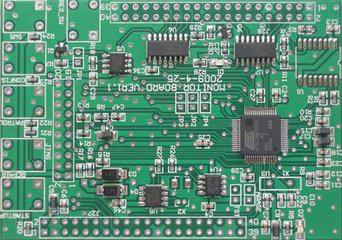
With the continuous development of science and technology, single and double panels can no longer meet the needs of part of the market, and the multilayer board has been greatly developed. The production of PCB multilayer board must go through the step of pressing. Pressing is the use of high temperature and high pressure to melt the semi-cured sheet, and make it flow, and then converted into solidified sheet. A process whereby one or more inner etched plates (blackened or browned) and copper foil are bonded together to form a single multilayer plate. The process also includes typesetting before pressing, drilling positioning holes and shape machining of multilayer plates after pressing. And in this process will encounter a lot of problems, below we will introduce the possible problems and causes.
First, uneven thickness, inner layer slip
1, the same window of the molding plate total thickness is different;
2. The cumulative thickness deviation of the printed board in the molding board is large; When the parallelism of the hot pressing template is different, the laminate can move freely, and the whole laminate is inclined to the center of the hot pressing template.
Two, the board surface has pits, resins, folds
1. Improper LAY-UP operation, the surface of the steel plate is not dry with water stains, resulting in copper foil wrinkle;
2. When pressing the plate, the surface of the plate loses pressure, resulting in excessive loss of resin, insufficient rubber under copper foil, copper foil surface wrinkle.
Three, the inner pattern shift
1, the inner pattern copper foil peeling strength is low or poor temperature resistance or line width is too fine;
2, prepressure is too high, the dynamic viscosity of resin is small;
3. Press the template not parallel.
Four, the dislocation between layers
1, the thermal expansion of the inner material, the resin flow of the adhesive sheet;
2. Thermal shrinkage when fitting;
3, the thermal expansion coefficient of laminate material and template is very different.
Five, foaming
1. Prepressure is too low;
2, the temperature is too high, the interval between prepressure and full pressure is too long;
3, the dynamic viscosity of the resin is high, the total pressure application time is late;
4, high content of volatile matter;
5, the adhesive surface is not clean;
6, poor activity or insufficient prepressure;
7, the board temperature is low.
Six, plate warping, plate warping
1. Asymmetric structure;
2. Insufficient curing cycle;
3, the direction of the bonding sheet or the inner coated copper plate is not consistent;
4, the board using different manufacturers of multilayer board or rubber board.
5, the multi-layer plate curing pressure after improper handling.
Seven, stratification, thermal stratification
1, the inner layer of high humidity or high volatile components;
2, adhesive paper volatile components are high;
3. Inner surface pollution; Foreign body contamination;
4, the surface of the oxide layer is alkaline; Chlorite residue on the surface;
5, abnormal oxidation, oxidation layer crystallization is too long; The pretreatment did not form enough surface area.
6, passivation effect is not enough.
Eight, white exposed glass cloth grain
1, resin flow is too high;
2, prepressure is too high;
3. The time to apply high pressure is not right;
4. The resin content of adhesive sheet is low, the gel time is long and the fluidity is strong.