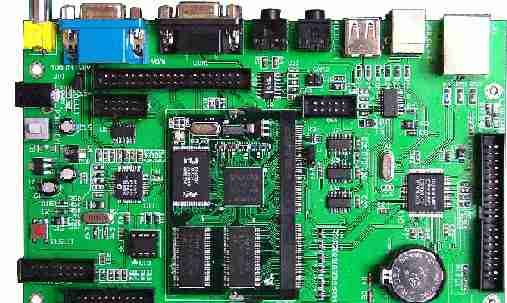
SMT (Surface Mount technology) patch processing requires the use of a variety of equipment and tools, the following are some common equipment:
1. SMT mounter: It is used to accurately attach SMT components to the PCB, including automatic mounter, semi-automatic mounter and manual mounter.
2. Through the hole equipment: including automatic drilling machine, riveting machine and gold sinking machine, etc., used for PCB through the hole processing.
3. Hot air welding equipment: including hot air gun and reflow welding furnace, etc., for welding SMT components on PCB.
4. SMT component storage rack: used to store and organize SMT components.
5. 3D AOI inspection equipment: used to check the placement and quality of SMT components.
6. Coating equipment: including automatic coating machine and manual coating machine, etc., for coating the glue on the PCB surface.
7. Solder paste printing machine: used to print solder paste on the PCB for use in the subsequent welding process.
8. Soldering soldering equipment: used for welding large components, such as connectors, sockets, etc.
9. Cutting machine: used to cut the PCB after the patch into a single board.
10. Cleaning equipment: used to clean the PCB after the patch to remove the glue and solder paste that may remain.
SMT processing
The above are some equipment commonly used in SMT patch processing, but the specific equipment and tools need to be used, but also according to the actual situation and process requirements to decide.
kingford has its own SMT processing plant, which can provide services for 0201 components in the smallest package. The SMT plant is equipped with 3 Fuji high-speed SMT lines, 2 DIP plug-in production lines, equipped with AOI optical detector, automatic solder paste printing machine, semi-automatic solder paste printing machine, lead-free wave soldering, lead wave soldering, upper and lower 8 temperature zone reflow welding, PCBA functional test frame, aging, board loading machine, cleaning tools, etc., at the same time, a professional research and development laboratory is set up. Five professional engineers cooperate with customers to perform general functional testing, test point testing, as well as channel, noise, waveform, drop and temperature testing.
PCBA processing soldering soldering soldering reasons may include the following aspects:
1.Solder alloy performance: Solder alloy needs to have good wettability and fluidity, so that the solder liquid can wet and fill the weld during the welding process, so as to form a complete welded joint.
2. Peak height and cycle: the choice of peak height and cycle also has a great impact on welding quality. Reasonable matching of peak height and period can make the time and degree of solder liquid wetting element solder joint surface reach the best state, so as to form a good welding joint.
3. Component solder joint design: The solder joint design of the component will also affect the quality of the welded joint. Reasonable solder joint design can increase the contact area of the welded joint, improve the welding strength and stability.
4. Welding process parameters: The selection and adjustment of welding process parameters will also affect the quality of welded joints. For example, the adjustment of parameters such as welding temperature, welding speed, crest height and period can achieve the best wetting and filling effect of welded joints.
In the process of PCBA wave soldering, if there is a tin connection, corresponding measures need to be taken to deal with it, the common methods are as follows:
1.Adjust the welding process parameters: properly adjust the welding process parameters, such as welding temperature, crest height, period, etc., to reduce the wetting time and wetting degree during welding, and prevent the solder from forming a tin on the solder joint of the component.
2. Replace the solder alloy: try to replace other solder alloys with better wettability and fluidity to make the welding process more stable and reduce the possibility of tin connection.
3. Replace components: Some components themselves have poor wettability, easy to appear tin phenomenon, you can consider replacing other components with good weldability.
4. Check the surface treatment of PCB board and components: Improper surface treatment of PCB board and components can also easily lead to the occurrence of tin phenomenon, you can check whether there is oil, oxidation and other problems, timely cleaning and treatment of the surface.