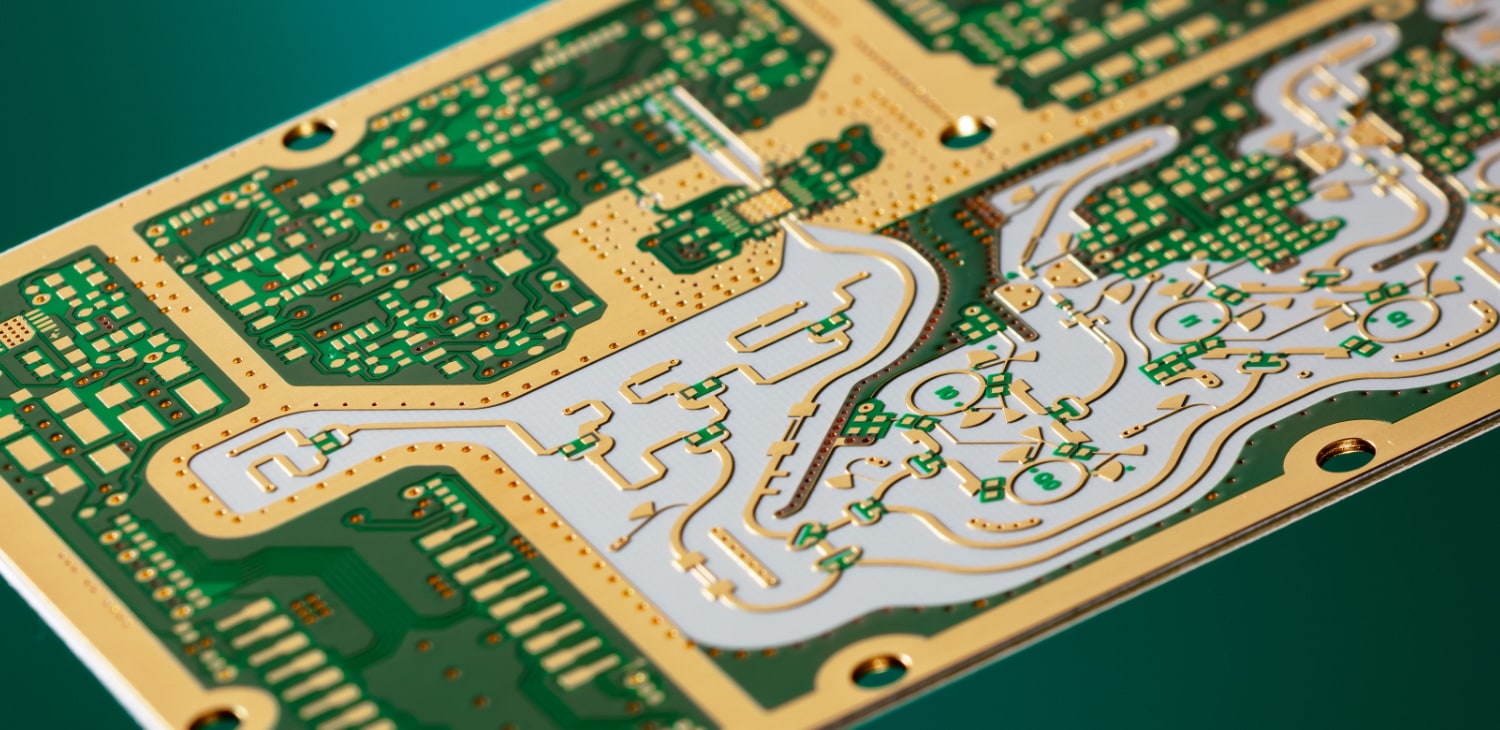
Characteristics and types of hybrid integrated circuits
A hybrid integrated circuit is an integrated circuit made by combining a semiconductor integration process with a thin (thick) film process. Hybrid integrated circuits are made by forming thick or thin film components and their interconnections on a substrate, then mixing discrete semiconductor chips, monolithic integrated circuits or micro components on the same substrate, followed by external packaging. Compared with discrete component circuits, hybrid integrated circuits have the characteristics of high assembly density, high reliability and good electrical performance. Compared with monolithic integrated circuits, hybrid integrated circuits have flexible design, convenient process, easy multi-variety and small-batch production, and have a wide range of component parameters, high precision, good stability, and can withstand higher voltage and higher power. Hybrid integrated circuits are mainly used in analog integrated circuits, microwave integrated circuits and optoelectronic integrated circuits. They are also used in special circuits with higher voltages and higher currents. The application of hybrid integrated circuits in the microwave field is particularly prominent.
1. Features
Hybrid integrated circuits concentrate the functional components of all components in the circuit on the substrate, which can basically eliminate auxiliary components in electronic components and assembly gaps and solder joints between components, thereby improving the assembly density and reliability of electronic equipment. Due to this structural feature, hybrid integrated circuits can be used as distributed parametric networks with electrical properties that are difficult to achieve with discrete component networks. Another feature of hybrid integrated circuits is to change the sequence, thickness, area, shape and characteristics of the three-layer films of conductors, semiconductors and dielectrics, as well as their lead positions, to obtain passive networks with different properties.
