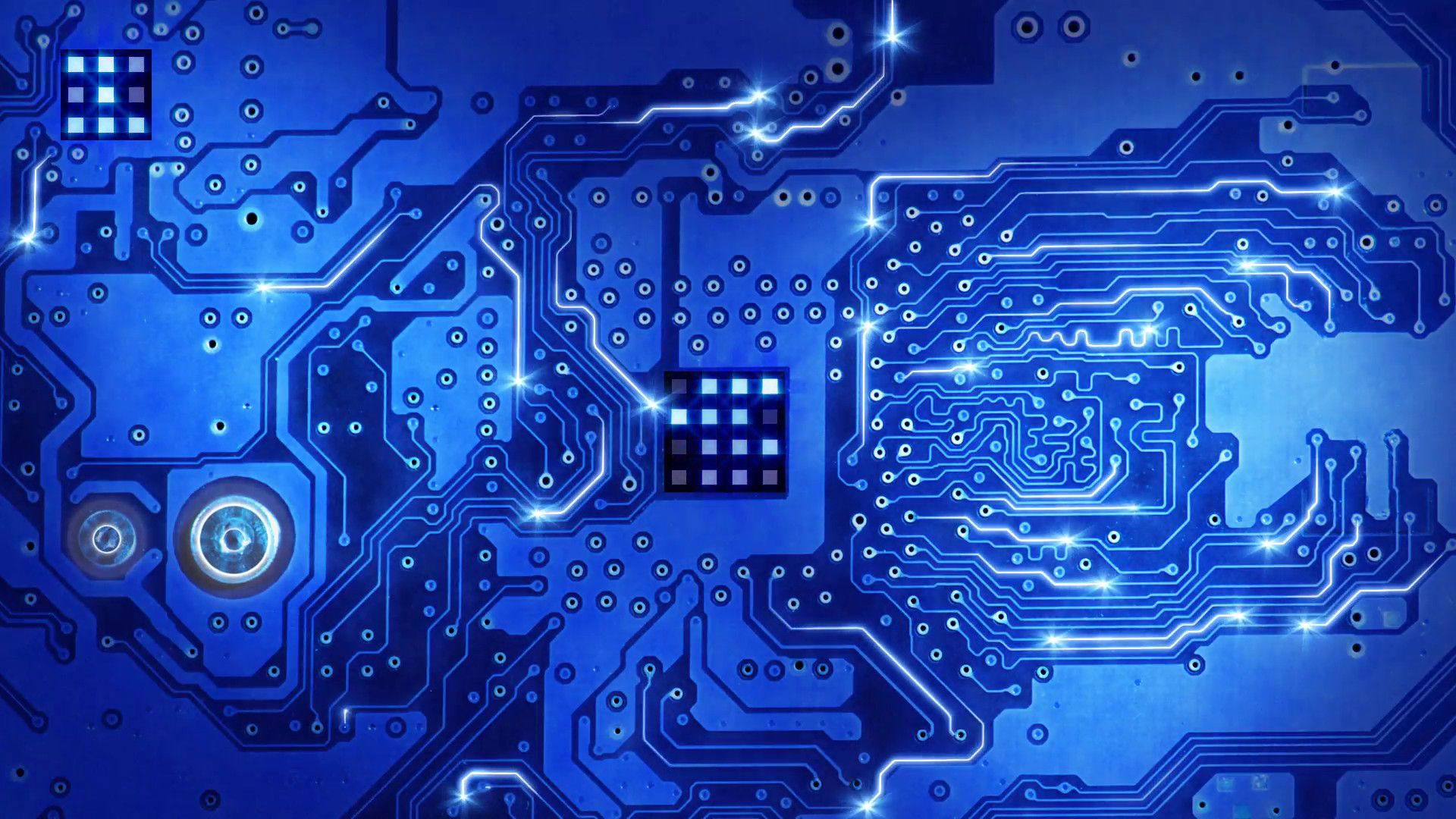
Introduction to flexible PCB materials
Flexible PCB materials need to support multiple design and operational goals: static or dynamic bending, ability to pass standard assembly processes, support simple manufacturing procedures, and achieve high yields. Flexible PCB materials may seem exotic at first glance, but a relatively small group of materials are available for high-volume production of flex and rigid-flex PCBs. In this guide, we'll look at some of the basic properties of flex PCB materials and how they can be used to build flex/rigid-flex PCBs.
