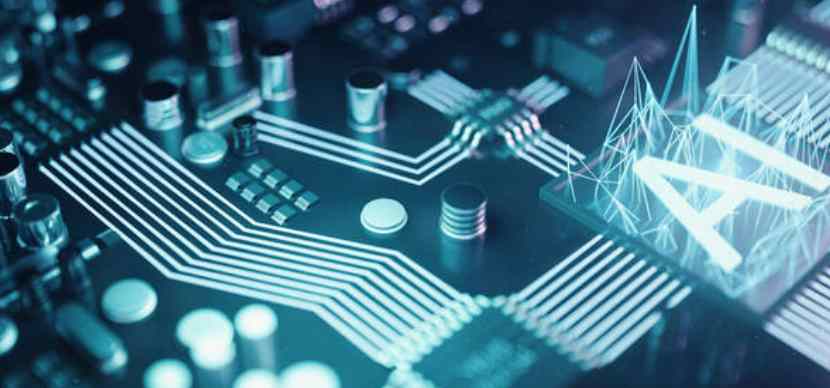
In the land of the A/D converter of analog and digital tube feet together, most of the A/D converter will advice: the AGND and DGND pin through the shortest lead connected to the same low impedance of the ground (note: Because most A/D converter chips do not connect analog and digital together internally, analog and digital must be connected via external pins), any external impedance connected to DGND will couple more digital noise to the analog circuit inside the IC via parasitic capacitors. According to this suggestion, need to turn the A/D converter AGND and DGND pins are connected to the analog ground, but the party * * such as the grounding end of the digital signal decoupling capacitor should receive analog or digital land problem.
If the system has only one A/D converter, the above problem is easily solved. As shown in Figure 3, divide the ground and connect the analog and digital parts together under the A/D converter. When adopting this method, it is necessary to ensure that the width of the bridge between the two ground is equal to the width of the IC, and that no signal line can cross the division gap.
If there are many A/D converters in the system, for example, how to connect 10 A/D converters? If analog and digital are connected at the bottom of every A/D converter, the resulting multi point connection makes the isolation between analog and digital meaningless. If you do not, you are violating the manufacturer's requirements.
The best way is to start uniformly. As shown in Figure 4, the land is uniformly divided into analog parts and digital parts. This layout meets IC device manufacturers' requirements for low impedance connections between analog and digital pins without creating loop or dipole antennas that could cause EMC problems.
If you have doubts about the unified approach to mixed-signal PCB design, you can use the method of ground layer division for the layout of the entire circuit board. During the design, pay attention to make the circuit board easy to use jumpers with less than 1/2 inch spacing or 0 ohm resistance to connect it together separately in the later experiment. Pay attention to zoning and wiring to ensure that no digital signal lines are above the analog section on all levels, and no analog signal lines are above the digital section. Moreover, no signal line should cross the ground gap or the gap between the split power sources. To test the functionality and EMC performance of the board, then retest the functionality and EMC performance of the board by connecting the two together with a 0 ohm resistor or jumper. Comparing the test results, it was found that in almost all cases, the unified solution was superior to the partitioned solution in terms of functionality and EMC performance.
Does the division of land still work?
This can be used in three situations: Some medical devices require very low leakage current between the circuits and systems connected to the patient; The output of some industrial process control equipment may be connected to noisy and high-power electromechanical equipment; Another situation is when the layout of the PCB is subject to specific restrictions.
There are usually separate digital and analog power supplies on mixed signal PCBS, and a split power surface can and should be used. However, the signal lines adjacent to the power layer cannot cross the gap between the power supplies, and all signal lines crossing the gap must be located on the circuit layer adjacent to the large area. In some cases, the analog power supply is designed with PCB connection lines rather than a surface to avoid the problem of power surface splitting.
Camera location and detection
In conventional on-line visual inspection applications, the camera is positioned above the circuit board to obtain an image of the printing position and can send the relevant image to the processing system of the visual inspection equipment. There, image analysis software compares the acquired image with a reference image stored at the same location in the device's memory.
In this way, the system can confirm whether too much or too little solder paste has been applied. The system can also reveal whether the solder paste position on the pad is aligned. It can discover whether there is excess paste between the two pads to form a bridge like connection phenomenon? The problem is what many PCB manufacturers call "bridging."
Detecting the cracks in the printed template is done in the same form. When excess paste is deposited on the surface of the stencil, the visual system can be used to detect if gaps are blocked by paste or if there is a tailing phenomenon.
After a defect is found, the equipment can immediately automatically require a series of cleaning operations on the screen below, or alert the operator that there is a problem that needs to be repaired. The inspection of printing templates can also provide users with very useful data on printing quality and consistency.
A key feature of the state-of-the-art on-line vision system is the ability to inspect highly reflective PCB boards and pad surfaces, in uneven light or in conditions where dry paste structure makes a difference. For example, HASL boards tend to be uneven, flat, contoured, and reflective. Proper lighting also plays a very important role in obtaining the highest quality images.
The light must be able to "target" the circuit board's reference and pad, in turn turning other subtle features into clearly recognizable shapes. You can then move on to visionsoftware rules systems to realize their full potential.
In certain situations, the visual system can be used to detect the height or volume of the paste on the pad, sometimes only an off-line detection system may be used to do this. Using this procedure means that a corresponding degree of accumulation is formed in a given printing template to verify that the volume of solder paste is missing on the same pad.