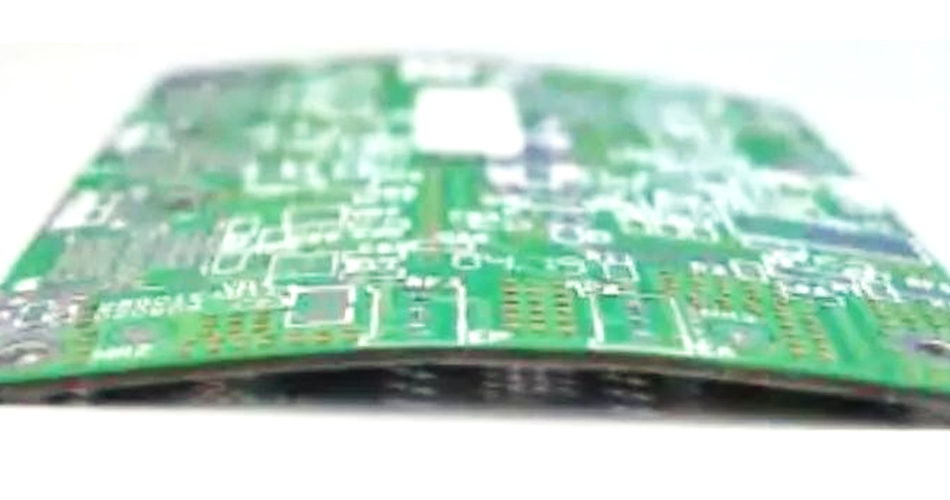
Hazards of PCB board deformation
Shenzhen pcb factory will explain to you: Why does PCB board warp? What are the hazards after deformation?
On the automatic surface mount line, if the circuit board is not flat, it will cause inaccurate positioning, and components cannot be inserted or mounted on the holes of the board and surface mount pads, or even damage the automatic insertion machine.
The circuit board with components is bent after welding, and it is difficult to cut the component legs neatly. The board can not be installed on the chassis or the socket inside the machine, so it is also very troublesome for the assembly plant to encounter the board warping.
At present, surface mount technology is developing towards high precision, high speed and intelligence, which requires higher flatness of PCB as the carrier of various components.
The IPC standard specifically points out that the allowable deformation of PCB boards with surface mount devices is 0.75%, and the allowable deformation of PCB boards without surface mount devices is 1.5%.
In fact, in order to meet the requirements of high-precision and high-speed mounting, some electronic assembly manufacturers have more stringent requirements on deformation. If required, the allowable deformation is 0.5%, or even 0.3% in some cases.
PCB board is composed of copper foil, resin, glass cloth and other materials. The physical and chemical properties of each material are different. After pressing together, thermal stress residues will inevitably occur, leading to deformation.
At the same time, in the process of PCB processing, high temperature, mechanical cutting, wet treatment and other processes will also have an important impact on the deformation of the board. In short, the causes of PCB deformation are complex and diverse. How to reduce or eliminate the deformation caused by different material properties or processing has become one of the complex problems faced by PCB manufacturers.
Cause Analysis of PCB Board Deformation
The deformation of PCB needs to be studied from several aspects such as material, structure, graphic distribution, processing and so on. This article will analyze and elaborate various causes of possible deformation and improvement methods.
The uneven copper surface area on the circuit board will worsen the bending and warping of the board.
Generally, a large area of copper foil is designed on the circuit board for grounding. Sometimes, a large area of copper foil is designed on the Vcc layer. When these large areas of copper foil cannot be evenly distributed on the same circuit board, the problem of uneven heat absorption and heat dissipation will occur.
Of course, the circuit board will also expand with heat and contract with cold. If the expansion and contraction cannot occur at the same time, it will cause deformation due to different stresses. At this time, if the temperature of the board has reached the upper limit of Tg value, the board will begin to soften and cause deformation.
The connection points (vias) on each layer of the circuit board will limit the board's expansion and contraction.
Nowadays, most circuit boards are multilayer boards, and there will be rivet like connection points (vias) between layers. The connection points are divided into through holes, blind holes and buried holes. Where there are connection points, the effect of expansion and contraction of the board will be limited, and the bending and warping of the board will be indirectly caused.
