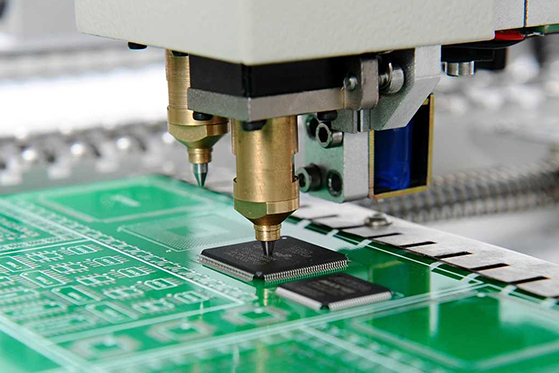
The PCB manufacturer teaches you how to draw beautiful PCB boards
1、 Layout
10 rules for component layout:
1. The layout principle of "large before small, difficult before easy" shall be followed, that is, the layout of important unit circuits and core components shall be given priority.
2. The layout shall refer to the principle block diagram and arrange the main components according to the main signal flow direction of the board.
3. The arrangement of components shall be convenient for debugging and maintenance, that is, large components cannot be placed around small components, and there shall be enough space around components to be debugged.
4. For circuits with the same structure, "symmetrical" standard layout shall be adopted as far as possible;
5. Optimize the layout according to the standard of uniform distribution, balance of gravity center and beautiful layout;
6. Plug in components of the same type shall be placed in one direction in the X or Y direction. Polarized discrete components of the same type shall also strive to be consistent in the X or Y direction, so as to facilitate production and inspection.
7. The heating elements should generally be evenly distributed to facilitate the heat dissipation of the single board and the whole machine. The temperature sensitive devices other than the temperature detection components should be far away from the components with large heat.
8. The layout shall meet the following requirements as far as possible: the total wiring shall be as short as possible, and the key signal lines shall be as short as possible; High voltage, high current signal and low current, low voltage weak signal are completely separated; Separate analog signal from digital signal; High frequency signal is separated from low frequency signal; The spacing of high-frequency components shall be sufficient.
9. The layout of the decoupling capacitor should be as close to the power supply pin of the IC as possible, and the loop formed between it and the power supply and the ground should be the shortest.
10. In the element layout, it shall be properly considered that the components using the same power supply shall be placed together as far as possible to facilitate the separation of power supply in the future.
2、 Wiring
(1) Routing Priorities
Priority of key signal line: key signals such as small signal, high-speed signal, clock signal and synchronization signal shall be wired preferentially
Density priority principle: start wiring from the components with the most complex connection relationship on the board. Start wiring from the area with the most dense connections on the board
Notes:
a. Provide special wiring layers for key signals such as clock signals, high-frequency signals and sensitive signals as far as possible, and ensure the minimum loop area. If necessary, manual priority wiring, shielding and increasing safety distance shall be adopted. Ensure signal quality.
b. The EMC environment between the power supply layer and the stratum is poor, and signals sensitive to interference should be avoided.
c. The network with impedance control requirements shall be wired according to the line length and width requirements as far as possible.
(2) Four specific routing methods
1. Clock wiring:
Clock line is one of the most influential factors to EMC. Punch less through holes on the clock line, try to avoid parallel wiring with other signal lines, and keep away from general signal lines to avoid interference with signal lines. At the same time, the power supply part on the board shall be avoided to prevent mutual interference between the power supply and the clock.
If there is a special clock generation chip on the board, the wiring is not allowed below it, but copper should be paved below it, and if necessary, the ground can be specially cut. For crystal oscillators with reference to many chips, wires should not be laid under these crystal oscillators, and copper should be laid for isolation.
2. Right angle routing:
Right angle routing is generally required to be avoided in PCB wiring, and it has almost become one of the standards to measure the quality of wiring. How much impact will right angle routing have on signal transmission? In principle, right angle routing will change the line width of the transmission line, resulting in impedance discontinuity. In fact, not only right angle wiring, sharp angle wiring, but also sharp angle wiring may cause impedance changes.
The influence of right angle routing on signal is mainly reflected in three aspects:
First, the corner can be equivalent to the capacitive load on the transmission line to slow down the rise time;
Second, impedance discontinuity will cause signal reflection;
The third is the EMI generated by the right angle tip.
