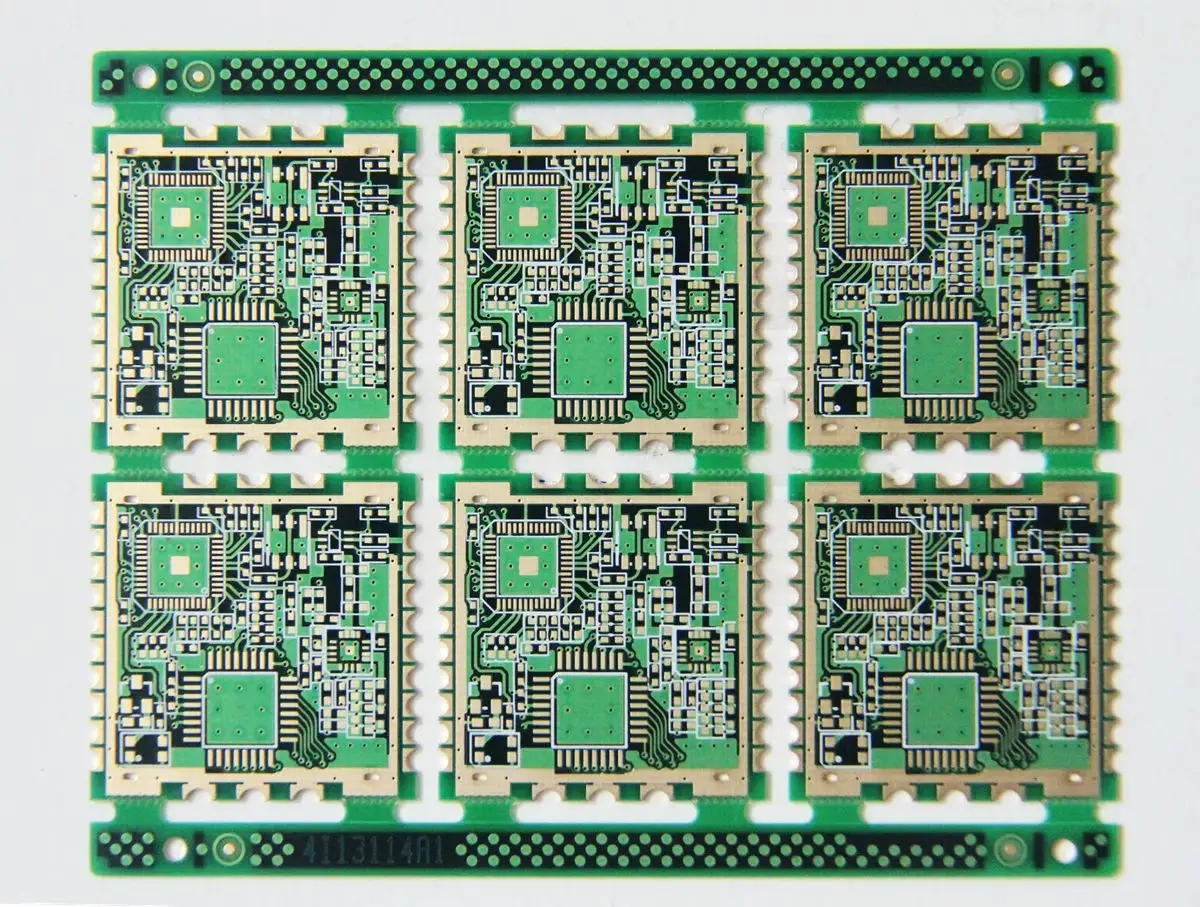
PCB factory engineer explains PCBA throwing control precautions
PCB manufacturer, PCB designer and PCBA manufacturer explain PCBA throwing control precautions to PCB factory engineers
What is the most common reason for PCBA dumping?
