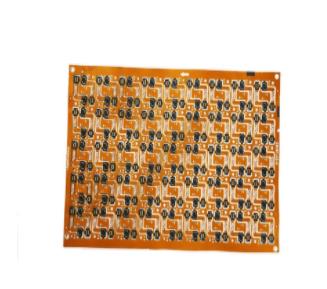
What inspections should be done before processing the SMT patch of soft board
The circuit board manufacturer, circuit board designer and PCBA processor will explain to you what inspection needs to be done before the processing of soft board SMT patches
1、 SMT chip component inspection
The main inspection items of components include solderability, pin coplanarity and usability, which shall be sampled by the inspection department. The solderability of components can be tested by clamping the component body with stainless steel tweezers and immersing it in a tin pot at 235 ± 5 ℃ or 230 ± 5 ℃, and taking it out after 2 ± 0.2s or 3 ± 0.5s. Check the tin sticking on the soldering end under a 20x microscope. It is required that more than 90% of the soldering end of the components be stained with tin.
SMT chip processing workshop can conduct the following visual inspection:
Visually or with a magnifying glass, check whether the welding ends or pin surfaces of components are oxidized or contaminated.
2. The nominal value, specification, model, accuracy, overall dimension, etc. of components shall conform to the product process requirements.
3. The pins of SOT and SOIC shall not be deformed, and the coplanarity of the pins of multi lead QFP devices with lead spacing less than 0.65mm shall be less than 0.1mm (optical detection through the mounting machine).
4. For the products required to be cleaned during SMT chip processing, the marks of components will not fall off after cleaning, and will not affect the performance and reliability of components (visual inspection after cleaning).
2、 Inspection of printed circuit board (flexible board)
The layout and size of bonding pad, solder mask, wire mesh and through hole of soft board shall meet the design requirements of smt printed circuit board. (For example, check whether the distance between pads is reasonable, whether the screen is printed on the pads, and whether the through hole is made on the pads).
2. The overall dimensions of soft boards shall be consistent, and the overall dimensions, positioning holes, datum marks, etc. of soft boards shall meet the requirements of production line equipment.
3. Allowable warping size of soft board:
1) Upward/convex: maximum 0.2mm/5Omm length maximum 0.5mm/length direction of the whole soft plate.
2) Downward/concave: maximum 0.2mm/5Omm length maximum 1.5mm/length direction of the whole soft plate.
4. Check whether the soft board is polluted or damped.
3、 Precautions for SMT chip processing
The SMT chip technician shall wear the electrostatic ring that is checked to be OK. Before the plug-in, the electronic components of each order shall be checked to be free of wrong/mixed materials, damage, deformation, scratches and other undesirable phenomena.
2. The plug-in board of the circuit board needs to prepare the electronic materials in advance, and pay attention to the correct capacitance polarity direction.
3. After the smt printing operation is completed, check whether there are any defective products such as missing inserts, reverse inserts, and misplacements, and transfer the good finished tin products to the next process.
4. Before SMT patch processing and assembly, please wear an electrostatic ring. The metal piece should be close to the wrist skin and kept well grounded. Both hands should work alternately.
5. Metal components such as USB/IF base/shielding cover/tuner/network port terminal must wear finger sleeves when inserting.
6. The position and direction of the inserted components must be correct, the components must be flat on the board surface, and the high components must be inserted into the K-pin position.
7. If the materials are found to be inconsistent with the specifications in the SOP and BOM, report to the team/leader in time.
8. The materials should be handled with care. Do not drop the soft board that has gone through the previous process of smt to cause damage to the components. The crystal oscillator should not be used if dropped.
9. Please tidy up the worktable and keep it clean before going on and off duty.
10. Strictly abide by the operation rules of the operation area. The products in the first article detection area, the waiting area, the defective area, the maintenance area, and the small material area are strictly prohibited to be placed at will without permission. The unfinished processes shall be noted during the handover of work. PCB manufacturers, PCB designers, and PCBA processors will explain what inspections need to be done before the processing of SMT patches on soft boards.