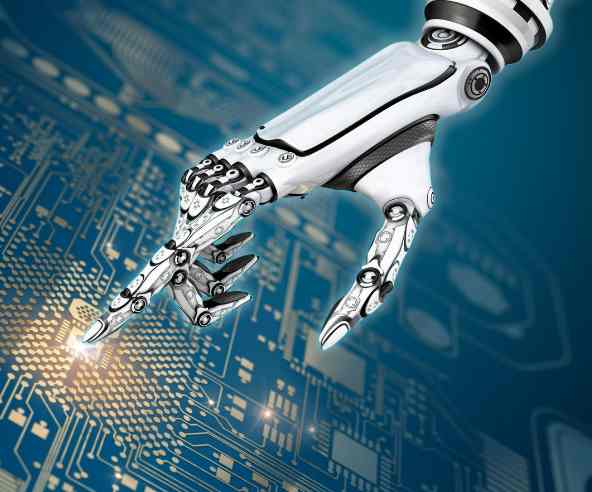
Pad is the most common contact in PCB design is also the most important concept, but beginners are easy to ignore its selection and correction, in the design of the same use of circular pad. The shape, size, arrangement form, vibration and heat condition, force direction and other factors should be considered comprehensively in selecting the type of pad of the element. Protel provides a series of pads with different sizes and shapes in the packaging library, such as round, square, octagonal, round square and positioning pads, but sometimes this is not enough, and you need to edit yourself. For example, the welding pad with large heat and force and large current can be designed into a "teardrop shape". In the design of the line output transformer pin pad of color TV PCB that we are familiar with, many manufacturers use this form. In general, in addition to the above, the following principles should be considered when editing the pad:
(1) When the length of the shape is inconsistent, the size difference between the wire width and the specific side length of the pad should not be too large;
(2) The length of asymmetrical pad is often used to get twice the result with half the effort when the wiring between the leading angles of components is needed;
(3) The size of the welding pad hole of each component should be edited according to the pin thickness of the component respectively. The principle is that the size of the hole is 0.2-0.4mm larger than the pin diameter.
Various types of membrane (Mask)
These membranes are not only essential in PcB manufacturing process, but also necessary for component welding. According to the position and function of the "film", the "film" can be divided into two categories: component surface (or welding surface) welding aid film (TOp or Bottom and component surface (or welding surface) welding resistance film (TOp or BottomPaste Mask). As the name suggests, the welding film is coated on the welding pad, improve the welding performance of a layer of film, that is, on the green board than the pad slightly larger each light colored round spot. Solder resistance film is on the contrary, in order to make the board to adapt to wave soldering and other forms of welding, the copper foil on the non-plate plate can not stick to tin, so in the various parts of the plate are coated with a layer of paint, used to prevent these parts on tin. It can be seen that the two membranes are complementary. From this discussion, it is not difficult to determine the Settings of items like solder Mask En1argement in the menu.
Flying line, flying line has two meanings:
Network connections similar to rubber bands are used for observation during automatic wiring. After components are called in through the network table and preliminary layout is made, the "Show" command can be used to see the crossover status of network connections under this layout. The positions of components are constantly adjusted to minimize such crossover, so as to obtain the maximum spread rate of automatic wiring. This step is very important, it can be said that sharpening the knife is not wrong to cut wood work, spend some time, value! In addition, the end of automatic wiring, and what network has not been distributed through the function to find. Find out the network is not spread, available manual compensation, compensation is not to use the second layer of "flying line" meaning, is in the future printing board with wire connected to these networks. It is to be explained that if the circuit board is a mass automatic line production, the flying line can be regarded as a 0 oh-resistance value, with a unified pad spacing resistance components to design.
2. PCB design principle of physical partition and electrical partition
Design partitions can be broken down into physical and electrical partitions. Physical partitioning involves component layout, direction, and shielding. Electrical partitions can continue to be broken down into partitions for power distribution, RF wiring, sensitive circuits and signals, and ground.
Physical partitioning principle
(1) Principle of location layout of components. Component layout is the key to achieving a good RF design. The most effective technique is to first secure and Orient the components located on the RF path so as to minimize the length of the RF path, keep the input away from the output, and separate the high power circuit from the low power circuit as far as possible.
(2) PCB stacking PCB design principles. The most efficient way to stack boards is to arrange the main ground (the main ground) in the second layer below the surface, and to arrange RF lines on the surface as much as possible. Minimizing the through-hole size on the RF path not only reduces the path inductance, but also reduces virtual solder spots on the main site and reduces the chance of RF energy leaking into other areas within the laminates.