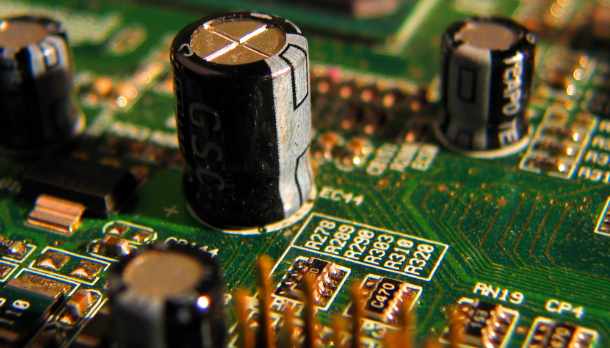
Transfer the printed PCB bottom drawing to the copper coating plate with a heat transfer machine
Repair board:
Patch up a few unprinted lines with quick-drying paint
5. Corrosion: Put the copper coated plate printed with the circuit board diagram into the ferric chloride solution for corrosion. If the solution concentration is high and the temperature is high, the corrosion rate is fast, but the concentration and temperature should be appropriate. Corrosion time to master.
6. Wash and dry
Step 7 Drill a hole
Select the right diameter drill bit: integrated circuit pin and general resistance and capacitance with 0.8mm diameter drill bit, if any component pin is thick, according to the measured value, can be changed into a larger diameter drill bit. During the drilling process, the drill should be inserted as deep as possible into the fixture, and the fixture should be tightened.
8. Remove the ink on the copper film
Use organic solvents (alcohol, banana water, acetone, etc.) to erase the ink covering the copper film line, or use sandpaper to erase it if no such solvents are available.
9. Sand and check the circuit board
After removing the ink, polish the copper film line with finer sandpaper. The better the sanding, the better the welding. However, do not polish too much, so as to avoid excessive loss of copper film thickness. After sanding, clean with Kleenex.
Check the circuit board: Use a multimeter to check whether there is short circuit or open circuit between the lines on the PCB. There is a short circuit to cut, there is a break to put on the solder, connect it well.
10. Apply flux
Dissolve rosin in anhydrous alcohol to make a flux for use. Make sure the flux concentration is right. Too thick, not bright after drying, too thin, poor welding performance.
Use a brush to evenly apply the alcohol rosin flux to the cleaned PCB board. When brushing, place the PCB board vertically so that the flux does not clog the drill hole. Brush once, too many times easy to wrinkle, not bright.
Place PCBS coated with alcohol rosin flux in the sun to cool dry or natural cool dry. ICL7107 is a decimal double integral 3-bit semi-ADC with an accuracy of ±2LSB(the least significant bit). When its typical reference voltage is 100.0 mV and 1000 mV, and the corresponding integral resistance and capacitance of the peripheral circuit are selected, it can form two kinds of circuits with full range of 200 mV and 2000 mV.
The relationship between the output display number N, input voltage and reference voltage VREF of ICL7107 is as follows:
N = 1000×
In the formula, N is only the output display numeric value, and its decimal point position needs to be set separately. Obviously, when the reference voltage VREF is less than its typical reference voltage (100.0 mV and 1000 mV), the output display digit N will be enlarged; When the reference voltage VREF is larger than its typical reference voltage (100.0 mV and 1 000 mV), the output display digit N will be reduced.
4 Analysis of the working principles of ICL7107 chips
ICL7107 integrated circuit has two parts: analog and digital circuits. The analog circuit is composed of a transfer switch and an operational amplifier to realize signal sampling and integration. It uses differential input with an input impedance of 1O10Ω. The digital circuit consists of counter, latch, control logic and display decoder. The voltage value of the input analog signal is first converted into a time width signal proportional to it, and then the clock pulse of a fixed frequency is counted in this time width, the counting result is proportional to the number of the input analog signal, and finally the digital latch and decode display. The conversion cycle is divided into three stages: automatic zero stabilization (AZ) stage, signal integration (INT) stage and anti-integration (DE) stage, whose time is as follows:
(1) Automatic zero stabilization stage (AZ)
TAZ =1O00×TCL-(2000×TCL -1000×TCL ×lN/VREF
(2) signal integration stage (INT)
The input analog signal is integrated at a fixed time: TINT= l000×TCL
(3) Inverse integral (DE) stage
This stage is to integrate the reference voltage VREF whose polarity is opposite to the input signal. The maximum time of reverse phase integration is T(DE)MAX =2000×TCL
The time from the beginning of the inverse integration until the integrator output returns to the analog common terminal (C00M0N) voltage VCOM is proportional to the magnitude of the input analog voltage, whose digital reading is:
N = 1000×
In the reverse integration period, the maximum number of input clock pulses is 2000, and when it is equal to or exceeds 2000, it overflows. When it is less than 2000, as long as the reverse integration period ends, it will enter the automatic zero stabilization period. To sum up, the three phases of A/D conversion require a total of 4000 TCL clock cycles, because the oscillation period is 4 frequency divided TCL, so the whole conversion time is 16,000 Tosc(oscillation period).
5 Assembly and debugging of components
5.1 Adopt the test method
The TEST end of pin 37 is shorted with pin l, and the watch head should display -188.8. Check the display for missing strokes. If there is, most of the pin, wire weld.
First, short connect IN+ with IN- and the header should appear as "0000". If not zero, check the reference source capacitor C2 and the automatic zeroing capacitor C4 for leakage.
Short connect pin 3l to pin 36, head reading should be 1000. If there is a deviation, potentiometer RP. Still not, mostly RP, integration capacitor C3 is bad.
Short connect pin 32 and pin 26, the highest position of the watch head should be displayed -l, other positions are not bright. Otherwise, check the power supply or change the chip.
5.2 Rectify the fault according to the fault symptom
This method is direct and fast to judge the fault. Such as: input signal is zero, the table head display is not zero, do not stop beating. Reference source capacitor C2 and autozeroing capacitor C4 should be checked.
If the meter head reading deviation is large, it may be the integration capacitor C3 problem, or the reference voltage changes.
6 Experimental Summary
a. Place the name (pinyin) in the BottomLayer and mirror horizontally. Chinese characters cannot be used
b. Check the network table: according to the Nets in the schematic diagram, check one by one under the manager Nets in the PCB to see if there are any errors.
C. CB must be DRC checked after production, no highlighting (green) display
d. When making components, the position of the package diagram is not paid attention to. Generally, No. 1 pad should be placed at the origin of coordinates. If it is far away from the origin of coordinates, it will be far away from the placement position when the PCB drawing is transferred, and it can not even be seen.
e. Know the test methods for whether ICL7107, ICL7660, MC78058T, TL431, S-DSP are normal.
f.ICL7660 can reverse voltage, ICL7107 can convert D/A and decode, LM35 can convert temperature signals into electrical signals, and MC7805T can provide +5V voltage.