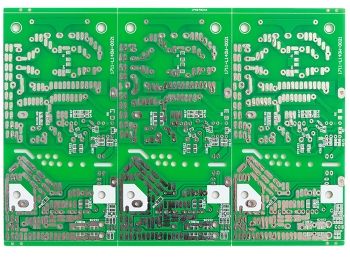
How to deal with expired AB glue epoxy
Can the expired AB glue epoxy with PCB problems be saved besides scrapping?
What should you do with your AB epoxy resin if it expires? Scrap? Or continue to use it?
Many people think it's a pity that the Epox will be scrapped when it expires. What will be the problem if the expired Epox is not scrapped?
When using expired Epoxy, two major problems may basically occur: failure to fully cure and decrease in surface resistivity (SIR) or volume resistivity (Volume Resistivity).
I believe that most of our friends can understand the problem of the inability of the epoxy to cure, because the epoxy will salivate outside the product and cause cosmetic problems. In addition, it will lose the protection purpose of the epoxy glue dispensing/filling. However, it is not easy to understand the other "reduction of surface resistivity (SIR) or volume resistivity". However, we can talk about the impact of the reduction of resistivity first. The biggest problem is that it will cause leakage current. If it is light, it may increase the power consumption of the product, reduce the battery endurance, or even cause unstable operation of the product, Risk of crash or restart.
How can I ensure that expired Epoxy can still be used?
Our approach is to first distinguish the Date code of the Epox, then take an empty circuit board, find out two independent pads (pads) with a spacing of 0.1mm. It is recommended to measure whether there is impedance, cut off the connecting lines (traces) around them, and then weld a wire on each of them to facilitate the subsequent impedance measurement. Finally, put the expired Epox glue on the upper point, and the Epox must cover all welded pads, Then operate according to the normal curing procedure, so that you can not only test whether the epoxy can be fully cured, but also measure its resistivity and whether it is suitable for your product needs.
It is recommended that the minimum distance between two welding pads should refer to the actual situation of their respective companies. Be sure to find out the minimum distance between two welding pads at the epoxy coverage area. As for whether the flux after welding should be cleaned, it is recommended to make a group of clean and non clean. The impedance of pure epoxy can be measured if the flux has been cleaned, and the worst case is simulated SMT or repaired if the flux has not been cleaned. As for the measured impedance, our company's regulation is 1 × 108 Om or above is OK, but it is recommended to consult their RDs to see if your product design has higher impedance requirements.
Finally, why do expired Epoxies cause the above problems?
The following is just a personal opinion. The answer may not be correct. It is only for reference. If you have an expert on Epox, please come out and help correct the error.
Because the content of the epoxy will contain many macromolecular chemical components and some will be doped with a small amount of metal components, these heavier chemical components will slowly precipitate to the bottom of the liquid epoxy with the influence of time and gravity, and will even partially harden as the epoxy is placed for a long time, so the barrel of the early epoxy will require the package to be stored upside down, Before taking it out for use, it should be placed on the roller machine or vibrating shaker and shaken for more than 10 minutes, so as to evenly distribute these sediments into the liquid of Epoxy.
If hardened sediment is still found after the above shaking or rolling, be careful not to use this can of glue. If it is really necessary to use, the hardened sediment must be broken to dissolve it into the original epoxy liquid, otherwise there is a great chance to produce products with incomplete curing.
If it is necessary to use these expired AB glue epoxys, is there any way to verify their quality?
Our method is to select the AB glue of different date codes according to the date, and select one can for each type to try to inject glue. The key points of judgment are as follows:
Check whether the epoxy is completely cured. Cut the filled glue for inspection.
(Refer to the illustration of the top picture) Select two welding pads on the circuit board with a distance of 0.1mm, connect a wire to each pad, and then add the epoxy on it until the two pads and solder joints are completely covered. After the epoxy is cured, measure the insulation resistance with a "megger". Our requirement is that it must be greater than 100M Om. Of course, it depends on the design of each product.
If the above two items are positive, fill the glue slowly one pot at a time. To ensure that the glue will really cure completely, make and keep the best record of each glue filling sample (dummy epoxy) to check the curing quality of the glue filling. In addition, the production line can also be required to place the cured products upside down in the manufacturing process. At this time, if there are products with incomplete curing, the epoxy will flow out, which can be visually inspected, so that the production line of the circuit board manufacturer can intercept the defective products, instead of waiting for customers to complain when they receive them.