Building 6, Zone 3, Yuekang Road,Bao'an District, Shenzhen, China
+86-13923401642Mon.-Sat.08:00-20:00
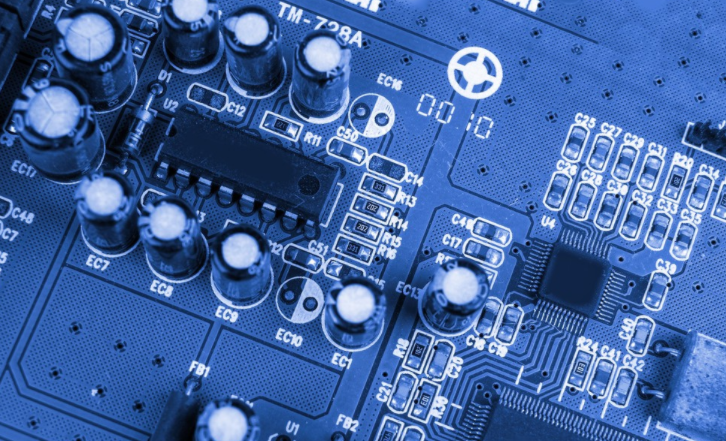
PCB short circuit and incoming line processing paster
Inspection method of circuit board short circuit in the process SMT chip processing
In the manufacturing process of SMT chip processing PCB, one of the defects prone to occur is short circuit. In order to avoid the circuit board short circuit affecting the efficiency, it is necessary to check the circuit board and solve it in time. So, how to check the short circuit of PCB? Let's look at the following.
Short circuit inspection method of PCB:
1. Use a short circuit position analyzer.
2 Open the PCB design and draw on the computer. Turn on the short circuit network and see where the nearest one is. It is easiest to connect Pay special attention to the internal short circuit of IC
3. A short circuit was found. Take a board to cut the line (especially for single-layer/double-layer boards). After the circuit is cut, each part of the function block is powered on and gradually eliminated.
4. If there is a BGA chip, because all the solder joints are covered by the chip and cannot be seen, and it is a multilayer board (more than 4 layers), it is better to use magnetic beads or 0 ohm resistance connection to separate the power supply of each chip in the design process, so that when there is a short circuit between the power supply and the ground, the magnetic bead detection is disconnected, and it is easy to find a chip. Because BGA welding is very difficult, if the machine does not weld automatically, the adjacent power supply and two grounded solder balls will be short circuited if you are not careful.
5. Be careful when welding small surface mount capacitors, especially the power filter capacitors (103 or 104), which are large in number and easily lead to short circuit between the power supply and the ground. Of course, sometimes the capacitor is short circuited due to bad luck. The best way is to test the capacitor before welding.
6. If it is manual welding, form a good habit: before welding, visually check the PCB board, and use a multimeter to check whether the key circuits (especially the power supply and grounding) are short circuited; Each time the chip is welded, use a multimeter to test to check whether the power supply and ground are short circuited; In addition, do not throw soldering iron at will.
Application of SMT Mounter in Incoming Material Processing
Surface mount technology is the key to assemble and produce surface mount products. Under normal circumstances, solder paste printing and reflow soldering can complete the printing and soldering of the entire PCB at one time, while the placement of SMC/SMD must be automatically performed by the placement machine, which usually needs to install SMDs piece by piece. In this case, the technical performance of the placement machine will directly affect the production efficiency and quality. SMT mounting machine is the core and key equipment of SMT product assembly line, which determines the automation degree of electronic product assembly technology. The advanced level of placement equipment fundamentally determines two requirements of placement process: placement accuracy and high placement rate.
What is patch handling? How does the mounter work?
SMT is to take surface mount components (such as SMC/SMD) out of their packaging structure, and then paste them on the designated pad position of PCB. This process is called "picking and placing" in English. Of course, the position of the bonding pad must be coated with solder paste, or although no solder paste is applied, the patch adhesive has been applied to the PCB surface covered by the components. After placement, the components initially adhere to the designated pad position by the adhesion of solder paste or patch adhesive.
