounds in the bath solution, electrons will be thrown out at the same time, and the electrons will be enriched on the gold surface through the circuit. When Cu2+exists in the bath solution, Cu2+will be reduced due to obtaining electrons, and will be complexed with imidazole compounds and deposited on the gold surface, resulting in high temperature discoloration of the gold surface. Therefore, with the increase of copper ion concentration in the OSP main tank, this phenomenon becomes more obvious.
This OSP system is specially designed for the copper/gold mixed carrier plate, which can greatly avoid the film on the gold surface. On the one hand, it uses weak alkaline pre immersion solution to replace the pickling in the original process, and the weak alkaline solution itself will not produce the Giavanni effect, but also can play a role in cleaning the gold surface. On the other hand, there is no copper ion added to the OSP main tank solution, and even fewer copper ions are brought into the tank solution after pre leaching, which can fundamentally solve the gold discoloration problem caused by the Giavanni effect.
3.2 Excellent weldability
The function of the OSP film is to protect the clean copper surface on the PCB from oxidation under certain conditions. Before the assembly and welding of electronic parts, the OSP film can be quickly removed with flux, so that the copper surface on the PCB has good solderability and can form a solid solder joint with molten solder. At present, the color change of OSP film reflow after treatment of many domestic OSP products is uneven, and there is still a certain gap in solderability compared with large foreign PCB companies. However, the color change of copper surface treated by this OSP system is uniform after multiple reflow soldering
3.3 Other advantages
At present, the majority of OSP main tank liquid medicines on the PCB market are composed of two or more kinds of liquid medicines. The control and addition of the tank liquid are cumbersome, and the operation is slightly improper, which is easy to cause tank liquid imbalance. The OSP system is different. The main tank liquid medicine is composed of a single liquid medicine, and has the following other characteristics: low operating temperature (34 ℃~38 ℃), less volatile; The control of process parameters is simple. Only the concentration of film forming agent, pH value and OSP film thickness need to be controlled; The buffer of the bath solution is good; The OSP film thickness is easy to adjust, and the OSP film thickness can be quickly adjusted by adjusting the pH value of pre leaching or OSP.
This OSP system has another major advantage, that is, its stability is better than that of ordinary OSP products, and there is no crystallization. The experiment shows that the wheel moving roller is repeatedly immersed in the OSP bath solution of this system and placed in the fume hood for one day. After the roller is dried, there is no crystal precipitation, while ordinary OSP products have crystal precipitation, as shown in Figure
4 Summary
With the development of PCB electronic products towards multi-function, light and thin, printed circuit boards are also moving towards high density. The development trend of replacing hot air leveling with organic solderable protective agent introduced by Japan is becoming more and more obvious. OSP process has the advantages of low cost, simple operation, convenient tank liquid maintenance, adapting to green and environment-friendly production mode, meeting RoHS instructions, meeting the requirements of the lead-free era, etc. Therefore, OSP technology has been widely used and praised by the PCB manufacturing industry. Although the current OSP process still has some shortcomings compared with the surface treatment of other metals, its stability and reliability are constantly improved with the continuous development of technology, which is bound to continue to become stronger and stronger on the road of PCB final surface treatment.