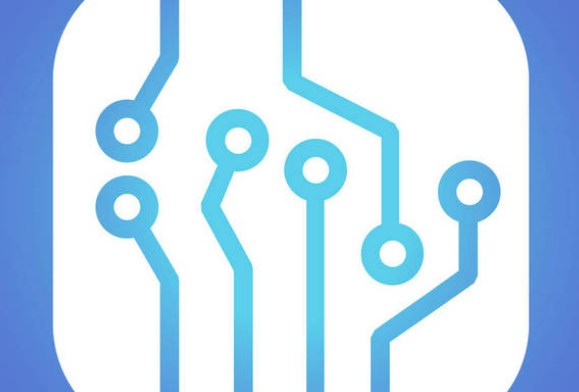
1. Problem: the width of all wires of the black and white film after turning becomes thin and uneven
Reasons:
(1) Improper selection of exposure process parameters
(2) The quality of the original film is poor
(3) There is a problem with silicon control in the turning process
Solution:
(1) First check whether the positive or negative positive is overexposed and should be corrected according to the actual situation.
(2) Check the optical density of the original film, especially whether the "shading density" is too low.
(3) Check the developer concentration and device.
2. Problem: the width of the wire on the outer edge of the film after turning becomes thin or irregular
Reasons:
(1) The verification of the exposure device is expired
(2) The light source is too close to the larger film
(3) The distance and Angle of the reflector of the light source are misaligned
Solution:
(1) Check again according to the process requirements to check whether the energy of the light source is within the technical requirements
(2) readjust the distance of the light source or use a large exposure machine
(3) readjust the distance and Angle of the "reflection mask"
3. Problems: the resolution of the turned film is not ideal, and the edge of the wire is not sharp
Reasons:
(1) The quality of the original film is not good
(2) The function of the vacuum system of the exposure machine is poor
Solution:
(1) Check the wire edge status of the original film
(2)A: It is especially necessary to check whether the sealing part and the sealing part of the film are sealed
B: In case of insufficient pumping, check whether the pumping hose is damaged
4, the problem: the local resolution of the film after turning is poor
Reasons:
(1) The quality of the original film is not good
(2) The function of the vacuum system of the exposure machine is poor
(3) There are bubbles between the negatives during exposure
Solution:
(1) Check the bad condition of the wire edge of the original film
(2)A: Check the sealing part of the vacuum system and the sealing part of the negatives
B: Check whether there are damaged parts in the air hose
(3) There are ash particles on the surface of the exposure machine, so the pumping system must be strengthened.
5. Problem: insufficient optical density of the film after turning (mainly refers to the insufficient shading degree of the dark area)
Reasons:
(1) The development process of the turned negative is incorrect
(2) Poor storage conditions of original negatives
(3) The function of developing equipment deteriorates
Solution:
(1) Check the developing process conditions and developer concentration
(2) need to be stored in the room that meets the process requirements, especially to avoid the light.
(3) Inspection and repair, especially the temperature and time control system
6. Problem: pinholes or holes appear on the graphic surface of the film after turning
Reasons:
(1) There is dust or particles on the surface of the exposure machine
(2) Poor quality of original film
(3) The substrate quality of the original film is poor
Solution:
(1) The original film and exposure table should be carefully cleaned.
(2) Check the graphic surface state of the original negative. If necessary, you can try to turn over the second negative for comparative inspection
(3) Experimental inspection is carried out to observe whether there are pinholes or holes in the black surface of the dark area after the whole piece is exposed and developed.
7, the problem: after turning the negative circuit graphic deformation
Reasons:
(1) The temperature and humidity of the working environment are incorrect
(2) Incorrect drying process
(3) The pre-processing of the negatives to be turned is not appropriate
Solution:
(1) Operation of ambient temperature and humidity control: temperature 20-27℃, humidity 40-70%RH, high precision film, its operating humidity should be controlled at 55-60%RH.
(2) Place the film horizontally and blow dry, and dry the film with thickness (100um) for 1-2 hours; Dry the 175-micron substrate for 6-8 hours.
(3) It should be placed in the environment of the film room for at least 24 hours for stability treatment
8. Problem: insufficient transparent area of negative or cloudy substrate
Reasons:
(1) There are inclusions in the original negative substrate
(2) The original substrate surface is poor
(3) The quality of the original film is poor
(4) There are problems in the exposure and development process
Solution:
(1) The original film with high resolution and high quality is selected
(2) Ensure that the temperature and humidity of the storage environment are controlled
(3) First of all, the performance and quality of the original film should be tested
(4) Check and adjust the equipment condition, developer solution, fixer solution and process conditions.
The cost calculation of PCB industry is the most special and complex in all industries. From opening material, pressing plate, forming, to FQC, packaging, completion and storage, it is necessary to input the material cost, labor cost and manufacturing cost of each process
Step by step accounting, and then according to the order product number batch cumulative cost. And different types of products, the process of the standard rate will be different. For some products such as blind hole plate, gold plate and copper plate, some special calculation methods must be adopted because of the particularity of the process or all materials. Similarly, the size of drill nozzle used in the drilling process will also affect the cost of the product, which directly affects the calculation and evaluation of WIP cost and scrap cost