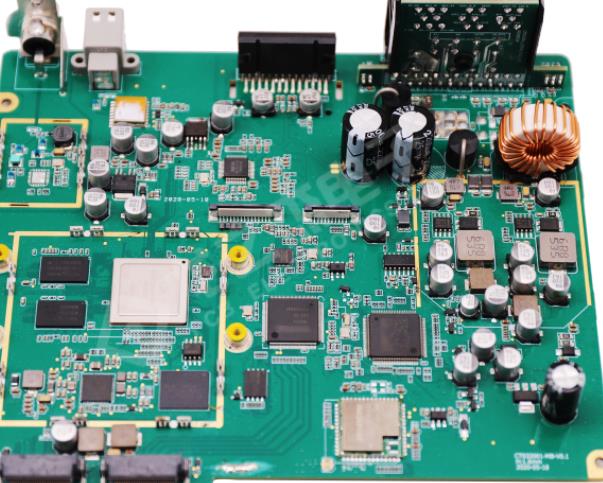
Reasons and Solutions for High Throwing Rate of SMT
SMT patch processing is in progress, and there may be throwing problems If it is within the normal range, this is a normal problem If the throwing speed value is relatively high, then there is a problem, then the production line engineer or operator should immediately stop the production line and check the reason for throwing, so as to avoid wasting electronic materials and affecting the production capacity Then, what is the reason for throwing the placement machine? Let me tell you how to solve this problem
1. Electronic material problems
If the electronic materials themselves are ignored in the PMC inspection, and the electronic materials flow to the production line for use, it may lead to new throwing, because some electronic materials may be squeezed and deformed during transportation or handling,
Circuit board
Or when they leave the factory There is a problem with electronic materials due to production. In retrospect, this needs to be solved through coordination with the electronic material supplier. New materials should be released and tested before use on the production line
2. Feeder position error
Some production lines are in two shifts, and some operators may feel tired or careless, leading to errors in the feeding station. Then, the mounter will throw out a lot of data and give an alarm. At this time, the operator needs to check and replace the feeder. Data station.
3. Reasons for picking position SMT places the machine
The placement of the placement machine depends on the suction nozzle on the placement head, which sucks the corresponding data in order for placement. Some throwing is caused by trolley or feeder, and the material is not at the suction nozzle or does not reach the suction height. There will be lots of empty stickers. In this case, it is necessary to calibrate the feeder or adjust the suction height of the suction nozzle.
4. The nozzle problem of the mounting machine
Some SMT machines operate efficiently and quickly for a long time, and the suction nozzle will be worn, resulting in data being sucked down or cannot be picked up, and a large number of throwing will occur. In this case, the placement machine needs to be maintained in time. Replace the nozzle frequently.
5. Negative pressure problem of mounting machine
The mounter can absorb components and place them, mainly relying on the negative pressure generated by the internal vacuum for suction and placement. If the vacuum pump or air pipe is damaged or blocked, the air pressure will be too low or insufficient, and the components will not be absorbed. Or drop during the movement of the placement head. In this case, the throw data will be added. In this case, the air pipe or vacuum pump needs to be replaced.
6. Visual recognition error of mounter image
The placement machine can install the specified components to the specified pad position, mainly due to the visual recognition system of the placement machine The placement machine visually identifies the part number, size, and component size, and then passes the placement machine The machine calculates and the components are installed on the designated PCB pad If there is dust or dust in the field of vision, or it is damaged, identification errors will occur, which will lead to errors in picking materials, resulting in new throwing In this case, you need to replace the visual recognition system
The above is the explanation given by the editor of pcb circuit board company.
If you want to know more about PCBA, you can go to our company's home page to learn about it.
In addition, our company also sells various circuit boards,
High frequency circuit board and SMT chip are waiting for your presence again.