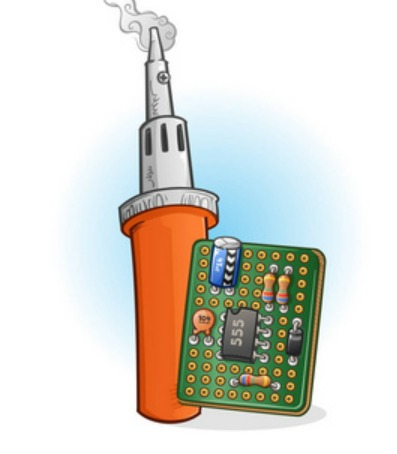
Some basic requirements of PCB board pad design
Pad type
On the printed circuit board, the electrical connection of all components is carried out through the pad. Pad is the most important basic unit in PCB design. According to different components and welding technology, the pad in printed circuit board can be divided into two types: non-perforated pad and perforated pad. Non-perforated pad is mainly used for the welding of surface-mounted components, while perforated pad is mainly used for the welding of pin components.
The selection of the shape of the welding pad is related to the shape, size, layout, heat condition and force direction of the components, and the designer needs to choose according to the comprehensive consideration of the situation. In most PCB design tools, the system provides designers with different types of pads, such as the Round pad, the Rectangle pad, and the Octagonal pad.
1. Circular pad
Circular pad is the most commonly used pad in printed circuit board. For the perforated pad, the main size of the circular pad is the size of the aperture and the size of the pad. There is a proportional relationship between the size of the pad and the size of the aperture, such as the size of the pad is generally twice the size of the aperture. Non-pass circular pad is mainly used for testing pad, positioning pad and reference pad, and its main size is the size of the pad.
2. Rectangular pad
Rectangular pads include square pads and rectangular pads. The square pad is mainly used to identify the first pin on the printed circuit board for mounting components. Rectangular pad is mainly used as pin pad for surface mount components. The size of the pad is related to the pin size of the corresponding component, and the pad size of different components is different. Please refer to Section 1.3 for the specific size of some component pads.
3. Octagonal pad
Octagonal pad is used in printed circuit board relatively little, it is mainly to meet the wiring of printed circuit board and the welding performance of the pad and other requirements.
4. Special-shaped pad
In the process of PCB design, the designer can also use some special shape pad according to the specific requirements of the design. For example, for some welding pads with large heat, large force and large current, it can be designed into tear drop shape.
Pad size
Pad size has a great influence on the manufacturability and life of SMT products. There are many factors affecting the size of the pad. When designing the size of the pad, we should consider the range and tolerance of the size of the components, the needs of the size of the solder joint, the accuracy, stability and process ability of the substrate (such as positioning and patch accuracy, etc.). The size of the pad is determined by the shape and size of the components, the type and quality of the substrate, the capacity of the assembly equipment, the type and capacity of the process adopted, and the required quality level or standard.
The size of the designed pad, including the size of the pad itself, the size of the solder resistance or the solder resistance layer frame, the design needs to consider the footprint of the components, the wiring under the components and the dummy pad or wiring requirements for dispensing (in the wave soldering process).
Because the specific and effective comprehensive mathematical formula can not be found in the design of pad size at present, the user must also cooperate with the calculation and test to optimize their own specifications, rather than the single use of others' specifications or calculated results. Users should set up their own design files and develop a set of size specifications suitable for their actual situation.
Users need to understand many aspects of the welding pad design, including the following parts.
① Although there are international specifications for the packaging and thermal characteristics of components, the specifications differ greatly in some aspects for different countries, different regions and different manufacturers. Therefore, it is necessary to limit the selection of components or to classify the design specification into levels.
(2) Need to have a detailed understanding of PCB substrate quality (such as size and temperature stability), materials, mimeographing process capacity and relative suppliers, need to sort out and establish their own substrate specifications.
(3) We need to understand the product manufacturing process and equipment capacity, such as the size range of substrate processing, patch accuracy, screen printing accuracy, dispensing process, etc. Understanding this aspect of the welding pad design will be of great help.