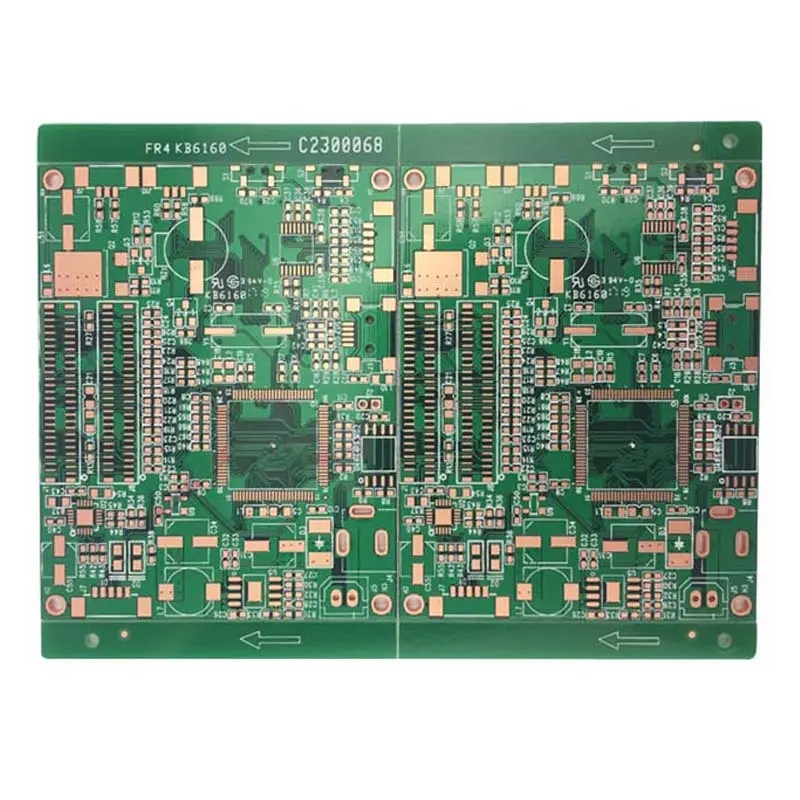
Manufacturing of flexible printed circuit boards that electronic engineers must know
The production process of flexible printed circuit board is basically similar to that of rigid board. For some operations, the flexibility of the laminate requires different devices and completely different treatment methods. Most flexible printed circuit boards adopt the negative method. However, there are some difficulties in the mechanical processing and coaxial processing of flexible laminates. One of the main problems is the processing of the substrate. Flexible materials are coiled materials of different widths, so rigid brackets are required for the transmission of flexible laminates during etching.
In the production process, the treatment and cleaning of flexible printed circuits are more important than the treatment of rigid boards (Lexin, 1993). Incorrect cleaning or operation against regulations may lead to failure in subsequent product manufacturing, which is determined by the sensitivity of materials used in flexible printed circuits. Flexible printed circuits play an important role in the manufacturing process. The substrate is affected by mechanical pressure such as wax baking, laminating and electroplating, and the copper foil is also vulnerable to the impact of knocking sound and dent, while the extension part ensures the maximum flexibility. Mechanical damage or work hardening of copper foil will reduce the flexible life of the circuit.
During manufacturing, a typical flexible single-sided circuit needs to be cleaned at least three times. However, multi substrate needs to be cleaned 3-6 times due to its complexity. In contrast, rigid multilayer printed circuit boards may require the same number of cleaning times, but the cleaning procedures are different, so more care should be taken when cleaning flexible materials. Even under extremely light pressure during cleaning, the spatial stability of flexible materials will be affected, and the panel will be elongated in z or y direction, depending on the pressure bias. The chemical cleaning of flexible printed circuit boards should pay attention to environmental protection. The cleaning process includes alkaline dyeing bath, thorough rinsing, micro etching and final cleaning. The damage of membrane materials often occurs in the process of putting the panel on the shelf, when stirring in the pool, when removing the shelf from the pool or when there is no shelf, and when the surface tension is damaged in the cleaning pool.
The holes in the flexible plate are usually punched, which leads to higher processing costs. It is also possible to drill holes, but this requires special adjustment of drilling parameters to obtain a stain free hole wall. After drilling, remove the drilling dirt in a water cleaner with ultrasonic stirring.
It has been proved that mass production of flexible boards is cheaper than rigid printed circuit boards. This is because flexible laminates enable manufacturers to produce circuits on a continuous basis. This process starts with laminate coils and directly generates finished boards. In order to manufacture printed circuit boards and etch flexible printed circuit boards as a continuous processing schematic, all production processes are completed in a series of sequential machines. Screen printing may not be a part of this continuous transmission process, which causes the interruption of the online process.
In general, due to the limited thermal resistance of the substrate, soldering in flexible printed circuits is more important. Manual welding requires sufficient experience, so if possible, wave soldering should be used. When welding flexible printed circuit, the following matters shall be noted:
1) Because polyimide is hygroscopic, the circuit must be baked before welding (lasting for 1h at 250 ° F).
2) When pads are placed on large conductive areas, such as ground plane, power layer or heat sink, the heat dissipation area should be reduced. This limits heat dissipation and makes welding easier.
3) When manually welding pins in dense places, try not to continuously weld adjacent pins, and move the welding back and forth to avoid local overheating.
Information on flexible printed circuit design and processing can be obtained from several sources, but the best source of information is always the producer/supplier of processing materials and chemicals. With the information provided by suppliers and the scientific experience of processing experts, high-quality flexible printed circuit boards can be produced
Circuit board manufacturing, circuit board design, PCBA manufacturers will explain the manufacturing of flexible printed circuit boards that you must know.