Substrates and cover films
The most common substrate used in rigid printed circuit boards is woven fiberglass impregnated in epoxy resin. It's actually a fabric, and while we call these "rigid", if you take out the individual laminate layers, they're reasonably stretchy. The cured epoxy makes the board more rigid. Due to the use of epoxy resins, they are often referred to as organic rigid printed circuit boards. This isn't flexible enough for many applications, but for simple components that don't move constantly, it may be suitable.
The most common material choice for use as a flexible PCB substrate is polyimide. This material is very flexible and has incredible heat resistance.
Flexible polyimide film (Source: Shinmax Technology Ltd.)
For most flex circuit applications, more flexible plastics than usual network epoxies are required. The most common choice is polyimide, as it is very flexible (you can't tear it by hand or stretch it significantly, allowing it to withstand the product assembly process) and is extremely heat resistant. This makes it highly resistant to multiple solder reflow cycles and fairly stable against expansion and contraction caused by temperature fluctuations.
Polyester (PET) is another commonly used flexible circuit material, but it cannot withstand high enough temperatures to survive soldering. I've seen it used in very low cost electronics where the flexible parts have printed conductors (PET can't handle the heat of lamination), let alone elements that don't have solder - instead it conducts isotropically via rough pressure The elastomer makes contact.
The display in the product in question (timer radio) never really worked properly due to the poor quality of the flex circuit connections. Therefore, for rigid-flex, we assume sticking with PI films. (Other materials are available but less frequently used).
PI and PET films, along with thin flexible epoxy and fiberglass inner cores, constitute common substrates for flexible circuits. The circuit must then be covered with an additional film (usually PI or PET, sometimes flex soldermask). The cover layer insulates the outer surface conductors and prevents corrosion and damage, much like solder mask does on rigid board circuits. PI and PET films range in thickness from ⅓ mil to 3 mil, typically 1 or 2 mil. Fiberglass and epoxy substrates are significantly thicker, ranging from 2 mils to 4 mils.
conductor
While the aforementioned inexpensive electronics may use printed conductors—usually some kind of carbon film or silver-based ink—copper is the most typical conductor choice. Depending on the application, different forms of copper need to be considered. If you are simply using the flex portion of the circuit, reducing manufacturing time and cost by removing cables and connectors, then a copper foil laminate (electrodeposited or ED) typically used for rigid circuit boards is an option. This can also be used where a heavier copper weight is required to keep high current-carrying conductors to the smallest feasible width, such as planar inductors.
But copper is also notorious for deformation hardening and fatigue. If your end application involves repeated flexing or movement of flex circuits, higher grades of rolled annealed (RA) foils need to be considered. Clearly, the extra step of annealing the foil adds significantly to the cost. But annealed copper is able to stretch more before fatigue cracking and is more elastic in the Z deflection direction -- exactly what you want in a flex circuit that can bend or roll all the time. This is because the rolling annealing process elongates the grain structure in the planar direction.
If you are simply using the flex portion of the circuit, reducing manufacturing time and cost by removing cables and connectors, you can choose laminated copper foil, which is usually used for rigid circuit boards.
PCBA Manufacturing Machinery Challenge
in the manufacturing process
inner layer separation
May be caused by debris from drilling, microetching, desmearing, and insufficient electroless copper plating.
Heating of components may result in a partial or complete open circuit.
moisture wicking
Aged or dull bits can cause wicking. It can also be caused by lack of adhesion between prepreg and glass, poor glass etching and using the wrong laminate.
Short circuits may result, which may cause arcing and board damage when high voltages are present.
bent, bowed or twisted
Due to differences in copper weight, poor raw materials, unbalanced substrate heating, etc., irregular board shapes may occur.
Proper access to components may be prevented and lead to further deformation and the need for manual soldering or rework requirements.
during assembly
layered
Caused by cleaning too little to remove debris or cleaning too vigorously resulting in excessive adhesion between the copper foil and the plating.
Electrical opens may occur due to thermal or mechanical stress.
warping
Warpage can be caused by uneven placement of heavy components, low CTE ratio, or uneven heat distribution during reflow.
Good solder joints may be prevented, causing tombstoning or disconnected components. There may also be irregularities in the shape that prevent the mounting plate.