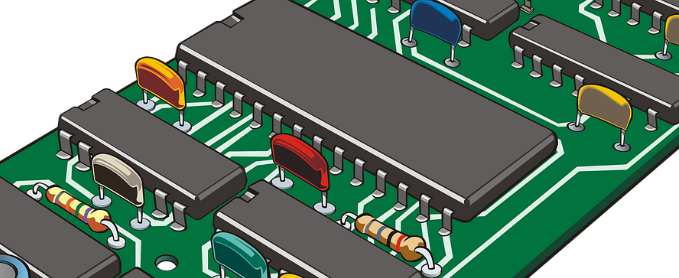
Traditional stiff-flexible plates are composed of rigid and flexible substrates pressed together by selective strata. The structure is tight, forming conductive connections with metallized holes. Mario Amalfitano, International Sales Manager at Aero Flexible Ciruitry in Torrance, California, commented: "If you have components on both the front and back of the board, rigidness and torsion is an excellent choice. However, if all the components are on one side, it is more economical to choose a double-sided flexible plate and layer a layer of FR-4 reinforcement material on the back. The FR-4 does not form an electrical connection to the metallized hole or an effective flexible PCB circuit, but only serves as a reinforcement. This increases reliability and reduces breakage during the manufacturing process or during the installation of components, or after the installation of components."Amalfitano recommends that manufacturers try to keep the number of layers as low as possible, taking into account reliability and price considerations.
The flexible PCB circuit industry is in a small but rapid development. Polymer thick film process (PTF) is an efficient and low-cost process for PCB production. The process is to selectively screen print conductive polymer inks on an inexpensive flexible substrate. Its representative flexible substrate is PET. PTF conductors include silk screen metal filler or toner filler. The PTF itself is very clean and uses lead-free SMT adhesives without etching. Al Hollenbeck, technical director of Poly-Flex, R.I. Cranstom, said: "PTFPCB circuits are ten times cheaper than copper Kapton PCB circuits because of the addition process and the low cost of the substrate. 2-3 times cheaper than PCB. PTF is especially suitable for the control panel of the device, because it is low cost, and it is easy to assemble and change under the flat graphics panel. In mobile phones and other portable products, PTF is suitable for converting components, switches and lighting devices on PCB motherboards into PTFPCB circuits. It saves costs and reduces energy consumption."
There is also a hybrid structure of flexible PCB circuit, which is also a multi-layer board, but the conductive layer of the multi-layer board is composed of different metals. Located in Carlsba, California
"An 8-layer board uses FR-4 as a medium for the inner layer and kapton as a medium for the outer layer, with leads extending from three different directions on the board, each of which is made of a different metal," says Jack Lexin, application engineer at L.E.lex Circuits, Inc. Constantan alloy, copper and gold are used as separate leads. This hybrid structure is mostly used in the case of low temperature where the relationship between electrical signal conversion and heat conversion and electrical properties are relatively harsh. In this case, flexible hybrid PCB circuits are the only viable solution.
Whether the composition of these flexible PCB circuits is cost-effective and whether it is best utilized can be evaluated by the convenience of the connected design and the total cost. George Serpa is a contract producer for Flextronics International in San Jose, Califonia. As a senior product development engineer, I know a lot about flexible assemblies." The overall way of interconnecting is not the same, the mobile phone is a block layout; Portable computer is X-Y orientation positioning layout; The printer is rigid-torsion PCB format. These products are made of different materials at different prices to reduce the cost of each inner lead. Each design is typologically evaluated to achieve the best price/performance ratio."
If the design of the PCB circuit is relatively simple, the total volume is not large, and the space is suitable, the traditional internal connection method is mostly cost-effective. If the circuit is complex, handles many signals, or has special electrical or mechanical properties requirements, flexible PCB circuits are a better design choice. "PCBS should be preferred if possible," says Tim Patterson, design and development manager at Smartflex in Tustin, Califonia. It's especially cheap to use multiple layers. When the size and performance of the application exceed the capability of the PCB, the flexible assembly method is the most economical choice. Flexible PCB circuits with 5mil aperture, 3mil lines and pitch in 12mil pads can be made on a single film. Therefore, it is more reliable to mount the chip directly on a thin film, such as a polyimide film. Because they do not contain flame retardants that can be a source of ion contamination. These films may be protective and cure at higher temperatures, resulting in a higher glass transition temperature." Another potential cost saving reason for flexible materials over rigid materials is the elimination of plug-ins.
The high cost of raw materials is the main reason for the high price of flexible PCB circuits. "The price of raw materials varies considerably," says Joseph DiPalermo, application engineering manager at Parlex in Methuen, Mass. The lowest raw material cost of polyester flexible PCB circuit, PCB cost is 1.5 times of the raw materials used; High-performance polyimide flexible PCB circuits are up to 4 times or more. At the same time, the flexibility of the material makes it difficult to automate processing in the manufacturing process, resulting in a decrease in output; In the final assembly process, defects are prone to occur, including the stripping of flexible accessories and line breakage. This kind of situation is more likely to happen when the design is not suitable for the application. In the case of high stresses caused by bending or forming, it is often necessary to choose reinforcing or reinforcing materials. Although the material is more expensive and troublesome, DiPalermo believes that folding, bending and multi-layer panel function will reduce the overall component size, the material used will be reduced, and the total assembly cost will be reduced.