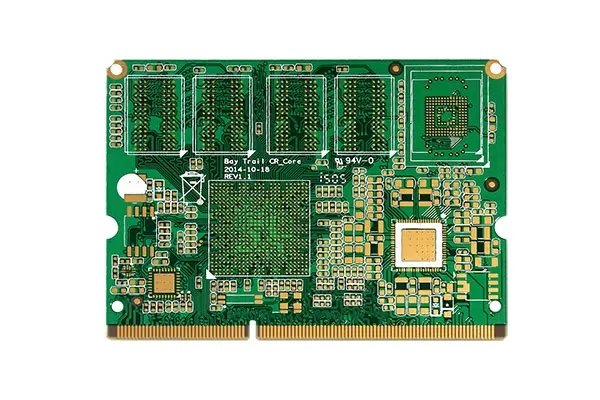
There are skills in PCB circuit board heat dissipation, you can do this
For electronic equipment, a certain amount of heat will be generated during operation, so that the internal temperature of the equipment will rise rapidly. If the heat is not dissipated in time, the equipment will continue to heat up, the devices will become invalid due to overheating, and the reliability of electronic equipment will decline. Therefore, it is very important to conduct a good heat dissipation treatment on the circuit board. The heat dissipation of PCB is a very important link. Now let's discuss the heat dissipation techniques of PCB.
At present, PCB boards widely used for heat dissipation through PCB boards are copper clad/epoxy glass cloth substrate or phenolic resin glass cloth substrate, and there are a few paper based copper clad boards. Although these substrates have excellent electrical and processing properties, they have poor heat dissipation. As a heat dissipation way for high heating elements, they can hardly be expected to transmit heat from the resin of PCB itself, but to dissipate heat from the surface of the element to the surrounding air. However, as electronic products have entered the era of miniaturization, high-density installation and high heating assembly of components, it is not enough to rely only on the surface of components with very small surface area for heat dissipation. At the same time, due to the large use of surface mounted components such as QFP and BGA, a large amount of heat generated by the components is transferred to the PCB board. Therefore, the best way to solve heat dissipation is to improve the heat dissipation capacity of the PCB itself in direct contact with the heating elements, which is transmitted or distributed through the PCB board.
2. Heat sink and heat conduction plate are added to high heating components. When there are a few components in the PCB with large heat generation (less than 3), heat sink or heat conduction tube can be added to the heating components. When the temperature cannot be reduced, heat sink with fan can be used to enhance the heat dissipation effect. When there are many heating devices (more than 3), large heat dissipation cover (plate) can be used. It is a special radiator customized according to the position and height of the heating devices on the PCB board, or different component high and low positions can be picked out on a large flat panel radiator. Buckle the heat shield onto the element surface as a whole, and contact each element to dissipate heat. However, the heat dissipation effect is not good due to the low consistency of components during assembly and welding. Usually, a soft thermal phase change heat conduction pad is added on the surface of the components to improve the heat dissipation effect.
3. For equipment cooled by free convection air, it is better to arrange the integrated circuit (or other devices) in longitudinal or transverse direction.
4. The reasonable routing design is adopted to realize heat dissipation. Because the resin in the plate has poor thermal conductivity, and the copper foil lines and holes are good conductors of heat, improving the residual rate of copper foil and increasing the thermal conductivity holes are the main means of heat dissipation. To evaluate the heat dissipation capability of a PCB, it is necessary to calculate the equivalent thermal conductivity (9 eq) of the insulating substrate for PCB, a composite material composed of various materials with different thermal conductivity.
5. The components on the same printed board shall be arranged in zones as far as possible according to their calorific value and heat dissipation degree. The components with low calorific value or poor heat resistance (such as small signal transistors, small-scale integrated circuits, electrolytic capacitors, etc.) shall be placed at the top (entrance) of the cooling air flow, and the components with high calorific value or good heat resistance (such as power transistors, large-scale integrated circuits, etc.) shall be placed at the bottom of the cooling air flow.
6. In the horizontal direction, high-power devices are arranged as close to the edge of the printed board as possible to shorten the heat transfer path; In the vertical direction, high-power devices shall be arranged as close as possible to the top of the printed circuit board, so as to reduce the impact of these devices on the temperature of other devices during operation.
7. The heat dissipation of the printed circuit board in the equipment mainly depends on the air flow, so the air flow path should be studied during the design, and the device or printed circuit board should be reasonably configured. When air flows, it always tends to flow in a place with small resistance. Therefore, when configuring components on the PCB, it is necessary to avoid leaving a large space in a certain area. The configuration of multiple printed circuit boards in the whole machine should also pay attention to the same problem.
8. The devices that are sensitive to temperature should be placed in the area with the lowest temperature (such as the bottom of the equipment), and should not be placed directly above the heating devices. Multiple devices should be staggered on the horizontal plane.
9. The devices with the highest power consumption and heat generation are arranged near the best heat dissipation position. Do not place the components with high heat generation on the corners and surrounding edges of the printed board, unless there is a heat sink near it. In the design of power resistance, select a larger device as far as possible, and make it have enough heat dissipation space when adjusting the layout of the printed circuit board.
10. Avoid the concentration of hot spots on the PCB, distribute the power evenly on the PCB as much as possible, and keep the PCB surface temperature performance uniform and consistent. It is often difficult to achieve strict uniform distribution in the design process, but the area with too high power density must be avoided to avoid the occurrence of hot spots that affect the normal operation of the entire circuit. If conditions permit, it is necessary to conduct thermal efficiency analysis of printed circuit. For example, the thermal efficiency index analysis software module added to some professional PCB design software can help designers optimize circuit design.
PCB manufacturers, PCB designers and PCBA manufacturers explain the skills of PCB heat dissipation, which can be done.