Building 6, Zone 3, Yuekang Road,Bao'an District, Shenzhen, China
+86-13923401642Mon.-Sat.08:00-20:00
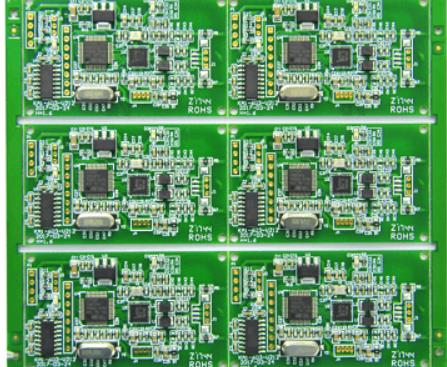
Standard specification for chip processing technology
The main equipment of smt processing production line includes solder paste printer, flat panel machine, reflow furnace, and AOI automatic optical tester When you are ready to start the SMT patch 4. production line, you must understand the SMT patch production process and select the SMT patch smt processing production line that maximizes the production capacity without wasting it
1. Template: PCB designed by smt processing determines whether to process template. If a PCB has resistors, capacitors, and repair components with more than 12.06 packages, you can use a syringe or an automatic bonding device to smear solder paste without creating a template. If the PCB contains SOT, standard operating procedures, PQFP, PLCC and BGA package chips, resistor and capacitor packages below 0805, you need to create a template. The universal template is a chemical etching copper template (low price, small batch size, 0.63.5 mm between the test and chip pin; larger than). Laser etched stainless steel sample (large batch,
2. Screen printing: (Zhichi high-precision semi-automatic solder paste printer) engrave the wiper or patch glue on the soldering board of the PCB to prepare the attached parts. This is its function The equipment used includes manual tabs (screen printer), templates and scrapers (metal or rubber), located in the SMT production line Our company suggests to use the precision semi-automatic screen printing method with the middle end and the template fixed on the screen Use the up, down, left, and right knobs of the manual tab to confirm the position of the PCB on the screen platform, and then fix this position Then, place the required coated PCB between the screen platform and the template, place the solder paste on the sieve plate at room temperature, keep the template and PCB parallel, and evenly smear the solder paste on the PCB with a scraper SMT processing and use are in progress. Clean the mold with alcohol in time to prevent the mold from being blocked by casting oil
3. Accessories: (JUKI accessories, Panasonic accessories, Siemens accessories) can accurately locate bent accessories on the fixed position of PCB. The equipment used includes batching machine (automatic, semi-automatic or manual), vacuum suction pen or tweezers (located behind the label on the SMT production line). Our company generally recommends that laboratories or small batches use double pen anti-static vacuum suction pens. To solve the deployment and deployment problem of high-precision chips (chip pin spacing is less than 0.5mm),
Because the solder paste can be directly placed where resistors and capacitors are needed, the vacuum sucker can directly select resistors, capacitors and chips from the component rack. For the chip, a suction cup can be added to the vacuum suction cup, and the size of the suction cup can be adjusted through the knob. If the position is not correctly placed (independent of the placed components), you need to clean the PCB with alcohol, reprint the PCB, and reposition the components. 4. Reflow soldering: (Heller reflow soldering, wave reflow soldering) melt the solder paste, weld the surface mounted components with PCB, achieve the electrical characteristics required by the design, accurately control according to the international standard curve, and effectively prevent the thermal damage and deformation of PCB and components. The equipment used is the reflux furnace behind the batch machine on the SMT production line (automatic infrared/hot air reflux furnace).
5. Cleaning: It has the function of removing substances that affect power efficiency or welding residues (such as welding). Use soldering that does not require cleaning, which is usually not required. Micro power products or high-frequency products need to be cleaned, and general products do not need to be cleaned. If the equipment is manually cleaned directly with ultrasonic cleaner or alcohol, the position cannot be fixed.