Reasons for PCB board deformation:
(1) The weight of the circuit board itself will cause the board to sag and deform
Generally, a chain is used in the reflow furnace to drive the circuit board forward in the reflow furnace, that is, both sides of the board are used as fulcrums to support the whole board.
If there are overweight parts on the board or the size of the board is too large, the board will show a hollow in the middle due to its own weight, resulting in bending.
(2) The depth of V-Cut and the connecting bar will affect the deformation of the panel
Basically, V-Cut is the culprit of destroying the board substructure. Because V-Cut cuts grooves on the original large sheet, the V-Cut area is prone to deformation.
Influence of pressing material, structure and figure on deformation of plate:
PCB board is made of core board, semi solidified sheet and outer copper foil by pressing. The core board and copper foil are subject to thermal deformation when pressing, and the deformation amount depends on the thermal expansion coefficient (CTE) of the two materials.
The coefficient of thermal expansion (CTE) of copper foil is about 17X10-6; While the CTE of common FR-4 substrate in Z-direction at Tg point is (50~70) X10-6; Above TG point is (250~350) X10-6. Due to the existence of glass cloth, CTE in X direction is generally similar to copper foil.
Deformation caused during PCB processing:
The causes of PCB board deformation during processing are very complex, which can be divided into thermal stress and mechanical stress.
The thermal stress is mainly generated in the pressing process, and the mechanical stress is mainly generated in the process of plate stacking, handling and baking. The following is a brief discussion in the order of the process.
1. Incoming materials of CCL:
Copper clad plates are double-sided plates with symmetrical structure and no graphics. Copper foil and glass cloth CTE are almost the same, so there is almost no deformation caused by different CTE during pressing.
However, due to the large size of the CCL press and the temperature difference in different areas of the hot plate, the resin curing speed and degree in different areas during the pressing process will be slightly different, and the dynamic viscosity at different heating rates will also be greatly different, so the local stress caused by the difference in the curing process will also be generated.
Generally, this kind of stress will maintain balance after pressing, but will gradually release in the future processing to produce deformation.
2. Pressing:
The pressing process of PCB is the main process to generate thermal stress. Similar to the pressing process of CCL, it will also generate local stress caused by the difference in curing process. Due to the thicker thickness, diverse pattern distribution, more semi cured pieces and other reasons, the thermal stress of PCB will be more and more difficult to eliminate than that of CCL.
However, the stress in PCB is released in the subsequent drilling, shape or barbecue processes, resulting in deformation of the board.
3. Baking process of resistance welding and characters:
Because solder resist inks cannot be stacked with each other when curing, PCB boards will be vertically placed in the shelf to dry the boards for curing. The solder resist temperature is about 150 ℃, which just exceeds the Tg point of medium and low Tg materials. The resin above the Tg point is highly elastic, and the boards are easy to deform under the self weight or strong wind in the oven.
4. Hot air solder leveling:
The temperature of tin furnace is 225 ℃~265 ℃ and the time is 3S-6S when the hot air solder for ordinary plate is leveled. The temperature of hot air is 280 ℃~300 ℃.
When the solder is leveled, the plate enters the tin furnace at room temperature, and the post-treatment water washing at room temperature is carried out within two minutes after it is discharged from the furnace. The whole hot air solder leveling process is a sudden heating and cooling process.
Due to different PCB materials and uneven structure, thermal stress will inevitably occur during the cold and hot process, resulting in micro strain and overall deformation and warping.
5. Storage:
The storage of PCB boards in the semi-finished product stage is generally vertically inserted in the shelf. The improper adjustment of shelf tightness or stacking of boards during storage will cause mechanical deformation of the boards. Especially for the thin plates below 2.0mm, the impact is more serious.
In addition to the above factors, there are many other factors that affect PCB deformation.
Prevention of PCB Warpage
The warpage of the circuit board has a great impact on the production of the printed circuit board. The warpage is also one of the important problems in the production process of the circuit board. The board with components is bent after welding, and it is difficult to keep the component feet neat.
