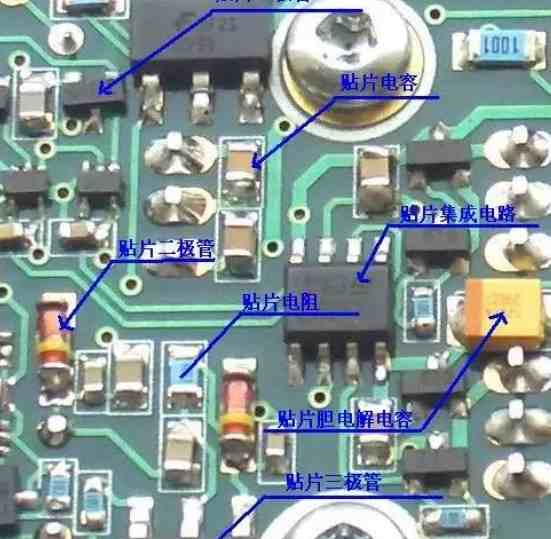
Xiaobian today mainly introduces the short-circuit phenomenon of single side/double side/multilayer circuit board test method:
There are some micro short circuit, short circuit phenomenon of PCB circuit board, with ordinary low-voltage computer testing machine can not guarantee its quality, once into the hands of users will affect our own credibility. The development of high voltage computer board measuring machine to ensure the quality of PCB circuit board, ensure 100% qualified rate. Now let's talk about the testing process.
The low-voltage test of the double-sided circuit board was all OK, and the second test was conducted with 300V high-voltage test to test short circuit. The third time was remeasured with ordinary low pressure, and the short-circuit plate measured the second time was also determined as short circuit. The welding between two lines was counted as short circuit by measuring the short circuit point with the resistance range of multimeter, and the average resistance value was 6.7 ohms. Therefore, it should be considered as complete short circuit rather than micro short circuit. Then use a high magnifying glass to check the short circuit phenomenon can not accurately check out the short circuit point (should be the finished product has solder resistance ink).
From the double-sided circuit board test process and its resistance value can be identified as: etching side erosion produces a spike, and then the grinding process makes the spike break down to form a bridge between the wires, and then printed green oil to make the bridge is not a complete short path bridge. This double-sided circuit board test for low pressure naturally can not measure the bridge short circuit. The second high voltage is first measured as a micro short circuit, and then high voltage breakdown welding (because the copper wire is small, it does not need a lot of power to welding to form a short circuit. If the tester manufacturer can increase the allowable power of its short-circuit test current to burn the bridge contact, we will hardly see this phenomenon). So the third time the low-voltage computer test was able to detect the short circuit, and its resistance was only an average of 6.7 ohms.
The simplest and most economical and feasible method is to purchase a new grinding machine or improve the existing grinding machine, adopt the swing grinding brush and the use of ash throwing brush or low eye number of nylon brush, and then rinse with high pressure, especially the washing section has a filter device, to prevent the foreign matter that can cause short circuit from polluting the surface again. The grinding machine can remove the copper wire formed by side erosion and the protruding edge (the sticky dust machine also has a certain removal effect). Single-side circuit board at the same time the newly purchased computer testing machine should be selected high pressure machine, can reduce the circuit board micro short circuit and short circuit. This short-circuit phenomenon usually appears in the single panel, double panel and high density circuit board.
PCB circuit board reprocessing and repair
When printed circuit boards are inspected and tested, whether bare or fully assembled, as defects are discovered, cost-effective repair methods need to be evaluated while providing users with a product that is as reliable as the original. For simple circuit boards with only a few defects, it is often uneconomical to rework them. However, many boards are of high complexity and a full load of assembly boards can be expensive, making it economical to reprocess a nonconforming product to pass the test.
Bare panels are usually not repaired because they pose a reliability risk for future assembly use and are relatively inexpensive compared to assembled panels. Combined with these factors, the repair and reprocessing of bare plates is not allowed in high reliability and military applications, and the reprocessing of bare plates can only be used commercially. However, the maintenance of the board must meet the requirements of the original design and meet the desired reliability and quality standards.
In addition, some used circuit boards need to be repaired and reworked. In most cases, the original component needs to be removed and a new one replaced, which is usually done manually. For plates with plated through holes, repairs can be done with simple tools such as soldering irons and capillating braids. For SMDS, on the other hand, special reworking tables are required, which rely on hot air reflow welding equipment. A lot of chemicals need to be used during the repair process, especially during cleaning, moisture removal, flux removal, lubricant wiping, freezing spray to locate heat sensitive components, etc.