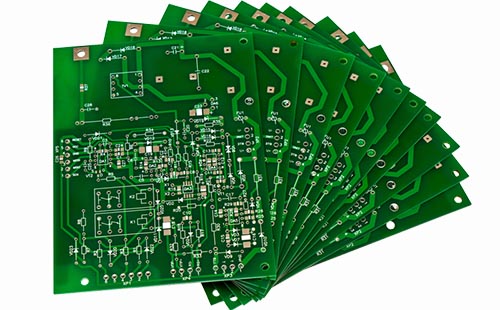
Detailed explanation of quality management measures for PCBA processing
The production process of PCBA is a complex process, which requires the coordination and cooperation of all departments from the determination of cooperation with customers, production materials to final product shipment. In the production process, due to improper operation of employees or equipment, it is easy to produce welding defects of products, so strict quality control measures are required in the processing process.
Quality Control Methods in PCBA Production Process
1. Make production documents and strictly check them
DFM manufacturability analysis of customer PCB, BOM, schematic diagram, 3D drawing, assembly manual and other documents shall be conducted, and the following items shall be checked one by one:
a) Document version number and last modification time
b) Process: environmental protection
c) Whether the marking of directional components on PCB screen is complete and clear
d) Whether the model, brand and silk screen of electronic components in BOM are complete and clear
e) Whether PCB manufacturing process requirements (substrate, number of layers, copper thickness, plate thickness, surface treatment, impedance, special through-hole method, etc.) are clear
f) Whether PCB wiring, windowing, splicing, solder mask, aperture and component layout are reasonable
g) Whether the patch coordinate file is complete and clear
h) IC program burning process (before production or after mounting)
i) Whether the material, size and special process are clearly marked in 3D drawings such as housing
j) Whether the requirements, standards and operation instructions of the assembly manual are clear and accurate
k) Whether the test plan is complete and clear
l) Customer's special process description
2. Conduct product introduction meeting
The meeting was attended by the marketing, project manager, procurement, engineering, production, PMC, quality and other departments to clarify the customer's background and process requirements, and document the places that need special attention in the order production process, so that all departments can better cooperate in the actual production.
3. Select a reliable PCB factory
Select high-end PCB production plants with abundant capacity, on-time delivery, stable quality, support for special process requirements such as multilayer boards, HDI, FPC, impedance, blind hole, etc., use Rogers A+grade base materials, equipped with high-end fully automatic copper sinking and drilling production lines, and 100% factory testing of all products to ensure the quality of PCB boards.
4. Select the primary component agent or trader
Establish a long-term and stable cooperative relationship with the top tier one electronic component agents to ensure 100% authentic purchase and reliability of components.
5. IQC incoming material inspection
The incoming materials of PCB circuit boards, electronic components, steel meshes and jigs shall be inspected to ensure that they meet the requirements of circuit electrical design and production process at the source and greatly improve the production quality.
6. Storage of sensitive components
Special constant temperature and humidity storage for sensitive components such as IC and BGA to ensure that they remain in a stable state is conducive to improving the reliability of later welding.
7. PCB, IC, BGA baking
Professional oven is used to bake PCB, important IC and BGA for 2-12 hours, which is convenient to remove the moisture on the bonding pad and pin, and can ensure the reliability in the chip welding process to the greatest extent.
8. Solder paste printing
Solder paste printing is critical to the entire welding process. Nordec will perform the following key controls:
a) Selection of solder paste: use industry famous brand solder paste (Qianzhu, Weitelian)
b) Solder paste mixing: fully stir the solder paste clockwise for 2-5 minutes with an automatic solder paste mixer until the solder paste reaches a filiform viscous state; Stirring charge
The distributed solder paste is immediately put into the production line for printing
c) Laser steel mesh: use the laser steel mesh of Musen and Guanghong brands, and fine tune the opening according to the engineering process to ensure the control of solder paste printing
d) Full automatic solder paste printing machine: Universal full-automatic solder paste printing machine of famous brand is used to automatically scan Mark points, adjust printing coordinates and detect the printing thickness of solder paste.
9. SMT patch
Seven full-automatic high-end SMT mounters, equipped with Samsung SM471/482/481, Fuji CP8/6 series, electric Feida feeding, perfectly achieve 01005 mounting accuracy, and support precision mounting of mainstream IC, BGA, QFN, PLCC and other components.
