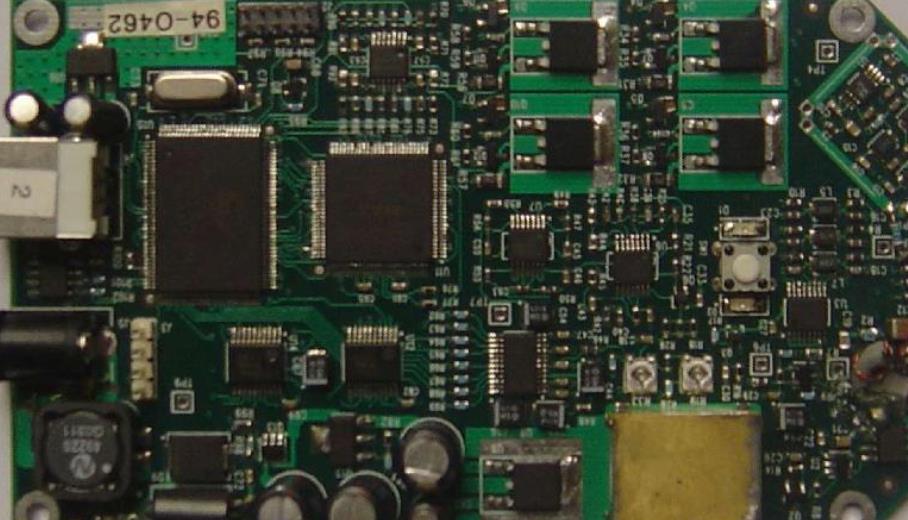
Process monitoring of PCB surface coating and SMT
Use and select PCB surface coating in SMT processing
The choice of PCB surface coating technology SMT is welded in surface mount technology. Processing mainly depends on the type of final assembly components. The surface treatment process will affect production, PCB assembly and final use
1. SMT processing technology PCB weldability surface treatment can be divided into three categories according to the use:
1. Welding: copper surface must be protected by coating (plating), otherwise it is easy to oxidize;
2. Connection: such as gold finger, nickel gold plating or nickel gold chemical plating;
3. Lead wire bonding process: electroless Ni Au plating.
2. Selection basis of PCB solderable surface coating:
When selecting PCB weldable surface coating in SMT processing, it is necessary to consider the selected welding alloy composition and product application.
1. Solder alloy composition
Circuit board
The compatibility of PCB pad coating and solder alloy is the main factor in selecting PCB solderable surface coating (electroplating). This directly affects the solderability and connection reliability of the solder joints on both sides of the pad. For example, tin lead alloy should choose tin lead hot air leveling, and lead-free alloy should choose lead-free metal or lead-free solder alloy hot air leveling.
2. Reliability requirements
For products with high reliability requirements, the same hot air leveling with solder alloy shall be selected first. This is the best choice for compatibility. In addition, high-quality Ni Au (ENIG) can also be considered, because the interface alloy Ni3Sn4 between Sn and Ni has the most stable connection strength. If ENIG is used, the nickel layer must be controlled at>3mm (5-7mm) and the gold layer – 1mm (0.05 0.15 mm), and the weldability requirements must be proposed to the manufacturer.
3. Manufacturing technology
When selecting PCB solderable surface coating (electroplating), the compatibility of PCB pad coating with manufacturing technology should also be considered. Hot air leveling (HASL) has good weldability, can be used for double side reflow welding, and can withstand multiple welding. However, due to the uneven surface of the pad, it is not suitable for narrow spacing. OSP and immersion tin (I-Sn) are more suitable for single-sided assembly and one-time welding processes.
Monitoring of chip processing
11% of SMT quality problems are caused by design, 27% by process, 31% by process data and 31% by process control. It can be seen that DFM, process optimization, process control and supply chain management (procurement and management of process data) are very important for achieving high quality.
SMT process monitoring:
Process monitoring is an important activity to ensure quality and production efficiency. Take SMT key process reflow as an example. Although the reflow soldering furnace is equipped with a temperature sensor (PT) and a furnace temperature control system to control the furnace temperature, the set temperature of the equipment is not equal to the actual temperature of the solder joints on the assembly board. Although the display temperature of the furnace is controlled within the temperature control accuracy of the equipment, it is due to the differences in the quality, layers, assembly density, number of assembly plates entering the furnace, conveying speed, air flow and other aspects., The temperature curve of the assembly plate entering the furnace will also fluctuate randomly. At present, the density of chip processing and assembly is getting higher and higher, the assembly plate is getting more and more complex, the lead-free process window is very narrow, and several degrees of temperature change may also affect the welding quality. It is necessary to continuously monitor the reflow welding process.
Process monitoring requires scientific and technical personnel to have good measurement knowledge, statistical knowledge, causal analysis ability, and in-depth understanding of equipment efficiency
Because there are many variables on the production line, equipment, personnel, data, etc. have their own variables, and these variables affect and constrain each other to varying degrees every day. How to fully and effectively monitor without affecting production and new production costs is a difficult task.
At present, software and equipment that can continuously monitor are becoming more and more popular, such as reflow process control tools, process control using AOI software technology, etc However, the automatic monitoring and response of process parameters require a large amount of investment, which is not recognized by most people in China at present In this case, we need to formulate some practical and effective norms and systems, comply with the implementation of the norms, and achieve process stability through manual monitoring and monitoring