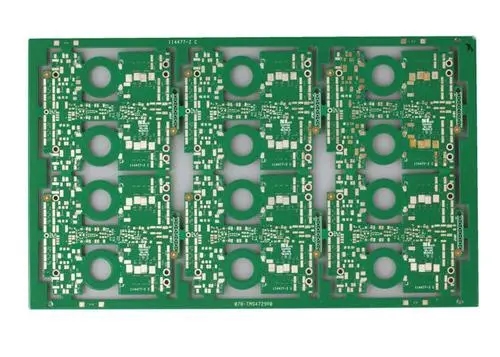
Solution to Micro Short Circuit of CAF Circuit Board
To solve or prevent CAF, we can actually start from the above five necessary conditions. As long as we eliminate any of them, we can prevent CAF from occurring.
1. Improve the ability of circuit board materials in Anti CAF
In fact, the selection of circuit board is very important to prevent CAF, but generally, every penny is paid for every product. Generally, the substrate with high CAF protection capacity needs to be specially customized. The following are suggestions on the selection of circuit board substrate to prevent CAF:
Reduce the content of impure ions in materials.
The fiberglass cloth is fully impregnated with resin and is well bonded.
When making the base plate of the circuit board, we will first weave multiple bundles of glass fiber bundles into cloth, then introduce them into the resin tank for impregnation, and then gradually pull up or pull out the glass fiber cloth stained with resin, so that the resin can fill the gap of the glass fiber bundle. If the parameters at this stage are not set well, it is easy to form a gap in the glass fiber bundle, so that the CAF has a gap to multiply.
Use low hygroscopic resin. Related reading article: Introduction to the structure and function of PCB board
2. PCB layout design avoids bias voltage and hole spacing
The through-hole, circuit size and position and stack structure design of the circuit board will also have an absolute impact on CAF, because almost all requirements come from the design. As the products become smaller and smaller, the density of circuit boards becomes higher and higher. However, PCB manufacturing process capability has its limits. The smaller the distance between adjacent lines with a bias voltage, the higher the probability of CAF. Basically, the higher the bias voltage or the smaller the distance, the higher the probability of CAF.
According to the information provided by current circuit board manufacturers, the following are the PCB size design values recommended by most circuit board manufacturers for CAF protection:
Distance from hole to hole edge (minimum): 0.4mm
Hole to Metal: 12mil (0.3mm)
Recommended aperture: 0.3mm
In addition, according to practical experience, it is found that the channel (gap) of CAF almost occurs along the same glass fiber bundle. Therefore, if the arrangement of through-hole or welding pad can be cross routed at a 45 degree angle, it will help reduce the incidence of CAF.
CAF improvement measures - design. According to practical experience, the channel (gap) of CAF almost always occurs along the same glass fiber bundle. Therefore, if the arrangement of through-hole or welding pad can be cross routed at a 45 degree angle, it will help to reduce the incidence of CAF.
3. Wicking control in PCB manufacturing process
High temperature will be generated during mechanical drilling or laser hole burning of PCB. When the Tg point of resin is exceeded, it will melt and form glue slag. This glue slag will adhere to the inner copper edge and hole wall area, which will cause poor contact during subsequent copper plating. Therefore, de smear operation must be carried out before copper plating. The initial station for removing glue slag must use a swelling agent to soak for 1~10 minutes to make various glue slag swell and relax, In order to facilitate the smooth penetration and erosion of Mn+7. However, the operation of removing glue residue will also cause certain corrosion to the through-hole and may lead to copper penetration (wicking). Some circuit board manufacturers will increase the temperature of the bulking tank in order to speed up the bulking operation, resulting in excessive opening of the bulking agent and subsequent copper migration.
IPC-A-600 has the following acceptance standards for copper penetration (Wicking):
Class 1, copper penetration shall not exceed 125 μ m (4.291 mil)
Class 2, copper penetration shall not exceed 100 μ m (3.937 mil)
Class 3, copper penetration shall not exceed 80 μ m (3.15 mil)
Wicking control in PCB manufacturing process
With the progress of science and technology, 0.1mm (100 μ m) It seems that the copper penetration of is no longer in line with the actual needs. In terms of the distance from the 0.4mm hole to the hole edge, the distance is only 0.4-0.1-0.1=0.2mm after deducting the size of the copper penetration. In terms of the current process capability of circuit board manufacturers, it should be possible to control the copper penetration at 50 μ M (2mil) or less. On the other hand, the distance between holes in the Layout circuit board of the system factory is also reduced to 100 μ M (4mil), which is really a big test for CAF prevention.
In addition, if the feed speed is too fast or the milling cutter exceeds its service life during mechanical drilling operation of PCB, it is also easy to tear the glass fiber and create gaps due to the external force of the milling cutter.
4. Control of waterproof moisture during PCB processing
Solder paste printing, part attachment, high temperature reflow, etc. during PCB assembly may leave some pollutants on the circuit board. These pollutants may include solder, glue, dust, condensation and other substances that are prone to electrolysis, which may cause electrochemical migration. Sealants can be used to seal the junction that may produce gaps and form CAF, to prevent water vapor from infiltrating.