1. The suction nozzle is blocked and damaged
2. Identify system problems. There are sundries interfering with the identification. It is not clean and may be damaged
3. Position problem: the reclaiming is not in the center of the material, causing deviation and poor suction, which is inconsistent with the corresponding data parameters and is discarded by the identification system as invalid material
4. Vacuum problem, insufficient air pressure, the vacuum gas pipe channel is not smooth, the vacuum channel is blocked by a guide, or the vacuum leaks
5. Program problem, the program you edited has problems, such as incorrect parameter settings, inconsistent with the real object, etc
6. Material problems, irregular incoming materials or unqualified products
7. FEEDER problem, the strip is not stuck on the ratchet gear of FEEDER, or the position is wrong, FEEDER
Control PCBA dumping
Generally, the material loss of SMT factory cannot exceed 0.3%, which includes all material loss from incoming to outgoing
This ratio refers to common components. Special types of components include large ICs, BGA/CSP and other loss rates. In general, material loss should be controlled from two aspects: first Equipment loss refers to the material loss caused by equipment, which is generally called PCBA throwing. It is unavoidable and can only be controlled by controlling the equipment operation status
There is a good equipment maintenance system, including weekly, monthly, quarterly and annual maintenance. Companies with good requirements clean up every day
2. Establish equipment status management system: record the daily operation status of each equipment, and then make statistics
The main content of the record is the equipment absorption rate. The purpose of the mounting rate is to discover the long-term operation status of the equipment. First, the production plan can be adjusted for equipment in different statuses. Second, the equipment in poor operation status can be found, and timely repair and maintenance can be carried out to prevent minor problems from becoming major ones. Second, the material management and personnel operation management can be strengthened
Strengthen the management of materials in and out, regularly check materials according to different types or products, and timely find possible problems
2. Strengthen operators' operating skills and improve their sense of responsibility
3. Establish reward and punishment measures Establish a loss reward and punishment system for the material loss of the production line according to the equipment status of the production line to improve the employees' habit of saving materials in daily production
4. Do a good job in shift handover, and ensure that the material receiving and discharging are consistent with the actual output. There are many valuable components
In the SMT production process, how to control the production cost and how to improve the production efficiency is a matter of great concern to the bosses of enterprises, which has a lot to do with the PCBA dumping of the SMT mounter. Here we talk about the PCBA dumping. The so-called PCBA throwing means that the chip mounter does not stick the material after it is sucked in during the production, but instead transfers the material? To? Perform one of the above PCBA throwing actions in the material box or other places, or when the material is not sucked. PCBA dumping causes material loss, prolongs production time, reduces production efficiency and improves production cost. In order to optimize production efficiency and reduce cost, the problem of PCBA dumping rate must be solved.
The main reasons and countermeasures for PCBA dumping are as follows:
Cause 1: suction nozzle problem, deformation, blockage, damage, resulting in insufficient air pressure, air leakage, unable to pick up materials, improper picking up, identification failure, etc. Countermeasures: clean and replace the suction nozzle
2. Cause 2: identification system problems, poor vision, uncleanness of vision or laser lens, foreign matters interfering with identification, improper selection of identification light source and insufficient intensity gray scale, and possible identification system countermeasures: clean and wipe the identification system surface, keep it clean and free of foreign matters, adjust the light source intensity, and replace the identification system components
3. Cause 3: Position problem, the reclaiming is not in the center of the material, the reclaiming height is incorrect (generally 0.05 mm after touching the parts), which causes deviation, incorrect reclaiming, deviation, and the identification is inconsistent with the corresponding data parameters, and the identification system is regarded as invalid material. Countermeasures: Adjust the reclaiming position
4. Cause 4
5. Cause 5: Program problem. The component parameters in the edited program are not set correctly, which are inconsistent with the physical size, brightness and other parameters of the incoming material, resulting in the failure of identification and being discarded. Countermeasure: Modify the component parameters and search for the current parameter settings of the component
6. Cause 6: Problems with incoming materials, irregular incoming materials, unqualified products such as pin oxidation Countermeasures: IQC shall conduct inspection and contact the supplier
7. Cause 7: Feeder problem, feeder position deformation, poor feeding of feeder (feeder gear is damaged, the belt is not stuck on the ratchet gear of feeder, there are foreign matters under the feeder, the spring is aging, or the electrical is poor), resulting in the failure of reclaiming or poor PCBA throwing, and feeder failure
Countermeasures: Adjust the feeder, clean the feeder platform, and replace the damaged parts
In addition, when many faults occur and need to be solved, you can ask the on-site personnel first, and then find the problem directly through description and observation and analysis, so that you can find the problem more effectively, solve it, and improve production efficiency at the same time, without taking up too much machine production time. The PCB manufacturer, PCB designer and PCBA processing manufacturer will explain to you the PCBA factory engineers about PCBA throwing control precautions.