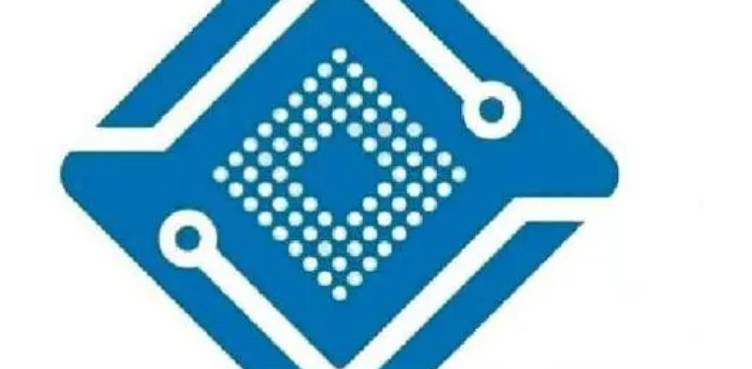
Although, the above mentioned by adding flame retardant and other substances, can reduce the flammable (or explosive) performance of PCB flux, but not add flame retardant PCB flux is not flammable (or explosive), but relative to the PCB flux without adding flame retardant is flammable (or explosive) degree is lower. Therefore, PCB flux itself is still flammable (explosive) products. In this way, it is required that our users should pay special attention to stay away from the open flame when using PCB flux, and eliminate all kinds of hidden dangers that may cause PCB flux combustion (explosion).
Through the above analysis of the flammable (explosive) performance of PCB flux itself, we can realize that the common PCB flux itself is flammable (except for water-based PCB flux or special PCB flux). In fact, in the actual production operation, the PCB flux ignition and combustion reasons are more from the operating process and the working condition of machinery and equipment. The following focuses on these two aspects caused by "PCB flux fire in wave soldering" reasons.
In terms of the welding process of "PCB flux over wave soldering furnace", the reasons that may cause PCB flux over wave soldering fire are as follows:
1. PCB flux coating amount is too much, which drops onto the heating tube during preheating.
2. There are too many rubber strips on the PCB, or the rubber strips fall off the heating pipe or heating plate, igniting the rubber strips.
3. The board speed is too fast, at the same time, the PCB flux coating amount is too much, PCB flux in the complete volatilization, continuous drops to the heating pipe or heating plate.
4. The board speed is too slow, causing the board surface temperature is too high.
5. The preheating temperature is too high.
6. PCB itself has poor flame retardant performance, and the distance between the heating pipe and PCB is too close.
The above points are the reasons that may cause PCB flux fire in the process. In addition to the sixth reason, which may be the quality problem of the board itself, other aspects can be improved through process adjustment. The second reason is the fire caused by too many adhesive strips falling off on PCB. The situation may be improved by reducing the use of adhesive strips or by using adhesive strips that are more viscous and resistant to high temperature. The fourth and fifth reasons indicate that the preheating temperature is too high, and reducing the preheating temperature may effectively reduce the hidden danger of fire. The first and third reasons mainly talk about the amount of welding coating too much, and cause too much coating in addition to the spray or foam amount of larger reasons, have to consider is the role of wave soldering stroke knife, which is also to discuss one of the reasons for the use of machine equipment.
From the use of machinery and equipment, the possible causes of PCB flux fire may be as follows:
First, the crest welding machine is not installed with air knife, or the Angle of the wind knife is wrong and the wind knife hole is blocked, the air pressure is not enough, the wind is too weak and can not work normally, so the PCB flux coating amount is too large. In wave welding machine, whether spray or foam wave welding machine, after coating PCB flux, it should be blown by air knife. Refer to Figure 1 and Figure 2 below, which are respectively the wind knife renderings of spray wave soldering machine and foam wave soldering machine.
Cause analysis and countermeasure of PCB flux ignition during over wave soldering
Cause analysis and countermeasure of PCB flux ignition during over wave soldering
As can be seen from the figure above, the air knife in normal operation blows against the PCB coated with PCB flux at an Angle of about 40 degrees. Good blowing effect, on the one hand, can make the PCB flux coated on the board more evenly, on the other hand, can blow off the excess PCB flux, so as to ensure that in the over-preheating area, Basically there will be no excess PCB flux dripping down in the preheating zone; It can not only reduce the risk of PCB flux fire, but also protect the heat pipe from erosion and extend the service life.