10.IPQC
Based on the BOM and process documents, the Quality Department checks the first product after SMT placement item by item to avoid material error, wrong direction and location, etc., and patrols the line to control the quality during the batch production process.
11. Reflow welding
Equipped with well-known brand Jintuo 16 temperature zone reflow welding, precise furnace temperature control, smooth furnace temperature curve, and effectively control the welding process. The engineering personnel shall use the furnace temperature tester to measure the reflow furnace temperature every 4 hours to ensure that the equipment operates normally.
12. AOI detection
100% of the PCB circuit boards that have completed reflow soldering have been inspected by AOI (optical detector), scanned and photographed, and compared with the preset PCB image to effectively prevent defects such as tin bonding, false soldering, false soldering, component falling off, and component inversion.
13. X-Ray detection
X-Ray equipment is equipped to conduct X-scan for PCB containing BGA, and detect whether there are defects such as BGA solder ball bonding, faulty soldering, solder ball falling off, bubbles and so on through equipment imaging to ensure 100% BGA welding effect. For BGA defective products, a professional third-party company will replant the ball through BGA repair bench, X-Ray detection and other processes.
14. DIP plug-in
Four DIP plug-in production lines, with a daily plug-in capacity of 100 points, are equipped with automatic track pull wire, foot shearing machine, shaping machine and other auxiliary tools. Worker training is normalized and special personnel are assigned to ensure plug-in efficiency and quality.
15. Wave soldering
New wave soldering equipment, accurate furnace temperature control (± 3 ℃). According to the requirements of PCB plates and components, adjust the furnace passing speed and gradient, select the corresponding flux, and use customized carriers for mass production to ensure the consistency and yield of welding. After the completion of the furnace, the PCB surface shall be cleaned by foot cutting, professional washing water and ultrasonic wave.
16. ICT test
The PCB designer is required to reserve test points on the board surface, make professional test jigs, perform ICT test on the welded PCB, connect external power supply and load, detect the voltage and current values between test points, ensure that the input and output are consistent with the designed test scheme, and thus detect the electrical continuity of the PCB.
17. Program burning
According to customer requirements, program burning is carried out for PCB, and mainstream burners such as J-Link and ST Link are supported. The production line is equipped with a computer host for assembly line operation.
18. Function test
After burning the program, connect the PCB board to the load, simulate the user's input and output, perform function detection on the PCB board, realize the joint debugging of software and hardware, and ensure that the front-end manufacturing and welding are normal.
19. Finished product assembly
It is equipped with 4 professional automatic product assembly lines, professional tools and auxiliary materials, and is assembled in strict accordance with the customer's assembly manual. The reasonable division of production areas, the setting of standard line edge material in and out and recording, effectively prevent wrong materials.
20. Aging test
Equipped with professional aging test stand, 100% product aging (aging method, time and environment shall be set according to customer requirements), independent aging area, and effective management.
21. Vibration test
For some PCB boards with vibration test requirements, a professional vibration tester shall be used for long-term test to ensure that the welding elements do not fall off. The sampling test proportion shall be determined according to customer requirements.
22. High and low temperature test
Customers with this test demand will equip their products with professional test rooms, and provide targeted testing services in common temperature areas such as - 40 ℃ to 100 ℃, fully simulate the environmental temperature of products, and maximize the reliability of products.
23.OQA
Set OQA post to check AQL items of final products before delivery, such as:
a) Appearance: check for scratches, marks and other appearance items
b) Whether the inner packing accessories are complete
c) Whether the product functions meet the design requirements
Ensure that 100% of the test is passed. If one piece is found defective, the whole batch shall be returned for full inspection until the problem is found and effectively improved. Generally, customers will also cooperate in QC spot check at this link until it reaches the standard.
24. Packaging logistics
According to the customer's logistics and transportation requirements, support the following packaging requirements for ex factory products:
a) Ordinary carton packaging
b) Pearl cotton protection (Grade 10 anti-static)
c) Independent packaging of products
d) Wrap wooden pallet for reinforcement
The above is the quality control method of PCBA production process. Only by strictly checking each link and process, can we create perfect products.