2. Type
There are two film-forming techniques used in the manufacture of hybrid integrated circuits: screen printing and sintering and vacuum film-forming. The film made by the former technique is called thick film, and its thickness is usually more than 15 microns, while the film made by the latter technique is called thin film, and its thickness is between several hundred angstroms to several thousand angstroms. If the passive network of the hybrid integrated circuit is a thick film network, it is called a thick film hybrid integrated circuit. If it is a thin film network, it is called a thin film hybrid integrated circuit. In order to meet the miniaturization and integration requirements of microwave circuits, microwave hybrid integrated circuits exist. According to the concentration and distribution of the composition parameters, the circuit is divided into a concentrated parameter and a distributed parameter microwave hybrid integrated circuit. The structure of the lumped parameter circuit is the same as that of a conventional thick-film hybrid integrated circuit, except that the component size accuracy is higher. Distributed parametric circuits are different. Instead of visually distinguishable electronic components, its passive network consists entirely of microstrip lines. The dimensional accuracy of microstrip lines is high, so thin film technology is mainly used to manufacture distributed parameter microwave hybrid integrated circuits.
Another difficulty in modern mixed-signal PCB design is that there are more and more devices with different digital logic, such as GTL, LVTTL, LVCMOS and LVDS logic. The logic threshold and voltage swing of each logic circuit are different. However, these different logic thresholds The circuit with voltage swing must be co-designed on one PCB. Here, you'll learn strategies and techniques for success through a thorough analysis of layout and routing designs for high-density, high-performance, mixed-signal PCBs.
Mixed Signal Circuit Layout Fundamentals
When digital and analog circuits share the same components on the same board, the layout and routing of the circuits must be methodical.
In mixed-signal PCB design, there are special requirements for power traces and the isolation of analog noise and digital circuit noise to avoid noise coupling, which increases the complexity of layout and routing. The special demands on power transmission lines and the requirement to isolate noise coupling between analog and digital circuits add further complexity to the layout and routing of mixed-signal PCBs.
If the power supply of the analog amplifier in the A/D converter and the digital power supply of the A/D converter are connected together, it is likely to cause mutual influence between the analog part and the digital part circuit. Perhaps, because of the location of the I/O connectors, the layout scheme must mix the routing of digital and analog circuits.
Before placing and routing, engineers need to understand the fundamental weaknesses of the placement and routing scheme. Even with false positives, most engineers tend to use placement and routing information to identify potential electrical effects.
Layout and routing of modern mixed-signal PCBs
The following will illustrate the technology of mixed signal P CB layoutand wiring through the design of OC48 interface card. OC48 stands for Optical Carrier Standard 48, basically oriented to 2.5Gb serial optical communication, which is a kind of high-capacity optical communication standard in modern communication equipment. The OC48 interface card includes several typical mixed-signal PCB layout and routing issues, and its layout and routing process will indicate the order and steps to solve the mixed-signal PCB layout scheme.
The OC48 card contains an optical transceiver that realizes bidirectional conversion of optical signals and analog electrical signals. Analog signal input or output digital signal processor, DSP converts these analog signals into digital logic level, which can be connected with microprocessor, programmable gate array and system interface circuit of DSP and microprocessor on OC48 card . A separate phase-locked loop, mains filter and local voltage reference are also integrated.
Among them, the microprocessor is a multi-power supply device, the main power supply is 2V, and the I/O signal power supply of 3.3V is shared by other digital devices on the board. Independent digital clock sources provide clocks for OC48I/O, microprocessor and system I/O.
After checking the layout and wiring requirements of different functional circuit blocks, it is initially recommended to use a 12-layer board, as shown in Figure 3. Microstrip and stripline layer configurations safely reduce coupling to adjacent trace layers and improve impedance control. A ground plane between the first and second layers will isolate the sensitive analog reference source, CPU core, and PLL filter power routing from the microprocessor and DSP devices on the first layer. The power and ground planes always come in pairs, as is done on the OC48 card for the shared 3.3V power plane. This will lower the impedance between the power supply and ground, thereby reducing noise on the power supply signal.
It is necessary to avoid running digital clock lines and high-frequency analog signal lines near the power plane, otherwise, the noise of the power signal will be coupled into the sensitive analog signal.
Carefully consider utilizing power and analog ground plane splits, especially at the input and output of mixed-signal devices, according to digital signal routing needs. Routing through an opening on an adjacent signal layer can cause impedance discontinuities and poor transmission line loops. These can cause signal quality, timing and EMI problems.
Sometimes adding several ground planes, or using several peripheral layers under a device for the local power plane or ground plane, can eliminate openings and avoid the above problems. Multiple ground planes are used on the OC48 interface card. Maintaining the lamination symmetry of the position of the opening layer and the wiring layer can avoid deformation of the card and simplify the manufacturing process. Due to the strong ability of 1 ounce copper clad laminate to withstand large currents, 1 ounce copper clad laminate should be used for the 3.3V power supply layer and the corresponding ground layer, and 0.5 ounce copper clad laminate can be used for other layers. In this way, the transient high current or peak period can be reduced. Voltage fluctuations.
If you are designing a complex system from the ground plane up, use 0.093-inch and 0.100-inch thick cards to support the wiring and ground isolation planes. The card thickness must also be scaled to the routing feature dimensions of the via pads and holes so that the aspect ratio of the drilled hole diameter to the thickness of the finished card does not exceed the aspect ratio of the metallized holes provided by the manufacturer.
If you want to design a low-cost, high-volume commercial product with a minimum number of routing layers, carefully consider the routing details of all special power supplies on the mixed-signal PCB before placing or routing. Have the target manufacturer review the preliminary layering scheme before starting place and route. Layering is basically based on finished product thickness, number of layers, copper weight, impedance (with tolerance) and minimum via pad and hole size, and the manufacturer should provide layering recommendations in writing.