6. Inspection: used to verify the welding quality and assembly quality of the attached PCB. The equipment used can be equipped with magnifiers, microscopes and positions according to the inspection requirements, and the production line can be placed in an appropriate position.
7. Rework: Rework the faulty PCB, such as solder ball, welding bridge, opening and other defects The tools used are intelligent soldering iron, rework station, etc. Assign to any position in the production line
The main equipment of smt processing production line includes solder paste printer, flat panel machine, reflow furnace, and AOI automatic optical tester When you are ready to start the SMT patch 4. production line, you must understand the SMT patch production process and select the SMT patch smt processing production line that maximizes the production capacity without wasting it
1. Template: PCB designed by smt processing determines whether to process template. If a PCB has resistors, capacitors, and repair components with more than 12.06 packages, you can use a syringe or an automatic bonding device to smear solder paste without creating a template. If the PCB contains SOT, standard operating procedures, PQFP, PLCC and BGA package chips, resistor and capacitor packages below 0805, you need to create a template. The universal template is a chemical etching copper template (low price, small batch size, 0.63.5 mm between the test and chip pin; larger than). Laser etched stainless steel sample (large batch,
2. Screen printing: (Zhichi high-precision semi-automatic solder paste printer) engrave the wiper or patch glue on the soldering board of the PCB to prepare the attached parts. This is its function The equipment used includes manual tabs (screen printer), templates and scrapers (metal or rubber), located in the SMT production line Our company suggests to use the precision semi-automatic screen printing method with the middle end and the template fixed on the screen Use the up, down, left, and right knobs of the manual tab to confirm the position of the PCB on the screen platform, and then fix this position Then, place the required coated PCB between the screen platform and the template, place the solder paste on the sieve plate at room temperature, keep the template and PCB parallel, and evenly smear the solder paste on the PCB with a scraper SMT processing and use are in progress. Clean the mold with alcohol in time to prevent the mold from being blocked by casting oil
3. Accessories: (JUKI accessories, Panasonic accessories, Siemens accessories) can accurately locate bent accessories on the fixed position of PCB. The equipment used includes batching machine (automatic, semi-automatic or manual), vacuum suction pen or tweezers (located behind the label on the SMT production line). Our company generally recommends that laboratories or small batches use double pen anti-static vacuum suction pens. To solve the deployment and deployment problem of high-precision chips (chip pin spacing is less than 0.5mm),
Because the solder paste can be directly placed where resistors and capacitors are needed, the vacuum sucker can directly select resistors, capacitors and chips from the component rack. For the chip, a suction cup can be added to the vacuum suction cup, and the size of the suction cup can be adjusted through the knob. If the position is not correctly placed (independent of the placed components), you need to clean the PCB with alcohol, reprint the PCB, and reposition the components. 4. Reflow soldering: (Heller reflow soldering, wave reflow soldering) melt the solder paste, weld the surface mounted components with PCB, achieve the electrical characteristics required by the design, accurately control according to the international standard curve, and effectively prevent the thermal damage and deformation of PCB and components. The equipment used is the reflux furnace behind the batch machine on the SMT production line (automatic infrared/hot air reflux furnace).
5. Cleaning: It has the function of removing substances that affect power efficiency or welding residues (such as welding). Use soldering that does not require cleaning, which is usually not required. Micro power products or high-frequency products need to be cleaned, and general products do not need to be cleaned. If the equipment is manually cleaned directly with ultrasonic cleaner or alcohol, the position cannot be fixed.
6. Inspection: used to verify the welding quality and assembly quality of the attached PCB. The equipment used can be equipped with magnifiers, microscopes and positions according to the inspection requirements, and the production line can be placed in an appropriate position.
7. Rework: Rework the faulty PCB, such as solder ball, welding bridge, opening and other defects The tools used are intelligent soldering iron, rework station, etc. Assign to any position in the production line
Just upload Gerber files, BOM files and design files, and the KINGFORD team will provide a complete quotation within 24h.