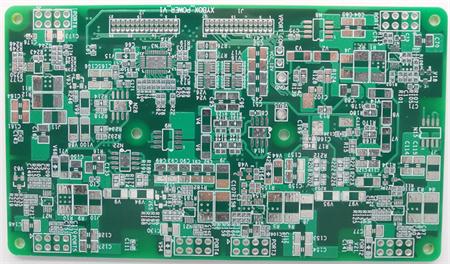
In PCBA processing, the quality of PCB welding has a great impact on the performance and appearance of PCB, so it is very important to control the welding quality of PCB. PCB welding quality is closely related to PCB design, process materials, welding process and other factors.
1、 Design of PCB
1. Pad design
(1) When designing the pad of plug-in components, the pad size shall be designed appropriately. The pad is too large, the solder spreading area is large, and the solder joints formed are not full, while the surface tension of the copper foil of the smaller pad is too small, and the solder joints formed are non wetting solder joints. The fit clearance between the hole diameter and the component lead is too large, which is easy to solder. When the hole diameter is 0.05 - 0.2mm wider than the lead, and the pad diameter is 2 - 2.5 times of the hole diameter, it is an ideal condition for welding.
(2) When designing the bonding pad of SMD components, the following points should be considered: In order to eliminate the "shadow effect" as far as possible, the SMD terminal or pin should face the direction of the tin flow to facilitate the contact with the tin flow and reduce false soldering and solder skips. The smaller components shall not be arranged behind the larger components, so as to prevent the larger components from hindering the contact between the tin flow and the pad of the smaller components and causing solder leakage.
2. PCB board flatness control
Wave soldering has high requirements on the flatness of printed boards. Generally, the warpage should be less than 0.5mm. If it is greater than 0.5mm, leveling should be done. In particular, if the thickness of some printed boards is only about 1.5mm, the requirements for warpage are higher. Otherwise, the welding quality cannot be guaranteed. The following matters should be noted:
(1) Properly store printed boards and components, and shorten the storage period as much as possible. During welding, copper foil and component leads free of dust, grease and oxide are conducive to forming qualified solder joints. Therefore, printed boards and components should be stored in a dry and clean environment, and the storage period should be shortened as much as possible.
(2) For printed boards that have been placed for a long time, their surfaces should generally be cleaned to improve solderability and reduce false soldering and bridging. For component pins with a certain degree of oxidation on the surface, the surface oxide layer should be removed first.
2、 Quality control of process materials
In wave soldering, the main process materials used are: flux and solder.
1. The application of flux can remove the oxide on the welding surface, prevent the re oxidation of solder and welding surface during welding, reduce the surface tension of solder, and help heat transfer to the welding area. Flux plays an important role in the control of welding quality.
2. Quality Control of Solder
The tin lead solder is continuously oxidized at high temperature (250 ℃), which makes the tin content of tin lead solder in the tin pot continuously decrease, deviates from the eutectic point, resulting in poor liquidity, continuous soldering, faulty soldering, insufficient solder joint strength and other quality problems.
3、 Welding process parameter control
The influence of welding process parameters on the quality of welding surface is relatively complex. There are several main points: 1. Control of preheating temperature. 2. Inclination of welding track. 3. Wave crest height. 4. Welding temperature.
Welding is an important process step in PCB manufacturing. In order to ensure the welding quality of PCB , we should master the quality control methods and welding skills.