3. Differential routing:
Refer to Altium Designer -- Difference distribution line and impedance matching
Differential signal is more and more widely used in high-speed circuit design. The most critical signal in the circuit is usually designed with differential structure Definition: Generally speaking, the driver sends two equivalent and inverse signals, and the receiver judges whether the logic state is "0" or "1" by comparing the difference between the two voltages. The pair of wires carrying differential signals is called differential wiring.
Compared with ordinary single ended signal routing, differential signal has the most obvious advantages in the following three aspects:
a. Strong anti-interference capability, because the coupling between the two differential lines is very good, when there is noise interference from the outside, it is almost coupled to the two lines at the same time, and the receiver is only concerned about the difference between the two signals, so the external common mode noise can be completely offset.
b. It can effectively suppress EMI. In the same way, since the polarities of the two signals are opposite, the electromagnetic fields radiated by them can cancel each other. The tighter the coupling, the less electromagnetic energy released to the outside world.
c. The timing positioning is accurate. Because the switch change of differential signal is located at the intersection of two signals, unlike ordinary single ended signals, which are judged by high and low threshold voltages, it is less affected by process and temperature, which can reduce the timing error, and is more suitable for circuits with low amplitude signals. The current popular LVDS (low voltage differential signaling) refers to this small amplitude differential signal technology.
For PCB engineers, the most important thing is to ensure that these advantages of differential routing can be fully utilized in actual routing. Maybe anyone who has been in contact with Layout will understand the general requirements of differential routing, that is, "equal length, equal distance".
Equal length is to ensure that two differential signals maintain opposite polarity at all times and reduce common mode components; Isometric is mainly used to ensure the consistency of differential impedance and reduce reflection. The principle of "as close as possible" is sometimes one of the requirements of differential routing.
4. Serpentine:
Serpentine is a kind of routing method often used in Layout. Its main purpose is to adjust the delay and meet the requirements of system timing design. Designers should first understand that the serpentine wire will damage the signal quality and change the transmission delay. It should be avoided when wiring. But in actual design, in order to ensure that the signal has enough holding time, or reduce the time offset between the same group of signals, it is often necessary to deliberately wind the wire.
Notes:
The differential signal lines in pairs are generally laid in parallel with as few holes as possible. When holes must be drilled, the two lines shall be drilled together to achieve impedance matching.
A group of buses with the same attribute should be routed side by side as far as possible to achieve equal length. The via from the patch pad shall be as far away from the pad as possible.
(3) Common rules for routing
1. Direction control rules of routing:
That is, the routing direction of adjacent layers is orthogonal. Avoid running different signal lines in the same direction at adjacent layers to reduce unnecessary inter layer interference; When it is difficult to avoid this situation due to the restriction of board structure (such as some backplanes), especially when the signal rate is high, it is necessary to consider to use the ground plane to isolate each wiring layer and the ground signal line to isolate each signal line.
2. Open loop inspection rules for wiring:
In general, dangling lines with one end floating in the air are not allowed, mainly to avoid "antenna effect" and reduce unnecessary interference radiation and reception, otherwise unpredictable results may be caused.
3. Impedance matching check rules:
The wiring width of the same network shall be consistent. The change of the line width will cause the nonuniform characteristic impedance of the line. When the transmission speed is high, reflection will occur. This situation should be avoided as far as possible in the design. Under some conditions, such as connector outlet and BGA encapsulated outlet with similar structure, it may be impossible to avoid the change of line width. The effective length of the inconsistent part in the middle should be minimized.
4. Routing length control rules:
That is, the short line rule. In the design, the wiring length should be as short as possible to reduce the interference problem caused by too long wiring. In particular, some important signal lines, such as clock lines, must be placed close to the device. For driving multiple devices, the network topology should be determined according to the specific situation.
5. Chamfer rules:
In PCB design, sharp corners and right angles should be avoided to generate unnecessary radiation and poor process performance.
6. Decoupling rules of components:
A. The necessary decoupling capacitor is added to the printed board to filter the interference signal on the power supply and stabilize the power supply signal. In multilayer boards, the position of decoupling capacitor is generally not required to be high, but for double-layer boards, the layout of decoupling capacitor and the wiring mode of power supply will directly affect the stability of the whole system, sometimes even the success or failure of the design.
B. In double-layer board design, the current should be filtered by filter capacitor before being used by devices.
C. In the design of high-speed circuit, the stability of the whole board is related to the correct use of decoupling capacitor.
7. Device layout zoning/layering rules:
A. It is mainly to prevent mutual interference between modules with different operating frequencies, and to shorten the wiring length of high-frequency part as much as possible.
