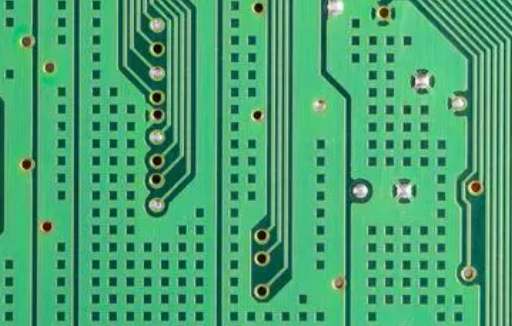
Today I would like to popularize the production process of smt laser steel mesh with you. For some friends who do not know how to make SMT steel mesh, this is a blessing:
(1) Making the net frame Below is a made good net frame. In the middle is a breathable mesh, four sides are aluminum alloy smt steel mesh frame. The mesh frame is used to hold the steel sheet in place. Steel mesh frame smt laser steel mesh production process
(2) The so-called sealing net, is to put the steel sheet, on the top of the net frame, and then affixed AB glue fixed. The frame must be able to have a good levelness; Screen is best with polyester mesh, it can maintain tension stability for a long time; The steel sheet is best used 304, and the matte will be more conducive to the solder paste (adhesive) rolling than the mirror; The adhesive must be strong enough and resistant to certain corrosion. smt laser steel mesh production process
Steel mesh cutting, is the use of steel mesh cutting machine, in the steel mesh cutting. The quality and progress of the cutting machine, position accuracy, determine the quality of this steel mesh.
(4) grinding, QC treatment because laser cutting will produce metal slag attached to the wall and the opening, so generally to surface grinding; Of course, grinding is not only to remove slag (burr), it is also to coarsening the surface of the steel sheet, increasing the surface friction, to roll the solder paste, to achieve good tin effect. If necessary, "electric polishing" can also be selected to completely remove slag (burr) to improve the hole wall. Clean up first. After laser cutting the steel mesh, there are a lot of debris. The D is removed first and then the sanding is done. Take a shot of a polished gadget). In fact, is to use sandpaper, on top of the grinding, very simple! SMT laser steel mesh production process and product quotation.
(5) Package and deliver.
Take out the delivery, because, steel mesh is easily damaged goods. It is easily damaged in transit. As we all know, domestic express companies, when dividing parcels, use the foot, throw hard, very common.
If not packaged, the customer received, is the waste. Specially mention the packaging of smt laser steel mesh of Jialichuang: After putting the finished SMT steel mesh into the packaging box, we specially add a very hard but very light board on the outside of the outer packaging box. Even if it is trampled, it can ensure that the steel mesh is not deformed, not damaged, convenient for smt steel mesh processing and use, no problem. After packaging, wait for the Courier company to pick up the goods.
How to save the cost of wave soldering in PCB circuit board
The following four process technologies form several aspects that are economically closely combined, thus saving the cost of wave soldering:
1. Recovery and regeneration of solder. The use of solder recycling system can maximize the cost savings. During welding operations, up to 75% of the solder (depending on the pump design) oxidizes into scum, which is primarily pure solder.
2. Control of lead-free process. In fact, preheating is more stringent in lead-free applications because it requires higher temperatures: some lead-free solders have melting temperatures approaching 700℉.
3. Type of preheater. Wave soldering equipment manufacturers use different types of heating methods: quartz lamps, infrared (IR) tubes, and Calrod ceramic components, all operating at high temperatures (1,300 to 2,000 ℉) so that the top surface of the PCB reaches an optimal temperature of 190 to 240℉ before entering the wave crest. The use of such a high heat source to try to achieve a relatively low temperature on the PCB surface greatly increases the possibility of flux overburning.
4. Design of preheater. Most wave welders are equipped with preheaters of different configurations. However, the best design for preheating systems should include more than one type of heater, for example, a system with a combination of a blackbody IR heating plate on the bottom and a strong air convection heater on the top.