The basic process of using the placement machine to complete the placement task is:
1. Send the PCB to the mounting machine workbench, and fix it after optical alignment;
2. The feeder sends the parts to be installed to the suction starting station of the mounter, and the mounter uses an appropriate suction nozzle to suck out the parts from its packaging structure;
3. When the patch head sends the components to the PCB, the automatic optical detection system of the placement machine cooperates with the patch head to complete the tasks of component detection and alignment correction;
4. After the placement head reaches the designated position, control the suction nozzle, accurately place the components at the designated pad position of the PCB with appropriate pressure, and use the coated solder paste and paster to bond the components;
5. Repeat steps 2-4 above until all the components to be installed are placed, the PCB sends the components on it out of the mounter, and the whole mounter is completed The next PCB can be sent to the workbench again to start a new placement job
Inspection method of circuit board short circuit in the process SMT chip processing
In the manufacturing process of SMT chip processing PCB, one of the defects prone to occur is short circuit. In order to avoid the circuit board short circuit affecting the efficiency, it is necessary to check the circuit board and solve it in time. So, how to check the short circuit of PCB? Let's look at the following.
Short circuit inspection method of PCB:
1. Use a short circuit position analyzer.
2 Open the PCB design and draw on the computer. Turn on the short circuit network and see where the nearest one is. It is easiest to connect Pay special attention to the internal short circuit of IC
3. A short circuit was found. Take a board to cut the line (especially for single-layer/double-layer boards). After the circuit is cut, each part of the function block is powered on and gradually eliminated.
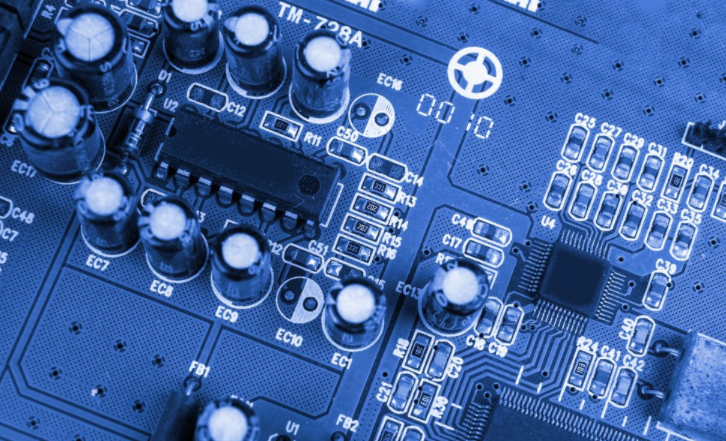
5. Be careful when welding small surface mount capacitors, especially the power filter capacitors (103 or 104), which are large in number and easily lead to short circuit between the power supply and the ground. Of course, sometimes the capacitor is short circuited due to bad luck. The best way is to test the capacitor before welding.
6. If it is manual welding, form a good habit: before welding, visually check the PCB board, and use a multimeter to check whether the key circuits (especially the power supply and grounding) are short circuited; Each time the chip is welded, use a multimeter to test to check whether the power supply and ground are short circuited; In addition, do not throw soldering iron at will.
Application of SMT Mounter in Incoming Material Processing
Surface mount technology is the key to assemble and produce surface mount products. Under normal circumstances, solder paste printing and reflow soldering can complete the printing and soldering of the entire PCB at one time, while the placement of SMC/SMD must be automatically performed by the placement machine, which usually needs to install SMDs piece by piece. In this case, the technical performance of the placement machine will directly affect the production efficiency and quality. SMT mounting machine is the core and key equipment of SMT product assembly line, which determines the automation degree of electronic product assembly technology. The advanced level of placement equipment fundamentally determines two requirements of placement process: placement accuracy and high placement rate.
What is patch handling? How does the mounter work?
SMT is to take surface mount components (such as SMC/SMD) out of their packaging structure, and then paste them on the designated pad position of PCB. This process is called "picking and placing" in English. Of course, the position of the bonding pad must be coated with solder paste, or although no solder paste is applied, the patch adhesive has been applied to the PCB surface covered by the components. After placement, the components initially adhere to the designated pad position by the adhesion of solder paste or patch adhesive.
The basic process of using the placement machine to complete the placement task is:
1. Send the PCB to the mounting machine workbench, and fix it after optical alignment;
2. The feeder sends the parts to be installed to the suction starting station of the mounter, and the mounter uses an appropriate suction nozzle to suck out the parts from its packaging structure;
3. When the patch head sends the components to the PCB, the automatic optical detection system of the placement machine cooperates with the patch head to complete the tasks of component detection and alignment correction;
4. After the placement head reaches the designated position, control the suction nozzle, accurately place the components at the designated pad position of the PCB with appropriate pressure, and use the coated solder paste and paster to bond the components;
5. Repeat steps 2-4 above until all the components to be installed are placed, the PCB sends the components on it out of the mounter, and the whole mounter is completed The next PCB can be sent to the workbench again to start a new placement job
Just upload Gerber files, BOM files and design files, and the KINGFORD team will provide a complete quotation within 24h.