The board cannot be installed on the chassis or the socket in the machine, so the warping of the circuit board will affect the normal operation of the whole subsequent process.
At this stage, the printed circuit board has entered the era of surface mounting and chip mounting, and the requirements of the process on the warpage of the printed circuit board are getting higher and higher. So we need to find the cause of the warping of the circuit board.
1. Engineering design:
Precautions for PCB design:
A. The arrangement of interlayer prepreg shall be symmetrical. For example, for six ply boards, the thickness between 1~2 and 5~6 layers shall be consistent with the number of prepreg sheets, otherwise it is easy to warp after lamination.
B. Multilayer core board and prepreg shall be from the same supplier.
C. The area of the outer layer A and B lines should be as close as possible. If the A side is large copper and the B side only runs a few wires, this kind of printed board is easy to warp after etching. If the difference between the line areas on both sides is too large, some independent grids can be added on the sparse side for balance.
2. Drying plate before blanking:
The purpose of drying the copper clad plate (150 ° C, 8 ± 2 hours) before blanking is to remove the moisture in the plate, and at the same time, fully solidify the resin in the plate, further eliminate the residual stress in the plate, which is helpful to prevent the plate from warping.
At present, many double-sided and multilayer boards still adhere to the process of drying boards before or after blanking. However, there are some exceptions to this rule. At present, the drying time of PCB plants is also inconsistent, ranging from 4 to 10 hours. It is recommended to decide according to the grade of PCB produced and the customer's requirements for warpage.
The two methods are both feasible, and it is recommended to bake the board after shearing. The inner plate shall also be baked.
3. The warp and weft directions of the prepreg:
After laminating, the shrinkage of the prepreg in the warp and weft direction is different. The warp and weft directions must be distinguished when blanking and laminating. Otherwise, it is easy to cause warping of the finished board after lamination, and it is difficult to correct even if the pressure is applied to bake the board.
Many reasons for the warping of multilayer boards are due to the disorderly overlapping of the warp and weft directions of the prepreg during lamination.
How to distinguish longitude and latitude? The roll up direction of the rolled prepreg is the warp direction, while the width direction is the weft direction; For copper foil, the long side is in the weft direction and the short side is in the warp direction. If you are not sure, you can check with the manufacturer or supplier.
4. Stress relief after lamination:
Take out the multilayer board after hot pressing and cold pressing, cut or mill off the burrs, and then place it flat in the oven at 150 ℃ for drying for 4 hours to gradually release the stress in the board and completely cure the resin. This step cannot be omitted.
5. The sheet needs to be straightened during electroplating:
When the 0.4~0.6mm ultra-thin multilayer board is used for plate surface electroplating and graphic electroplating, special clamping rollers shall be made. After the thin plate is clamped on the fly bar on the automatic electroplating line, a round bar shall be used to string the clamping rollers on the whole fly bar, so as to straighten all the plates on the roller, so that the plates after electroplating will not be deformed.
Without this measure, the thin plate will be bent and difficult to repair after electroplating 20 to 30 micrometers of copper layer.
6. Plate cooling after hot air leveling:
When the PCB is leveled by hot air, it will be impacted by the high temperature of the solder bath (about 250 ℃). After being taken out, it should be put on the flat marble or steel plate for natural cooling, and then sent to the post-processing machine for cleaning. This is good for warping prevention of boards.
Some factories, in order to enhance the brightness of the lead tin surface, put the boards into cold water immediately after hot air leveling, and take them out for post-treatment after a few seconds. This impact of one hot and one cold is likely to cause warping, delamination or blistering of some models of boards.
In addition, air floating bed can be installed on the equipment for cooling.
7. Treatment of warped boards:
In a well managed factory, 100% flatness inspection will be conducted for printed boards during final inspection. All unqualified boards will be picked out and put into an oven, dried at 150 ℃ and under heavy pressure for 3-6 hours, and naturally cooled under heavy pressure.
Then, take out the boards by pressure relief, and check the flatness. This can save some boards. Some boards need two or three times of baking to be leveled. If the anti warping process measures mentioned above are not implemented, it is useless to bake and press some boards, and you can only report to the superior?