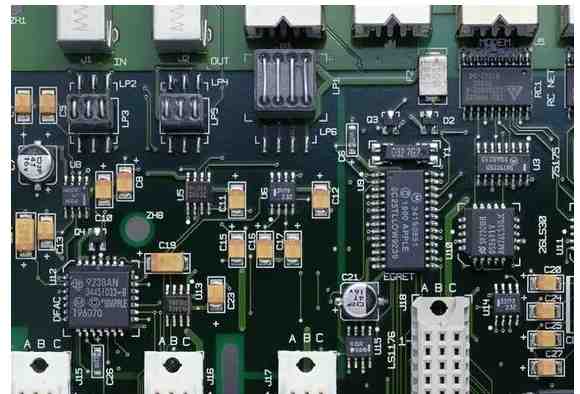
SMT is Surface Mount technology (short for Surface Mount Technology), known as surface mount or surface mount technology. It is a pin-free or short-lead surface assembly element (SMC/SMD, Chinese called chip element) mounted on the printed circuit board (PrintedCircuitBoard, PCB) on its surface or other substrate surface, by reflow welding or dip welding and other methods for circuit assembly technology.
Cause analysis and countermeasure of material loss in SMT processing
1, suction nozzle deformation, blockage, damage, insufficient vacuum pressure, leakage, resulting in suction can not afford, incorrect material, unqualified identification, throwing material.
The solution: The technician must check the equipment daily, test the NOZZLE center, clean the nozzle and maintain the equipment regularly as scheduled.
2, the spring tension is insufficient, the suction nozzle and HOLD are not coordinated, resulting in poor feeding;
Solution: Maintain the equipment regularly according to plan, check and replace the wearing parts.
3, Deformation of HOLD/SHAFT or PISTON, bent suction nozzle, short wear of suction nozzle, resulting in poor material extraction;
Solution: Maintain the equipment regularly according to plan, check and replace the wearing parts.
4, the material is not in the center of the material, the material height is not correct (generally 0.05mm after the part), resulting in deviation, incorrect material, deviation, identification system as invalid material discarded;
Solution: Maintain the equipment regularly according to the plan, check and replace the wearing parts, and correct the machine origin.
5, vacuum valve, vacuum filter element dirty, foreign matter blocked. The vacuum pipe channel is not smooth, the vacuum is insufficient when inhaling, and the equipment running speed leads to poor material extraction;
Solution: Technicians must clean the nozzle every day and maintain the equipment regularly as scheduled.
6, the machine positioning is not horizontal vibration, the machine and FEEDER resonance resulting in poor feeding;
Solution: Maintain the device regularly and check the horizontal retaining nuts.
7, screw, bearing wear loose, vibration during operation, stroke change, poor material extraction;
Solution: It is strictly prohibited to blow the inside of the machine with the air gun to prevent dust, debris and parts from being attached to the screw. Maintain equipment regularly according to schedule, check and replace wearing parts.
8, motor bearing wear, code reader, amplifier aging, resulting in changes in machine origin, inaccurate running data, poor material extraction;
Solution: Maintain the equipment regularly according to plan, check and replace the wearing parts, and correct the machine origin.
9, vision, lightning lens, suction nozzle reflective paper is not clean, debris interferes with camera recognition, resulting in poor processing;
The solution: The technician must check the equipment daily, test the NOZZLE center, clean the nozzle and maintain the equipment regularly as scheduled.
10, Improper selection of identification light source, insufficient aging luminous intensity and gray level of the lamp lead to poor processing;
Solution: Regular maintenance of equipment, testing of camera brightness and lamp brightness, inspection and replacement of wearing parts.
11, reflective prism aging carbon accumulation, wear scratches caused by poor treatment;
Solution: Maintain the equipment regularly according to plan, check and replace the wearing parts.
12, insufficient air pressure, vacuum leakage leads to insufficient air pressure, can not afford to take material or fall off in the way of the sticker after taking out; Solution: Maintain the equipment regularly according to plan, check and replace the wearing parts.
13, the deformation of the feeder extrusion each other, resulting in a change in the feeding position, poor material extraction;
Workaround: Require action.
14, the feeder gland deformation, spring tension is insufficient, resulting in the feeder spine gear stuck, do not roll and throw material, check and replace wearing parts.
15, the camera loose, aging lead to identification of poor throwing material; Solution: Maintain the equipment regularly according to plan, check and replace the wearing parts.
16, the feeder spine gear, drive claw, positioning claw wear, electrical poor, feed motor poor resulting in poor feed or feed poor;Check for replacement of vulnerable parts.
17, Machine feeding platform wear leads to loose installation of FEEDER and poor feeding;
Solution: Maintain the equipment regularly according to the plan, check and replace the vulnerable parts. Other special parts that need deceleration mounting do not decelerate mounting, which will also cause underground suction rate.Countermeasures: Feed deceleration, X/Y/H axis deceleration or adjust each action with timing control.