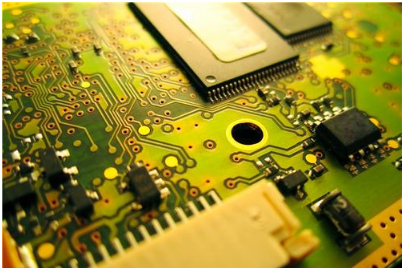
The electronics industry is trying to recover from the economic crisis, and the pressure to provide comprehensive support for the process from design to manufacturing is also increasing. Electronic companies around the world have to bring differentiated products to the market at a faster speed and at a lower cost, and this trend will continue due to economic weakness. Even in China's PCB market, system design and manufacturing support tools need to use the latest technology to improve productivity.
In a survey conducted by Aberdeen Group, many leading electronics companies identified six design technology best practices that can actively meet business objectives. With the slow recovery of the economic situation, these basic PCB technology practices will become an essential part of the development of companies in 2012.
The following is an overview of these six key strategies to make the company's work more intelligent. We believe these strategies will become the key to development in 2012.
Technical Strategy 1: Product Collaborative Development Process
Collaboration usually refers to the ability to turn serial operations into parallel, and has two modes. The first is the ability to let multiple designers work in the same design process at the same time. This practice is not a new thing, but the new technology has a huge difference in effectiveness compared with the original. Designers can always manipulate PCB design databases and split them. Then every designer works in the design phase - but eventually the database must be re merged. The merge process is time-consuming and error prone, but the end result can shorten the design cycle.
"The future solution is to simulate in software, such as virtual prototype."
At present, we have the ability to let multiple designers work in the same database at the same time, without database splitting. This applies to many processes in PCB design, including schematic input, constraint (high-speed and manufacturing rules) input and management, and physical layout. In addition, each designer can see the results of real-time operation of colleagues. This not only significantly shortens the design cycle time, but also improves the designer's productivity and product quality. Some users of this technology reported saving 30-70% of design time. In order to remain competitive in 2012, companies must achieve similar design cycle improvements (Figure 1).
Collaborative design usually requires the PCB design database to be split and then reorganized, but now it can be kept complete when multiple designers operate
The second mode of collaboration is the ability to run several different processes in a parallel manner different from the sequence. Schematic diagrams, constraints, layouts, and analyses can all be parallelized to further improve the productivity of designers and shorten the design cycle. However, this mode requires complex design data management with version management, synchronization calibration, permissions and update control, which will be described later in this article.
Technical strategy 2: virtual prototype
Usually companies verify their products by building and testing multiple prototypes. Design a PCB, build a physical prototype, test it in the laboratory, determine what changes need to be made, redesign, and then repeat the relevant process.
There are several problems with this method. First of all, it is time-consuming and expensive to build and debug a prototype. If the listing time is very urgent, it is likely to miss the market opportunity. Second, testing in the laboratory may not reveal all potential problems. For example, you want the product to be used for many years in harsh environments such as severe vibration, but the "vibration and heat treatment" laboratory may not be able to run long enough to find long-term problems. Similarly, signal integrity also has this problem. Extreme critical conditions are unlikely to be available in the laboratory.
The future solution is to simulate in software, such as virtual prototype. This operation can be performed in the PCB design process, and will cover many possible areas: signal (digital, analog, RF) and power network integrity; Thermal management in integrated circuit, package, PCB and full system simulation; Vibration and shock (Figure 2); PCB manufacturing and assembly practice; 3D mechanical interface, etc. Implementation throughout the design process can ensure that the design continues without backup and correction. In addition, the software can detect extreme critical conditions and simulate problems in the laboratory for weeks and months in a matter of hours. Although designers like to get real objects as soon as possible, and the implementation of extensive virtual prototype may be delayed, the latter can shorten the cycle, reduce costs, and improve the productivity and product quality/reliability of designers.
The vibration virtual prototype can use several hours of software simulation to replace weeks and months of operation in the laboratory, and highlight the potential failure problems of each component (red, yellow, blue)
Technical Strategy 3: Process Support from Design to Manufacturing
Time to market and PCB product cost are key to many industries. Even the military/aviation and automobile industries have faced the restrictions of long development time and/or high costs in the past, and now they have more positive goals for this issue. In addition, PCB designers must never forget that even if the data enters the manufacturing process, their responsibilities are not over. At the same time, from the perspective of EDA suppliers, the important thing is not to support the end of the design phase, not to allow designers to easily fulfill their responsibilities for manufactured products, but to optimize their production lines with manufacturers to achieve the lowest cost of product delivery.
Indicates that the process is evolving. Starting with support to help manufacturers define rules and practical capabilities, it has a positive impact on production and reliability in the manufacturing and assembly processes. These DFM (Design for Manufacturability) rules will be used by PCB designers for the design process. DFM software can find problems in the design environment, and then the designer can correct them. Coincidentally, most manufacturers also use the same rules and software to check the received design data. This ensures that once the design enters the PCB manufacturing process, it can be carried out continuously without design rework.
: Comprehensive design to manufacturing process support can ensure high output, high product reliability and low production cost.
Once the design enters the manufacturing process through intelligent interfaces, such as ODB++, the manufacturer can use software to model the production line and optimize its utilization. While the production line is running, the software will continuously monitor issues such as on-time delivery of parts, machine downtime, and product traceability. Even if a quality defect occurs, it can ensure that the equipment or process with an acceptable failure rate is tracked and highlighted.
Technical Strategy 4: Complexity Management
For differentiated products that defeat competitors, the company must use the latest and most advanced technology to compress more functions into a smaller space, while still meeting the positive market opportunities, which will become more important in 2012. IC technology continues to improve in terms of high density, high speed, more pins in a smaller space, and higher power consumption. PCB (printed circuit board) manufacturing technology, such as HDI/microporous technology, can increase the density, but the design is also more complex. In the face of this increasing complexity, how can we maintain and improve the productivity of designers? The answer is to increase the function of design tools as well.
For example, not long ago, a typical design might include high-speed networks that must comply with length and proximity rules. These networks can be easily managed by PCB designers. Now, large reading designs have more than 50% high-speed networks, even up to 90% Another example is the increase in the number and density of BGA stitches. This will be a challenge when the PCB is fanned out. This kind of situation poses a complex problem. Without advanced design tools, the productivity will be seriously reduced and the time to market will be significantly prolonged.
Strategic advantage - reliability is critical.
For many years, key mission applications have depended on Rogers' microwave materials. Rogers' military grade laminate can withstand the test of time and temperature to maintain stable and consistent performance, which is critical for aviation and defense applications.
The stable performance of Rogers microwave materials provides the high performance and high reliability required for most mission critical applications. Can you afford to reduce the use of materials?
Automatic high-speed interconnection routing following rules to meet performance goals
If we look at the first example of adding high-speed network content, existing tools can help designers comply with all the latency and signal integrity rules. The engineer sets these rules in the binding terms, and then the CAD designer sends the individual interconnection or bus structure according to the specified route, automatically adjusts the high-speed network, and then matches the length of the minimum/maximum limit, as well as the differential peer-to-peer network. Such a task cannot be completed manually.