B. For hybrid circuits, analog and digital circuits are also arranged on both sides of the printed circuit board, with different layer wiring and layer isolation in the middle.
8. Ground wire loop rules:
The minimum rule of the loop is that the loop area formed by the signal line and its loop should be as small as possible. The smaller the loop area is, the less external radiation is, and the less external interference is received.
9. Integrity rules of power and ground layers:
For areas with dense through holes, pay attention to avoid the interconnection of holes in the hollowed out areas of the power supply and the formation, which forms the division of the plane layer, thus damaging the integrity of the plane layer, and thus causing the increase of the circuit area of the signal line in the formation.
10. 3W rule:
In order to reduce the crosstalk between lines, ensure that the line spacing is large enough. When the line center spacing is not less than 3 times the line width, 70% of the electric fields can be kept from interfering with each other, which is called the 3W rule. If 98% electric fields do not interfere with each other, 10W spacing can be used.
11. Shielding protection:
The corresponding ground wire loop rules are actually designed to minimize the loop area of signals, which are often found in some important signals, such as clock signals and synchronous signals; For some signals of special importance and high frequency, the copper shaft cable shielding structure design should be considered, that is, the wires laid on the line, below the line, left and right should be separated by ground wires, and how to effectively combine the shielding ground with the actual ground plane should also be considered.
12. Network rules for routing termination:
In high-speed digital circuits, when the delay time of PCB wiring is greater than 1/4 of the signal rise time (or fall time), the wiring can be regarded as a transmission line. In order to ensure that the input and output impedance of the signal are correctly matched with the impedance of the transmission line, various matching methods can be used. The selected matching method is related to the connection mode of the network and the topology of the wiring.
A. For point-to-point (one output corresponds to one input) connection, you can choose to start in series matching or end in parallel matching. The former has simple structure, low cost and large delay. The latter has good matching effect, but its structure is complex and its cost is high.
B. For point to multipoint connection (one output corresponds to multiple outputs), when the topology of the network is daisy chain, terminal parallel matching should be selected. When the network is a star structure, you can refer to the point-to-point structure. Star and chrysanthemum chain are two basic topological structures. Other structures can be seen as the deformation of the basic structure, and some flexible measures can be taken to match. In actual operation, cost, power consumption, performance and other factors should be taken into account. Generally, perfect matching is not pursued, as long as the reflection and other interference caused by mismatch are limited to an acceptable range.
13. Wiring closed-loop inspection rules:
Prevent signal lines from forming self loops between different layers. This kind of problem is easy to occur in the design of multilayer plates, and self loop will cause radiation interference.
14. Control rules for branch length of routing:
Try to control the length of branches. The general requirement is Tdelay<=Trise/20.
15. Resonance rules of wiring:
Mainly for high-frequency signal design, that is, the wiring length shall not be an integral multiple of its wavelength to avoid resonance.
16. Control rules for isolated copper area:
The appearance of isolated copper area will bring some unpredictable problems. Therefore, connecting the isolated copper area with other signals is helpful to improve the signal quality. Usually, the isolated copper area is grounded or deleted. In the actual production, PCB manufacturers added some copper foils to the vacant parts of some boards, which is mainly for the convenience of PCB processing, and also plays a certain role in preventing PCB warping.
17. Rules for overlapping power and ground layers:
Different power supply layers should avoid overlapping in space. It is mainly to reduce the interference between different power sources, especially between some power sources with large voltage difference. The overlapping problem of power plane must be avoided. If it is difficult to avoid, the interlayer can be considered.
18. Rule 20H:
Because the electric field between the power layer and the stratum is variable, electromagnetic interference will be radiated at the edge of the board. It is called edge effect.
The solution is to shrink the power layer so that the electric field is only conducted within the range of the ground plane. In the unit of one H (the thickness of the medium between the power supply and the ground), if it is reduced by 20H, 70% of the electric field can be limited to the edge of the ground plane; Shrinking 100H can limit 98% of the electric field.
(4) Other
The power lines of single and double deck boards shall be as thick and short as possible. The width requirements of power line and ground wire can be calculated according to the maximum line width of 1mm corresponding to the current of 1A, and the loop formed by power line and ground wire should be as small as possible.
PCB manufacturers, PCB designers and PCBA manufacturers explain to you how PCB manufacturers teach you how to draw beautiful PCB boards.