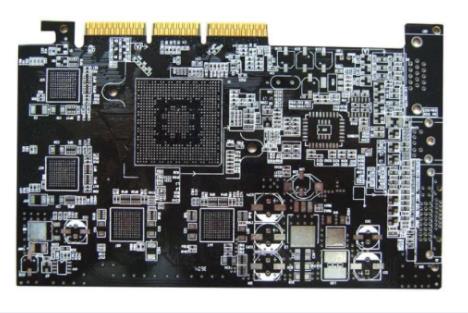
Failure analysis of PCB failure cases
As the carrier of various components and the hub of circuit signal transmission, PCB has become the most important and critical part of electronic information products The quality and reliability of PCB determine the quality and reliability of the whole equipment
With the miniaturization of electronic information products and the environmental requirements of lead-free and halogen-free, printed circuit boards are also developing towards high-density, high Tg and environmental protection. However, due to cost and scientific and technological reasons, a large number of failures have occurred in the production and application of PCB, causing many quality disputes. In order to clarify the cause of the failure, so as to find a solution to the problem and distinguish responsibilities, it is necessary to analyze the failure cases that have occurred.
Basic procedure of failure analysis
In order to obtain the accurate causes or mechanisms of PCB faults or failures, the basic principles and analysis process must be followed, otherwise valuable fault information may be missed, resulting in analysis failure or possible erroneous conclusions. The general basic process is: first, according to the fault phenomenon, the fault location and fault mode must be determined through information collection, functional test, power performance test and simple visual inspection, that is, the fault location or fault location.
For simple PCB or polychlorinated biphenyl, the fault location is easy to determine, but for more complex BGA or MCM packaging devices or substrates, these defects are not easy to observe through a microscope, nor to determine temporarily In this case, other methods are needed to determine
Circuit board
Then we must analyze the failure mechanism, that is, use various physical and chemical methods to analyze the mechanism that causes PCB failure or defects, such as virtual welding, pollution, mechanical damage, moisture stress, medium corrosion, fatigue damage, CAF or ion migration, stress overload, etc.
Then it is failure cause analysis, that is, based on failure mechanism and process analysis, find out the cause of failure mechanism, and conduct test verification if necessary. In general, test verification should be carried out as much as possible to find the exact cause of the failure.
This provides a targeted basis for further improvement. Finally, prepare the fault analysis report according to the test data, facts and conclusions obtained in the analysis process, which requires clear facts, strict logical reasoning and strong organization. Don't imagine it out of thin air.
In the process of analysis, attention should be paid to the basic principles of the analysis method, that is, from simple to complex, from outside to inside, never destroy the sample and then use it. Only in this way can we avoid the loss of key information and introduce new artificial failure mechanisms.
The optical microscope is mainly used for the appearance inspection of PCB, to find the fault location and relevant physical evidence, and to preliminarily determine the fault mode of PCB. The visual inspection mainly checks the PCB contamination, corrosion, the location of the board burst, the regularity of the circuit wiring and faults, and if it is batch or single, whether it is always concentrated in a certain area.
X-ray
For some parts that cannot be visually inspected, as well as internal and other internal defects of PCB through-hole, X-ray fluoroscopy system must be used for inspection.
The X-ray fluoroscopy system uses different data thicknesses or different data densities for imaging according to different principles of X-ray moisture absorption or transmittance. This technology is more used to check the internal defects of PCB solder joints, the internal defects of through-hole, and the positioning of defective solder joints of BGA or CSP devices in high-density packaging.
Slice analysis
Slice analysis is a process of obtaining PCB cross section structure through a series of methods and steps such as sampling, inlaying, slicing, polishing, etching and observation. Through slice analysis, we can obtain rich microstructure information (through-hole, electroplating, etc.) reflecting PCB quality, which provides a good basis for the next step of quality improvement. However, this method is destructive. Once sliced, the sample will inevitably be damaged.
Scanning acoustic microscope
At present, C-mode ultrasonic scanning acoustic microscope is mainly used for electronic packaging or assembly analysis. It uses the amplitude, phase and polarity changes generated by high-frequency ultrasonic reflection on the data discontinuity interface to image. The scanning method is to scan the information on the XY plane along the Z axis.
This scanning acoustic microscope can be used to detect various defects in components, data, PCBs and PCB, including cracks, delaminations, inclusions and cavities. If the frequency width of the scanning acoustic is sufficient, the internal defects of the solder joint can also be directly detected.
Typical scanning acoustic images use a red warning color to indicate the presence of defects. Since a large number of plastic packaging components are used in the SMT process, a large number of moisture reflux sensitivity problems will occur during the transition from lead containing process to lead-free process. That is to say, when the lead-free process temperature is high, the hygroscopic plastic packaging device will have internal or substrate delamination cracks during the reflow process, and ordinary PCB will often explode under the high temperature of the lead-free process.
At this time, scanning acoustic microscope highlights its special advantages in nondestructive testing of multilayer high-density PCB. In general, visible bursts can only be detected by visual inspection of the appearance.
Micro infrared analysis
Micro infrared analysis is an analysis method combining infrared spectroscopy and microscope. It uses different absorption principles of infrared spectra of different data (mainly organic compounds) to analyze the composition of compounds in data, and combines microscope to make visible light and infrared light the same. As long as the light path is within the visual field, the trace organic pollutants to be analyzed can be found.
Without the combination of microscopes, infrared spectroscopy usually can only analyze a large number of samples. However, in many cases of electronic technology, micro contamination may lead to poor solderability of PCB pads or lead pins. It can be imagined that without the infrared spectrum of the microscope, it is difficult to solve the process problem. The main purpose of micro infrared analysis is to analyze the organic pollutants on the welding surface or solder joint surface, and analyze the causes of corrosion or poor weldability.
Scanning electron microscope (SEM)
Scanning electron microscope (SEM) is one of the most useful large-scale electron microscope imaging systems for failure analysis. It is most commonly used for topographic observation. Scanning electron microscopes are very powerful today. Any fine structure or surface feature can be magnified. Observe and analyze hundreds of thousands of times.
In the failure analysis of PCB or solder joint, SEM is mainly used to analyze the failure mechanism. Specifically, it is used to observe the topographical structure of the pad surface, the metallographic structure of the solder joints, measure intermetallic compounds and solderable coatings, and conduct tin whisker analysis and measurement.
Unlike optical microscopes, scanning electron microscopes produce electronic images, which are only black and white. The samples of scanning electron microscopes need to conduct electricity, while non conductors and some transistors need to be coated with gold or carbon. Otherwise, the charge accumulation on the sample surface will affect the observation of the sample. In addition, the image of scanning electron microscope is more far-reaching than that of optical microscope, and it is an important analysis method for inhomogeneous samples such as metallographic structure, micro fracture and tin whisker.
Thermal analysis
Differential scanning calorimeter (DSC)
Differential scanning calorimetry (DSC) is a method to measure the relationship between the power difference between input data and reference data and the temperature (or time) under program temperature control. This is an analytical method to study the relationship between heat and temperature. Based on this relationship, the physical, chemical and thermodynamic properties of the data can be studied and analyzed.