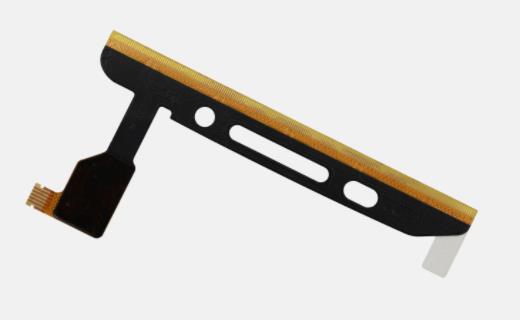
Items to be checked after flexible circuit board design and patch test form
PCB manufacturers, PCB designers and PCBA manufacturers will explain the items to be checked after the design of flexible circuit boards and the patch test forms
The following items need to be checked after flexible circuit board design:
1. DFM review of optical board: whether the production of optical board meets the technical requirements of flexible circuit board manufacturing, including line width, spacing, wiring, layout, through-hole, marking, wave soldering component direction, etc.
2. Check the consistency between the actual components and the bonding pad: whether the actual SMT mounting components purchased are consistent with the designed bonding pad (if not, please use a red label to indicate), and whether they meet the spacing requirements of the SMT mounting machine.
3. Generate 3D graphics: generate 3D graphics, check whether space elements interfere with each other, whether element layout is reasonable, whether it is conducive to heat dissipation, whether it is conducive to SMT reflow soldering heat absorption, etc.
4. Optimization of flexible circuit board mounting production line: optimize the loading sequence and the location of the material station. Input the existing pasting machine into the software, and distribute the components to be pasted to the existing boards. How many pasting methods does Samsung have, how many pasting methods do Samsung have in the world, how many locations and where to pick up materials. This can optimize the SMT chip processing program and save time. For multi line production, the distribution of installed components can also be optimized.
5. Operation instructions: automatically generate the operation instructions of the workers on the production line.
6. Revision of Inspection Rules: inspection rules can be modified. For example, if the component spacing is 0.1mm, the manufacturer and circuit board complexity can be set to 0.2mm according to the specific model, the line width is 6mi, and it can be changed to 5mil in high-density design.
7. Support Panasonic, Fuji and Universal patch software: it can automatically generate paste software to save programming time.
8. Automatically generate steel plate optimization graphics.
9. Automatically generate AOI and X-ray programs.
10. Check to support multiple software formats (Japan, KATENCE, China PROTEL).
11. Check the BOM and correct relevant errors, such as spelling errors of the manufacturer. BOM is converted to software format.
What are the test forms of flexible circuit board patch?
The process flow of flexible circuit board mounting is complex. During production and processing, various problems may occur due to improper equipment or operation, which cannot ensure that the products produced are qualified. Therefore, flexible circuit board mounting test is required to ensure that each product will not have quality problems. What are the test forms of flexible circuit board mounting?
Flexible circuit board mounting test mainly includes ICT test, FCT test, aging test, fatigue test, and harsh environment test.
1. ICT test: including circuit on-off, voltage and current values and fluctuation curves, amplitude, noise, etc.
2. FCT test: IC program burning is required, the function of the whole flexible circuit board patch board is simulated, and problems in hardware and software are found, and necessary production jigs and test racks are equipped.
3. Fatigue test: sample the flexible circuit board and patch board, conduct high-frequency and long-term operation of functions, observe whether there is failure, judge the probability of failure, and feed back the working performance of flexible circuit board and patch board in electronic products.
4. Testing in harsh environment: expose the flexible circuit board patch board to the temperature, humidity, drop, splash and vibration of the limit value, and obtain the test results of random samples, so as to infer the reliability of the whole batch of flexible circuit board patch board products.
5. Aging test: power on the flexible circuit board patch board and electronic products for a long time to keep them working and observe whether there is any failure. Only electronic products after aging test can be sold in batches. PCB manufacturers, PCB designers and PCBA manufacturers will explain the items to be checked after the design of flexible circuit boards and the patch test forms.