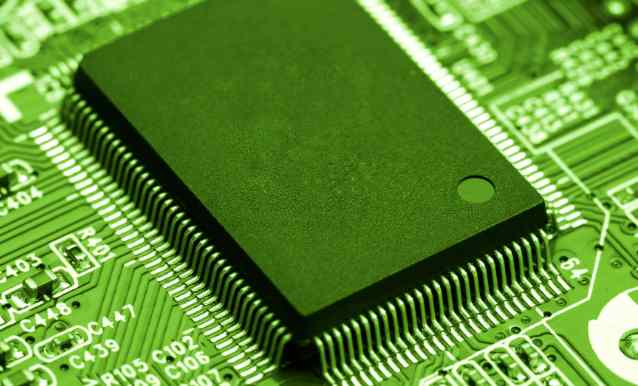
Experimental modal analysis is the synthesis of several engineering disciplines. It obtains the modal parameters of the system, such as natural frequency, mode shape and modal damping, through four steps: establishment of the test "device", estimation of frequency response function, system identification and identification result verification. Experimental modal analysis results are often used to test the validity and correctness of finite element analysis models. In order to verify the validity of the finite element analysis model and the correctness of the modal analysis results of the object PCB module, the modal analysis of the PCB module was carried out.
1. Experimental modal analysis system
The modal test system adopted in this paper is composed of vibrator, force sensor, fixture, test object, laser vibration meter (IVS200), dynamic signal analyzer (DP730), data acquisition and recording software (SignalCalc730)/ modal analysis software (ME 'Scope V4) and PC.
In order to make the boundary conditions of the object PCB component in the experimental modal analysis consistent with those in the finite element modal analysis, the object PCB component was fixed on the fixture plate through four 15mm high riveting nut columns with screws. The details are shown in Figure 7. In the experiment process, sinusoidal sweep frequency is used to excite test objects, and the response of PCB components is stimulated by laser vibration meter. Dynamic signal analyzer and data processing software are used to calculate the frequency response function (FRF) of each point on PCB components. Finally, modal analysis software is used to identify the modal parameters of the system.
2. Experimental modal analysis results
Several points with equal distance on PCB components were selected, and the frequency response function (FRF) of each point was obtained by point-by-point scanning, and then the modal parameters of PCB components were identified.
3. Results comparison and discussion
In order to verify the consistency of the finite element modal analysis results with the experimental modal analysis results, and then judge the correctness of the established finite element model of object PCB components and the degree of correlation with the experimental model, it is necessary to compare the finite element modal analysis results with the experimental modal analysis results, as shown in Table 4. The comparison between the results of finite element modal analysis and experimental modal analysis requires two steps: first, the natural frequency values of the two are compared, and then the degree of modal correlation (MAC) of the two is compared. Comparison of natural frequencies is the most common step, but if the results of experimental modal analysis and finite element modal analysis do not correspond in strict order, there is a risk of error in the comparison of natural frequencies alone. This is because two identical frequency values in the system may correspond to two distinct modes. Therefore, the correlation degree between the finite element analysis model and the experimental model can be accurately judged only when the above two steps are carried out simultaneously.
The results of finite element modal analysis are in good agreement with those of experimental modal analysis. Compared with the experimental results, the error of natural frequency obtained by finite element modal analysis is less than 7%, and the correlation between the two modes is greater than 0.75. Moreover, the mode shapes obtained by experiment correspond to those obtained by modal analysis in order.
4 Summary
In this paper, the PCB component of avionics equipment is taken as the research object. Firstly, the finite element analysis model is established, and the first 3 order natural frequencies and modes are calculated by using the Lanthos block method. Then, in order to verify the correctness of the calculation results and determine the degree of correlation between the finite element model and the actual PCB components, the experimental modal analysis system is used to carry out the experimental modal analysis of the object PCB components. Finally, the comparison between the calculated results and the experimental results shows that the finite element modal analysis results are in good agreement with the experimental modal analysis results. The dynamic characteristic data of object PCB components obtained in the paper are correct and reliable. The finite element model can be used for the subsequent dynamic response analysis work.
The key of PCB data exchange technology
The design-based PCB data exchange scheme and standardization process must focus on solving the following key technical problems in order to achieve success: (1) Seeking a sound single data structure of PCB; The PCB output exchanger of EDA tool is developed; (3) CAM software and PCB input exchanger of manufacturing equipment are developed so that the design data can be converted into the control data of driving equipment smoothly; (4) The full range of recognition of PCB design and manufacturing manufacturers.
Research and prospect of PCB data exchange
In recent years, the most influential design/manufacturing data Exchange research project in PCB manufacturing industry is Electronic CAD/CAM Exchange, ECCE) and the Data Exchange Convergence Project (DECP), where the ECCE project has been completed and DECP is underway. The ECCE project is promoted by two standardization bodies: IPC, which sets the format and parameter standards, and EIA, which sets the information model. The research involves design/manufacture interconnect (extended application of EDIF 400) and preparation of CAM format standard (IPC-2510 series). The final result of the implementation of the project was to enable IPC to publish a more complete GenCAM data exchange standard.