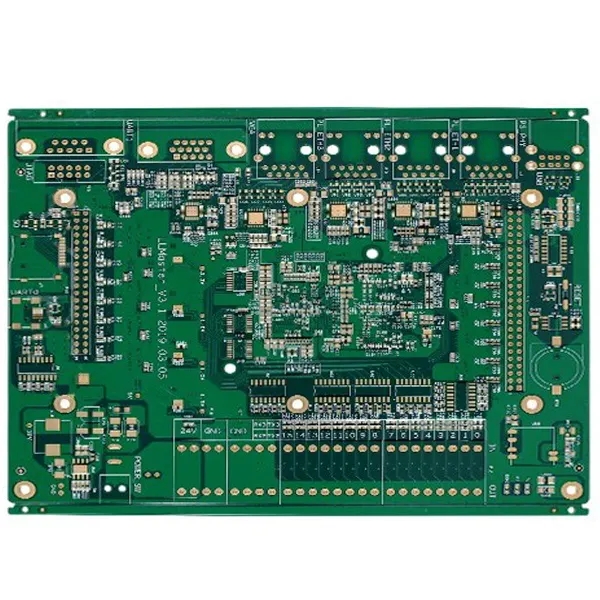
PCB manufacturer: function, usage and storage steps of solder paste
Solder paste
Solder paste is also called solder paste. It is called solder paste in English. It is a gray paste. Solder paste is a new type of welding material with SMT, which is a paste mixture formed by mixing solder powder, flux, other surfactants, thixotropic agents, etc. Mainly used in SMT industry PCB surface resistance, capacitance, IC and other electronic components welding.
Composition of solder paste
Generally speaking, the composition of solder paste can be divided into two major parts, namely, flux and solder powder (FLUX&SOLDER POWDER).
Function of solder paste
1. Activator (ACTIVATION): This component is mainly used to remove the oxidation substances on the surface of PCB copper film pad and the welding parts of parts, and has the effect of reducing the surface tension of tin and lead;
2. Thixotropic agent (THIXOTROPIC): This component is mainly used to adjust the viscosity and printing performance of solder paste, so as to prevent trailing, adhesion and other phenomena in printing;
3. Resin: This component mainly increases the adhesion of solder paste, and protects and prevents PCB from reoxidation after soldering; This component plays an important role in fixing parts;
4. SOLVENT: This component is the solvent of the flux component, which plays a role in regulating the uniformity during the mixing process of the solder paste, and has a certain impact on the service life of the solder paste.
Usage of solder paste
When the solder paste is taken out of the solder paste refrigerator, it should be opened in its sealed state after it returns to room temperature, about 3-4 hours; If the solder paste is opened just after being taken out of the freezer, the temperature difference will cause the solder paste to dew and condense into moisture, which will cause solder beads during reflow soldering; However, the solder paste can not be heated to return to the room temperature. Rapid heating will deteriorate the performance of the flux in the solder paste, thus affecting the welding effect. This is also a problem that the solder paste manufacturer should pay attention to in the use process. The components in the solder paste may be separated during cold storage. Before use, fully stir the solder paste for 1-2 parts to fully mix. Do not mix the remaining solder paste with the new solder paste in the same package. When the solder paste is not needed, it should be resealed. When the bottle cap can not be sealed well, replace the bottle cap liner to ensure the best possible sealing.
Precautions for use of solder paste
1. Scraper pressure: ensure that the printed solder joint edge is clear, the surface is flat and the thickness is appropriate;
2. Scraper speed: ensure that the solder paste is rolling rather than sliding relative to the scraper, generally 10-20mm/s is appropriate;
3. Printing mode: contact printing is preferred;
In addition, the solder paste shall be fully stirred during use, and then added to the printing screen according to the set amount of printing. If the spot injection process is adopted, the spot injection amount must be adjusted.
In the case of long-term printing, because the volatilization of the flux in the solder paste will affect the demoulding performance of the solder paste during printing, the container for storing the solder paste cannot be reused (it can only be used once). The solder paste left on the screen after printing should be stored in other cleaning containers. When it is reused next time, check whether the remaining solder paste is caked or solidified. If it is too dry, The solder paste thinner provided by the supplier shall be added to dilute and then used.
Operators shall avoid direct contact between solder paste and skin during operation. In addition, the printed substrate should be welded within days. Remember, the best working conditions of solder paste are: temperature 20~25 ℃, relative humidity 50~70%, clean, dust-free and anti-static.
Storage method of solder paste
Solder pastes should be stored in a sealed form in a refrigerator with constant temperature and humidity (note that refrigeration is not quick freezing). Solder pastes can be stored for 6 months at a temperature of 2 ℃~8 ℃. If the temperature is too high, the alloy powder in the solder paste will not react with the flux chemically, which will reduce its viscosity and activity and affect its performance; If the temperature is too low, the resin in the flux will crystallize, which will deteriorate the shape of the solder paste. In the process of storage, it is more important to pay attention to maintaining the "constant temperature". If the solder paste repeatedly changes in temperature from various environments in a short period of time, the performance of the flux in the solder paste will also change, which will affect the welding quality of the solder paste.
The above is about the function, usage and storage steps of solder paste explained by PCB manufacturers and PCB designers.