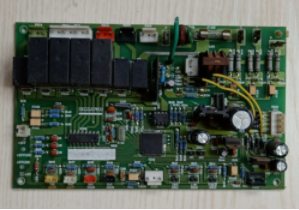
Problems needing attention in PCB wave soldering process
Wave soldering is a batch welding process for manufacturing PCB circuit boards, mainly used for through hole components welding.
1. There is green oil in the element hole, leading to poor tin plating in the hole. The green oil in the hole should be kept below 10 percent of the hole wall and the number of holes in the internal green oil should be below 5 percent.
2, leading to poor tin plating in the hole may be too small coating thickness.https://www.kingfordpcb.com/yuan.php
3. The coating thickness on the component hole wall is not enough, resulting in poor tin plating in the hole. Generally, the thickness of the pore wall should be above 18 microns.
4. The hole wall is too rough, resulting in poor tinning or pseudo-welding in the hole. 5, the hole is wet, resulting in pseudo welding or bubbles. Packaging the PCB when it is not dry or cooled, and leaving it for a long time after unpacking, etc., will result in moisture in the hole.
6. The main factor leading to welding failure may be that the hole size is too small, the parts can not be inserted into the hole, or the positioning hole is offset, the parts can not be inserted into the hole.
Use your eyes to observe the appearance of the circuit board, such as thickness, size and so on whether it meets the requirements, if it does not meet the need to remake, with the circuit board market competition is becoming more and more fierce, some manufacturers in order to save costs, the use of some low plate, more or less there will be scratches and cracks phenomenon, the performance of the board will have a certain impact.
2. First of all, it can be used normally after the installation of components, which requires the circuit board without short circuit and open circuit. The factory has an electrical testing process in production, which is to detect whether the board has short circuit. At the time of patch welding, it is necessary to check whether the pad falls off under the condition of high temperature, resulting in no welding. In addition, the high temperature resistance of the board is also very important. An important index of the board is the TG value. When making plates, engineers need to instruct the board factory to use the corresponding board according to the requirements of different service conditions.